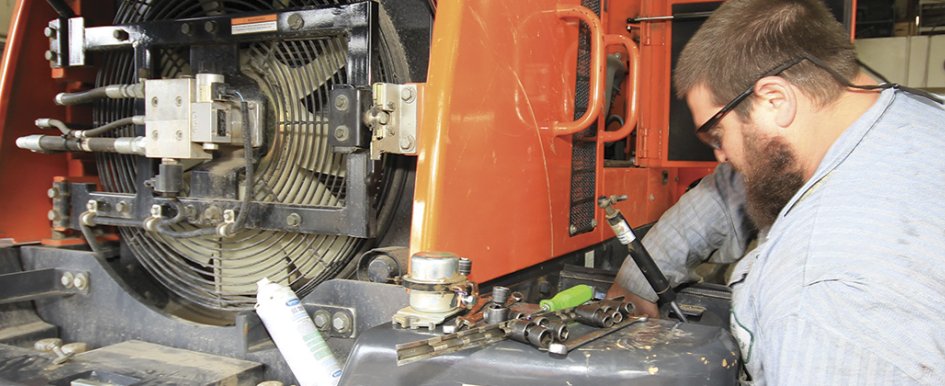
Critical machine components can be expensive to replace, so it is important that service technicians do everything they can to protect equipment investments and create the cleanest environment possible. You must adopt a clean-shop mindset to ensure the most productive environment possible. Cleaning wash bay floors, maintaining proper lighting, adhering to proper storage procedures, promoting technician hygiene, using high-pressure washers and handling fuel filters properly are a few recommendations helpful for minimizing contaminants.
1. Clean wash bay floors
Shop cleanliness starts with a clean, well-maintained floor. Designated wash bay locations should be free of dirt, oil, hydraulic fluid and other materials. If oil, grease and contaminants are not cleared from the floors, one can assume nothing else will meet the necessary level of shop hygiene.
Typically, wash bays are set up with drainage areas that allow sediment to fall and oils to collect. In some locations, the water can be discharged into the sewer, but in other areas, it must be held and removed from the site for further processing.
2. Maintain proper lighting
Equip your service areas with proper lighting, such as energy-efficient LED lightbulbs, so technicians can easily view all machine components and parts. Most older buildings were not built with natural light like many newer buildings. As a building ages, so does lighting, making it harder to see dirt. Every 5 years, you should conduct a thorough cleaning. You may be surprised at what was missed in the daylight.
3. Follow proper fluid storage procedures
Improper handling or storage of machine fluids can compromise fluid cleanliness, which may damage parts and critical system components, resulting in increased downtime and shortened component life. Set up a dedicated work environment and follow proper fluid storage procedures to reduce the threat of contaminants.
Some companies have a dedicated fluid containment area for engine oil and hydraulic oil. The oils are housed in bulk storage containers that are fully equipped with a filtration system to help reduce contaminants. Any fuel entering a storage tank should pass through a filter to help increase the effectiveness of the machine's fuel filter and prevent contaminants from entering the engine. Fuel tank filters should be capped and the tank vent must be filtered. Typically, tank filters have a 10-micron water separating fuel filter to help remove moisture as fuel is dispensed through the vent.
Moisture and other contaminants in fluids can cause damage to system components. Technicians should inspect supply tanks and remove any water present before transferring it to the machine tank. In addition, fluid-sampling services can be used to determine whether fluid has been compromised due to improper storage practices.
4. Promote technician hygiene
Maintaining proper hygiene is especially important. If a technician's hands are dirty when handling a new fuel filter, the dirt can be transferred onto the fuel filter and potentially impact your machine. Although some fuel filters can trap down to 2-micron contaminants, no filter will remove all particles. In addition to shop hygiene, using gloves can promote long-term personal health by reducing the amount of oils and fluids that are absorbed into a technician's skin.
5. Use high-pressure washers
Instead of washing dirt, dust and other debris from your machine and its components by hand, technicians today use high-pressure washers. High-pressure washers clean parts quickly and thoroughly, helping reduce costly downtime. Clean wash stalls and power wash a machine before a technician works on it. Technicians need to spend time cleaning the machine, especially when completing major maintenance.
6. Proper fuel filter Use
Before installing a new fuel filter, technicians should pressure-wash the fittings and lines to remove dirt and other debris. Any open component invites dirt, so if technicians complete even the simplest of repairs, they should clean around each item. Technicians should always install the filter immediately after removing it from the plastic bag. If the filter cannot be installed right away, it should be placed in a sealable plastic bag and labeled with the part number.
With these six tips, your service department can offer a clean, dirt-free environment and reduce contaminants that might otherwise harm machine components.