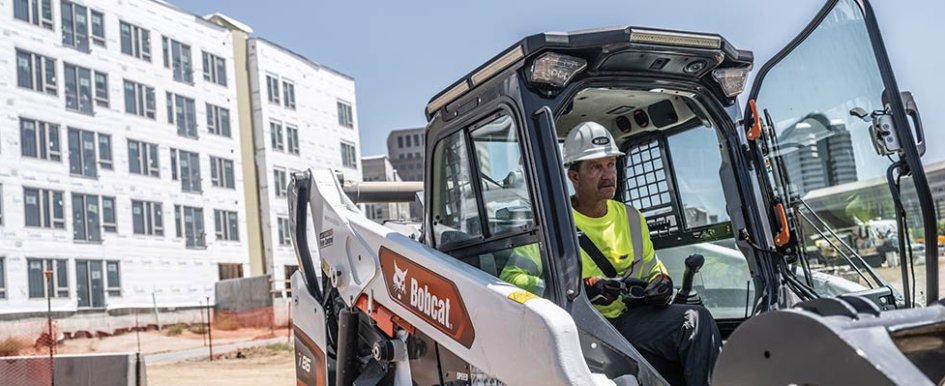
Today’s equipment operators and project managers are looking for ways to be more efficient and productive on the jobsite. Efficiencies can be achieved in a variety of ways, including using advanced technology to reduce the number of employees working on one task, selecting versatile equipment that can utilize multiple attachments for different applications, and following proactive maintenance schedules to improve the longevity of your machine and reduce unexpected downtime.
Today, operators can also benefit from utilizing a non-DPF engine while still meeting Tier 4 regulations. Tier 4 regulations are U.S. Environmental Protection Agency (EPA) emissions standards for diesel-powered construction equipment to reduce
harmful exhaust gases. Let’s take a closer look at what non-DPF means and how it translates to efficiencies and productivity on your jobsite.
What Does Non-DPF Mean?
A diesel particulate filter (DPF) is an aftertreatment system that takes the exhaust created by the engine and cleans it. It is typically used in diesel engines to meet emissions standards by capturing and storing exhaust soot and particulate matter in an effort to reduce air pollution.
Today, some equipment manufacturers have designed and are using engines that meet Tier 4 emissions standards without the need of a DPF, hence the name “non-DPF engines.” There is no waiting for equipment regeneration, which can lead to downtime or cause your machine to underperform while the regeneration process takes place. This also means there are no maintenance requirements typically associated with a DPF that can prove to be costly over the life of the machine, saving owners money.
What Is Regeneration?
Regeneration is the process of periodically removing soot from the DPF, a component that helps filter exhaust emissions from diesel engines. This self-cleaning process can take up to 30 minutes and increases exhaust temperatures to burn off/eliminate the soot from the walls of the DPF, and in severe instances, the equipment may even go into an idle state to prevent further damage. This can happen if a filter becomes increasingly clogged, leading to reduced engine power, decreased fuel economy, increased exhaust emissions and eventually engine damage due to excessive back pressure in the exhaust system.
During regeneration, customers may experience slower cycle times and potentially limited functionality depending on the manufacturer and the task at hand. Additionally, if an operator delays a regen cycle too many times, it can lead to other, larger maintenance issues for the machine. Passive regen is activated by the equipment when it’s working hard, while active regen requires system or operator action.
Benefits of Non-DPF Engines
Equipment operators with non-DPF engines avoid downtime associated with DPF regeneration and are at a minimized risk of long-term DPF maintenance costs. Non-DPF engines have more efficient fuel utilization and can also be more operator friendly.
As you consider your next purchase of compact equipment, consider the DPF versus non-DPF information shared above. Better yet, talk to your local dealer about the benefits of a non-DPF engine and how this one feature can save you both time and money in the long run