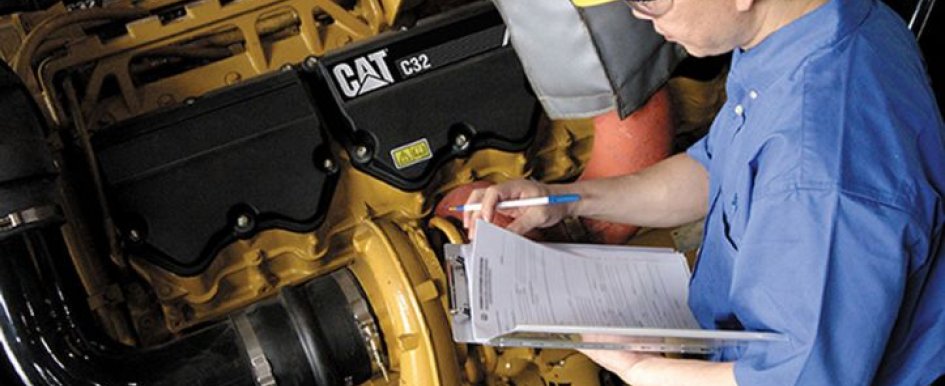
A contractor’s equipment fleet consists of tools that get the job done, which enables the company to get paid. Whether the fleet is one- or 1,000-strong, replenished with new or used equipment, and sees high or low utilization rates, a productive machine is core to the business’s success.
Equipment operating costs can vary greatly due to a variety of factors, including the severity of the application, how often the equipment is used and the amount of respect with which the operator treats the equipment. One critical owning/operating cost well within the control of the company—how well the equipment is maintained—can be the difference in operating costs of just under $1 per service hour or more than $7 per service hour.
“Our data shows that nearly 90% of machine failures are avoidable,” said Mike Scott, senior parts and service marketing consultant for Caterpillar.
Dave Matranga, also a Caterpillar senior parts and service marketing consultant, added, “If a contractor addresses an equipment problem indicator early enough prior to failure, the fix can be scheduled, should cost less to repair and can extend the life of other supporting components. If the issue is left to fail, repair costs are significantly greater than if the issue is dealt with earlier.”
Other than the unexpected failure, a contractor is in control of the interval and where the piece of equipment will be repaired or rebuilt. There may be some extenuating circumstances in which the contractor has to or chooses to run the equipment to failure, knowing full well that the repairs will cost more.
This is where developing a strong contractor-dealer relationship is critical for a company. Even before the first bucket of earth is excavated or the first wrench is turned on the machine, the contractor should consult with the dealer and explain the type of work anticipated, how strenuously the equipment will be used and how many life cycles are desired for the piece.
“It’s no longer a one-size-fits-all world,” said Tim Totten, solutions consultant for Caterpillar. “A variety of work factors should be included in the decision-making process, and the dealer offers a wealth of knowledge pertaining to equipment capabilities and specific market characteristics to help select the right model.”
Troublesome Indicators
The reality of owning and operating construction equipment is that it will require maintenance throughout its life. The level to which the equipment is serviced will ultimately be determined by the owner. There are different types of indicators to alert the owner that the equipment requires attention.
Planned indicators are within the company’s control to effectively and efficiently address, and one of the most common planned indicators is for maintenance performed by service meter units. The equipment’s operating and maintenance guide offers general guidelines for these intervals based on the number of hours.
Routine oil and coolant system fluid sampling offers insight into internal component wear and potential failure. The data gives important trends for these closed-loop systems and allows contractors to plan for component repair or rebuild. “Think of it like an annual blood test,” said Matranga. “Much like abnormal findings in bloodwork need to be either monitored or addressed, trends like increased metal fragments in the oil give an owner the data necessary to make a proactive service decision.”
Problem indicators, on the other hand, show up during operation, signaling that there is something failing within the machine. There are several different indicators, as Scott explained. “Items like black, blue or white smoke, increased oil consumption and overheating are all engine repair indicators; while brake slippage, vibration and leaks indicate a problem with the machine’s final drive,” he said.
Machine telematics data also can serve as an advanced warning problem indicator. In addition to machine utilization and location information, original equipment manufacturer (OEM) reporting programs capture data and give key personnel advanced warning about the condition of the equipment.
These problem indicators alert equipment operators and owners that a repair should be made soon, or an unexpected downtime event will occur. Whether and when these items are quickly addressed is up to the owner, but overwhelming evidence shows that repairing a machine problem before failure is significantly less expensive than waiting until after failure.
Repair Before Failure
There are worse negatives than higher costs associated with waiting until a failure to address a problem.
“High costs associated with repair after failure will often lead customers searching for lower replacement component cost alternatives,” said Totten, “which may lead to other problems down the road.”
