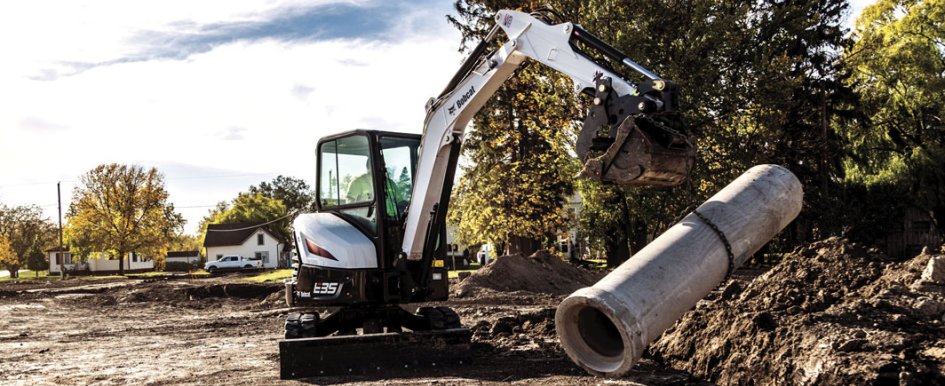
Lifting freely suspended objects with compact excavators demands preparation, special care and proper operator training. If correct lifting practices are not routinely followed, it may cause project delays and create machine instability, due to the additional stress being placed on the machine. This can lead to unnecessary downtime.
1. Examine the jobsite and level slopes.
Operators are responsible for all jobsite- and lift-related conditions and need to respond to condition changes that have the potential to create hazards. These might include machine condition, strength of the surface beneath the excavator and method of moving the load.
Before lifting, an operator should examine the area around the excavator to ensure there is nothing above or below the machine that could cause interference. When working on a slope, level the work area, if possible.
If leveling the work area is not an option, position the excavator with the blade downhill and lowered, and avoid working with the tracks across the slope or swinging the bucket in the downhill direction.
Always keep the boom centered and the load as low to the ground as possible for maximum stability. Move as slowly as the task allows and avoid sudden changes. Never travel on a slope measuring greater than 25 degrees.
2. Know your lifting capacity.
All excavator operators should understand that an excavator’s lifting capacity is limited by one of two factors: hydraulic limitations or tipping limitations.
“Hydraulic limited” means the excavator is governed by its hydraulic power to lift a load. “Tipping limited” means there is a point at which the excavator begins to lift off the ground when lifting a load.
Manufacturers test excavators to determine how much weight they can safely lift at various heights and distances from the centerline of the machine. Based on that information, they then create lift charts, which are printed in the owner’s manual or posted within sight of the operator, such as on a decal located in the cab.
To maximize the life of the equipment and minimize machine wear, always make sure you and your operators follow the guidelines in the lift charts and do not exceed the machine’s recommended lift capacity.
3. Correctly interpret the lift chart.
Even though lifting material with an excavator may seem simple to the experienced operator, it is always important to follow the excavator lift chart, as it designates the proper lifting capacity at any one lift height and swing radius. At the top of the lift chart is the machine’s configuration information.
There may be several lift charts for an excavator, based on combinations of boom length, arm length, counterweight size and track-shoe width. Some manufacturers will include the bucket size in the lift chart.
If the manufacturer includes a bucket in the lift chart, the company will indicate the bucket’s weight. However, if the lift chart does not include the bucket details, it is up to the operator to know how much weight is on the end of the machine. This may include the weight of a coupler or bucket, the lifting apparatus itself and the weight of the material or item being moved.
It is important to note that capacities typically marked with an asterisk on the lift chart are limited by the machine’s hydraulic capacity and do not exceed 87 percent of the machine’s hydraulic lift capacity, as defined by the International Organization for Standardization (ISO).
Similarly, rated loads without an asterisk are limited by the machine’s stability and do not exceed 75 percent of the tipping load capacity.Next, determine the lift-point height, which is typically located in the far-left column of the lift chart.
The lift point refers to the distance from the ground to the bucket pin, not from the ground to the object you are lifting. When measuring the lift point height, consider how high or low (if below ground) you will need to lift the item, including the height of the item itself, the length of the lifting device, and at what height you want to place the item on a transport device.
After determining lift point height, examine the lifting radius from the centerline of the swing point. This distance is typically shown in the top row of the lift chart. The lifting radius is dependent on whether you are lifting over the front of the excavator or squarely over the side.
Additionally, if you are operating an excavator with outriggers or a dozer blade, you must reference the portion of the lift chart that reflects its position during excavation.
Once you have determined the lifting radius, find the cell on the lift chart where the lift point height and radius intersect. The number shown is the excavator’s rated lift capacity in pounds and/or kilograms. If the cell is blank, the excavator has no lifting capacity at that point, and lifting should not be attempted.
4. Consider pick-and-carry precautions.
When traveling on or moving an excavator with a suspended load is necessary, it is recommended to use a safety lifting device, such as an excavator lift eye. But first, the lifting apparatus should be approved for the weight of the material, and operators should know how to properly hook the lifting apparatus to the material or object being moved.
Before attempting to pick and carry a load, align the boom with the forward direction of machine travel. Maintaining this boom position when turning the machine is best for stability. Operators should only turn when necessary, at the slowest speed possible and with a wide turning radius.
Other tips for pick-and-carry applications include:
- Use the shortest lifting radius distance possible for the task.
- Keep the load as close to the ground as conditions permit.
- Attach strong ropes, otherwise known as tag lines, to prevent the load from swinging back and forth.
- Travel at speeds predetermined by jobsite conditions.
- Avoid sudden starts and stops.
5. Make use of operator training courses.
Some manufacturers offer mail-order or online excavator-training courses. And some equipment manufacturers have in-person training opportunities.
Having your operators take one of these courses can be beneficial in helping to avoid typical operator problems. Ask your equipment dealership what training options are available for your machines.