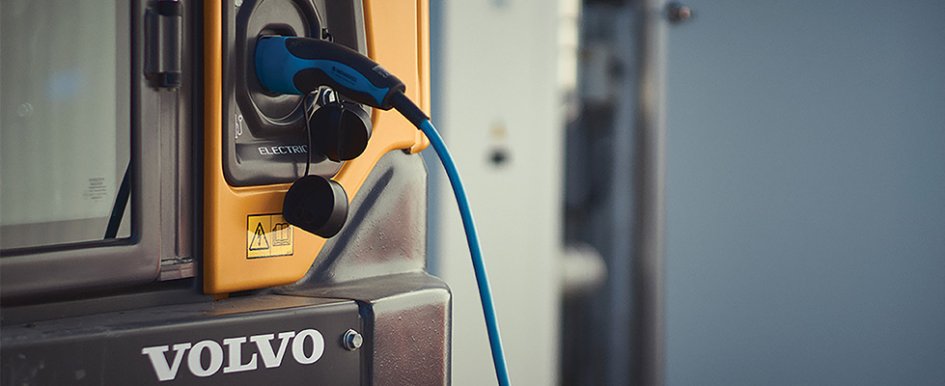
While many in our industry remain hesitant about electric heavy equipment, the machines are quietly but undeniably proving themselves on pilot tests and real jobsites.
Questions and concerns around how to charge, how long that charge will last and how the higher purchase price is recouped are all fair. But compact electric machines have been proving their worth for several years now, and the larger machines are not far behind. Let’s take a look.
Calming Charging Concerns
Charging is obviously a huge piece of the electrification puzzle, and there are more solutions than many people realize. Of course, there is the standard grid charging using outlets at your “home base.” Different types of outlets will take different amounts of time to power a machine, but they get the job done.
We’ve seen — and will continue to see — announcements about original equipment manufacturers (OEMs) and battery or charging solution providers entering partnerships, establishing joint ventures or making investments to further electrification efforts.
Another key factor for better charging is getting our infrastructure up to speed. The machines and charging units are developing quickly, but there is still work to do on the grid that supports them. Governments and trailblazing companies remain essential for moving this forward.
Making a Charge Last
The general rule for battery life is that the harder the task is, the faster a battery will run down. For example, cutting and grading with an electric excavator will affect battery life differently than moving a few buckets of dirt.
However, one of the biggest perks of electric equipment is that it doesn’t idle when it’s not in use. Most electric machines will turn off when the operator stops for a few seconds, and they can start right back up to provide immediate power. When you consider that diesel machines can spend 40% to 50% of their shift idling, this is a big deal for both battery life and resale value down the road.
That said, many models available today will benefit from a top-off over the lunch break or other pause in work (also called “opportunity charging”). This can often allow a machine to work a full eight hours — and again, this means actual operating hours with no idle time. It is important for contractors to size the machine and charging cycles to the tasks.
One such example comes from Coastal Waste & Recycling in Florida. They’re using a 23-ton Volvo EC230 Electric excavator to process up to 100 tons of construction and demolition debris and green waste each hour. They use it for four to five hours, give it a quick charge and then use it on another shift, allowing them to get a full day’s work out of the machine.
Keep in mind that most electric heavy equipment uses lithium-ion (Li-ion) batteries, which are far superior to the old lead-acid or nickel-cadmium technology some people may be more familiar with. Li-ion batteries offer triple the energy density, double the battery life, consistent performance, no memory effect, faster charging and no maintenance.
Justifying a Higher Price
Electric machine prices are higher than those of their internal combustion equivalents but — as with any new technology — this will improve as the supply chain strengthens and adoption grows. In the meantime, there are four additional factors in the cost equation.
- Maintenance — There is almost none! Because there’s no engine, diesel exhaust fluids and engine oil and air filters aren’t needed. There is no difference in the maintenance of nonelectric components (e.g., grease for joints) or ground engaging/wear items. Technicians will need to be trained on the electric components, especially regarding safety. It may feel like a big shift at first, but it’s just like when telematics and in-cab displays became more prominent. Once you have the knowledge, it becomes fairly simple. And don’t forget: No more buying and hauling fuel. The time and cost savings around uptime can counteract that purchase price pretty quickly.
- The ability to win more jobs — When you can significantly reduce noise and emissions on a jobsite, customers appreciate it. Consider that a difference of 10 decibels is perceived as twice as loud to the human ear. (Side note: Less vibration also makes operators happier and allows them to talk over the machine. Compact electric machines are proving themselves valuable for work like indoor demolition, food production, landscaping, any kind of night work and so much more. And larger machines are coming out of pilot tests with some impressive results too. Simply put: Having electric equipment in your fleet will put you ahead of the competition.
- Financial incentives and flexibility — Depending where you work, you could benefit from tax incentives or grants that prioritize carbon reduction. Your dealer and/or OEM can help you find these. And, since the tech is still relatively new, many manufacturers are offering flexibility in terms of buying, leasing or renting so you can try before you buy.
- Total cost of ownership — It’s important to consider all the factors that can cost or save dollars over the entire life span of your electric machine. The elimination of fuel, the reduction in maintenance, the ability to win new work and potential incentives can quickly make up for the higher purchase price.
For example, construction giant Skanska recently completed a 90-day pilot project with the Volvo EC230 Electric excavator, loading trucks of export material from an underground tunnel as part of a transit line renovation in Los Angeles. All things considered, the machine reduced hourly costs by 74% and hourly carbon emissions by 66%.
In another 90-day pilot in California, this time collaborating with Sunbelt Rentals, the machine delivered an 83% cost savings and an 80% carbon reduction rate in comparison to its diesel equivalent. Numbers like these will be hard to ignore for companies and governments looking to reduce emissions while being fiscally responsible.
The Proof Is in the Power
So far, nonconstruction industries are adopting electric heavy equipment faster because they have more incentives or regulations to do so, and because they may have simpler charging situations. What we learn from them — and the solutions that develop as a result — will make electric more viable in the construction segment.
We also have to keep in mind that the approach to making our industry more sustainable isn’t a single technical solution, but rather a variety of options we’ll need to develop and integrate into our operations (like hydrogen, hybrid, renewable fuels and more). As long as we keep working together toward the end goal, there is no wrong way to get there.