Most manufacturers build equipment to last multiple lives. There are several levels of parts that will require repair or replacement at different intervals throughout the equipment’s service life. Typically, the higher the level of part that requires repair, the higher the cost.
- Level 1—designed to wear and are not reusable. These include engine piston rings, exhaust valves, gaskets and seals. For the drivetrain, they include seals, gaskets and anti-friction bearings.
- Level 2—wear at a slower rate and are designed to be reused at a rebuild interval. These parts include the pistons, intake valves and fuel injectors/nozzles in an engine, as well as the drivetrain’s plates, discs, gears and shafts.
- Level 3—designed to last the lifetime of the machine unless there is a component failure. Examples of these parts include the engine’s block castings and crankshafts and the drivetrain’s transmission cases and final-drive planet carriers.
“Once you start replacing Level 2 and 3 parts, the opportunity for the lowest cost per hour and lowest operating cost is lost,” said Scott.
Matranga offers an example of service costs for a wheel loader to illustrate just how costly it is if repairs are not made before failure.
“The average overhaul time period for a medium wheel loader is approximately 14,000 hours and will cost approximately $12,000 to service if repairs are made before failure. This equals a service cost per operating hour of 86 cents,” he said. “That same contractor could choose to ignore the planned and problem indicators and possibly extend the machine to 20,000 operating hours before overhauling the loader after failure. The projected cost for repairs, since Level 2 and 3 parts would have to be involved, jumps to nearly $53,000, or $2.64 service cost per hour.”
Carefully Consider Alternatives
As diverse as the reasons for why, when and where the machines are repaired, is the wide range of factors contractors have to consider before purchasing parts for the equipment. Some select solely OEM parts to get the maximum warranty coverage and life out of the part. Others are cost conscious, looking for a quick and convenient fix to get the machine running, and will look for an aftermarket solution. Many contractors fall somewhere in between these two extremes.
“Contractors will often look at where they are in the life cycle of the particular machine,” said Totten. “They will consider how much and how often it’s used and how long before selling off. If it’s not a machine that is heavily used or relied on and they are not holding on to it, then they may go with an aftermarket part.”
However, Matt Reeves, marketing and brand manager for Yellowmark, a Caterpillar brand, offers this caution about will-fit aftermarket parts: “While it’s true that will-fit parts are made to fit, they have not been developed to operate as part of the manufacturer’s system components and may not be built to the same standards or offer the same tolerances.
This holds especially true for machine components that receive high stress and high day-to-day use. Contractors may not get the expected life span out of the part, or, worse yet, the part could lead to the failure of other components in the system.”
A growing trend among OEMs is to offer a “value line” of replacement parts that falls in between genuine OEM parts and will-fit aftermarket parts. “Not every contractor or situation requires a genuine OEM part,” Reeves said. “These value lines will offer the same fit and function as the original part and will typically be backed by a limited warranty.”
The advantage of parts offerings, since they are endorsed by the manufacturer, is that they are built to the same tolerances and work as part of adjoining system components. However, they may not offer as much durability or as long of a service life as the genuine OEM part does.
“These value lines are designed to be conveniently accessed, offer manufacturer-grade reliability and be purchased at a lower price than OEM parts,” said Reeves.
Rebuild/Remanufacture
Contractors keeping up with preventative maintenance schedules tend to get the most life out of the components of the machine. When planned indicators like inspections, service history and oil sampling show that components are toward the end of their first life, contractors should address the rebuild prior to seeing an indicator.
“Often, that first rebuild will be a rebearing/reseal, replacing Level 1 wear components and offering the lowest cost option for the rebuild,” said Scott.
The longer a contractor holds onto a piece of equipment and the service meter units add up, Level 2 components will begin to show signs of wear and will require either component rebuilding or remanufacturing. “The rebuild and remanufacturing processes are similar in the fact that the component is completely disassembled, cleaned and inspected,” said Matranga. It’s what happens after this stage that differentiates the two strategies.
These processes are intended to bring the machine’s component back to its original expected life. The rebuilt component, typically handled by a certified equipment dealer, includes the original parts paired with new to replace the ones that are too worn. “Basically, the component keeps its identity, and the machine keeps its core,” said Totten.
With the remanufacturing process, all the cleaned and reusable parts of the component go back to the manufacturer’s assembly line to be rebuilt. “The component loses its identity and the machine its core,” said Totten.
Despite this, contractors should expect to get another life from the component out of both rebuilding and remanufacturing. Additionally, the component also comes with the same warranty as if buying a new component. The contractor keeping up with equipment maintenance and repairing problems before failure will experience one final benefit at the time of unit disposal, regardless of whether the machine is on its first or third life.
“A full history of performed maintenance and rebuilds will accompany the machine, and those units that were properly maintained will bring a higher resale value,” said Matranga.