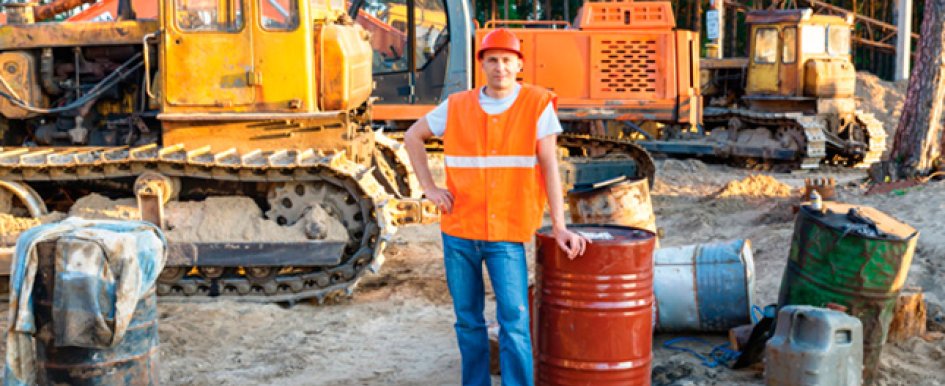
Fuel efficiency isn't only for commuters. It's a growing part of evaluating heavy equipment such as excavators, wheel loaders and articulated dump trucks. Whether you're monitoring fuel costs on a monthly or annual basis, fuel plays a fundamental role in your operation that can directly impact your bottom line.
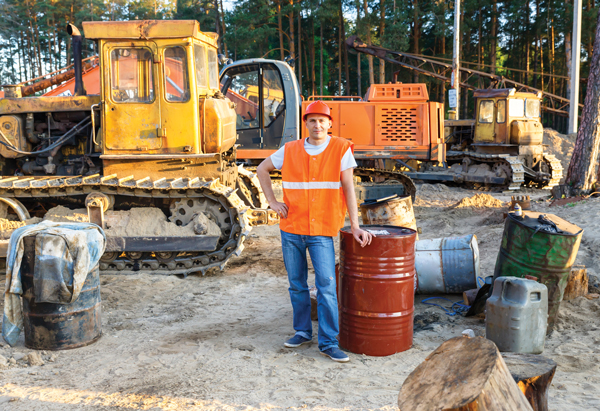
With diesel prices reaching more than $4 per gallon in some areas of the country, your company's profit potential is directly tied to its fuel consumption rates. One excavating and construction contractor estimated recently that his fuel costs are between 20 to 30 percent of annual equipment expenses, ranking second only to depreciation and leasing costs. Unfortunately, you have little to no control over the cost of diesel fuel. While you may be able to lock in prices through a bulk contract vendor to better manage price fluctuations, the price is ultimately controlled by market forces.
Improvements to diesel engine emission treatments and heavy equipment designs provide for greater efficiency—the ability to burn 2 gallons less of fuel per hour can add up to nearly $2,000 per month. That money could be put toward a machine payment. Consider these five steps to increase fuel efficiency in your fleet:
1. Identify fuel-efficient designs
Commit to machines with built-in fuel efficiencies. Improvements such as automated idling functions, power optimization systems, advanced transmission and hydraulic systems, programmable engine control units and sight gauges that monitor fuel efficiency by the minute can all contribute to more economical operation.
Changes in diesel engine technologies related to federal emissions compliance have prompted the development of high-pressure common-rail fuel delivery systems. These advanced fuel injection designs regulate fuel pressure and injection timing, and transform fuel into extremely fine mist as it leaves the injectors. In addition to creating cleaner exhaust, when fuel combusts more thoroughly less fuel is needed to run the engine, resulting in improved fuel economy.
2. Embrace new monitoring technologies
New machine intelligence and telematics are becoming standard with most manufacturers' machines. These GPS-based programs allow owners to monitor operational data and make recommendations to operators to improve machine-usage parameters, including fuel efficiency. From your computer or other Internet-enabled device, you can typically access a website to see if an operator lets a machine idle or is turning the engine off to save valuable diesel fuel.
Operational data and critical reports that track usage also provide insight into the machine's fuel efficiency related to different applications. Fuel levels for each machine can be reviewed remotely, eliminating the need to visit each machine to check fuel levels and minimizing trips for fuel trucks.
3. Spec the right bucket
Because an excavator's bucket is typically its biggest revenue generator, its size and capacity are important factors for productivity.
However, the right excavator or wheel loader bucket also has a direct correlation to fuel efficiency. A too-large bucket carrying overly heavy loads increases vehicle drag, and the extra weight decreases fuel efficiency.
A bucket properly matched to its material and equipped with adequate lift capacity and dump height could reduce the number of passes needed to fill trucks.
A proper match starts with the type of material you're handling. Once you've determined daily production targets, calculate the density of the material you'll be working with and match it to the size and capacity of the bucket you'll need to get the job done efficiently. Specifying the bucket first will help you identify the necessary machine size.
4. Set operator expectations
Operators have a direct relationship with assets that impact fuel efficiency and cost, so it is important that they understand the role fuel consumption plays in the costs of ownership and the company's overall profitability. Properly trained operators can help owners save money.
Operators should try to avoid aggressive acceleration, speeding, excessive travel and extended idling. Factoring in travel aspects, such as congested work sites and the location of material staging areas, can help reduce travel time and fuel usage. Machine features like automatic shutdown help save fuel during nonworking conditions. When enabled, the feature will shut down the excavator's or wheel loader's engine after a preset idle time. In some states, like California, automatic shutdown helps meet idling regulations for off-highway machines.
5. Calculate fuel usage
If you're not sure how your fuel consumption will work out, try projecting your fuel costs with an easy formula. Multiply a particular machine's consumption rate by the cost per gallon. Multiply that per-hour cost by the total number of hours you plan to operate the machine. Although this estimate will provide a fairly accurate idea of consumption, it's important to recognize that various applications can have considerably different consumption rates. The fuel consumption rate also depends on several factors including the engine size, equipment condition, operators' habits, the load, environmental conditions and the machine's design. Finally, monitoring a machine's fuel usage can signal the need for routine maintenance that will keep the machine running more efficiently.