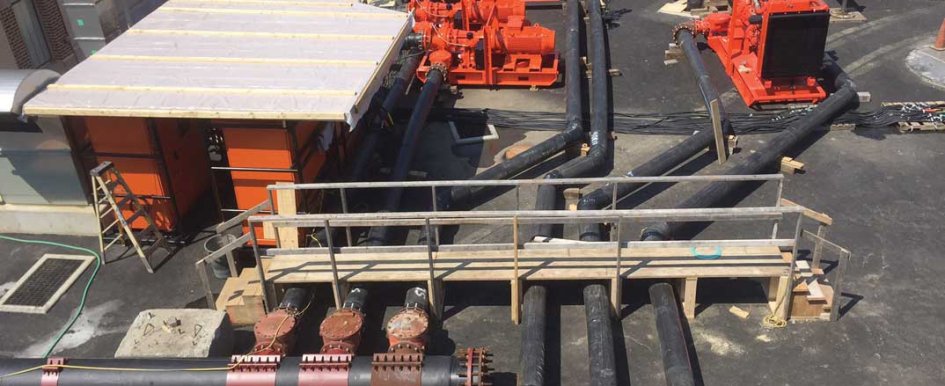
The city of Lancaster, Pennsylvania, like hundreds of other cities across the United States, is saddled with an aging infrastructure originally designed and built in the mid-1800s. Basement sump pumps, roadside storm water drains, sewage lines and industrial wastewater all drain together, and the system is easily overwhelmed by storm events and annual snow melt. One solution, to build miles of separate lines for storm water and sewage under city streets, was financially and physically prohibitive. So, the city is tackling the challenges as efficiently as possible without causing undo financial burden to the city or its residents. Upgrading the city’s four pumping stations along the Conestoga River to reroute more storm water to the city’s Advanced Wastewater Treatment Plant (AWWTP), instead of draining into the river, has been part of the upgrade plan for the past few years.
The Lancaster North Sewage Pumping Station expansion was one of the many projects that the city had undertaken. To spearhead the effort, city officials hired CDM Smith as consulting engineers to design the pump station project. Wickersham Construction & Engineering, a local firm with over 100 years of experience in commercial and industrial construction, won the bid for the construction work. Given the many projects in the environmental and wastewater space over the years, and the fact that the company’s headquarters was located in Lancaster, the company was the perfect fit for the job. Wickersham brought in Xylem, a water technology provider, to design and handle the temporary bypass required to circumvent the station while it was being upgraded.
“This wasn’t a straightforward construction job, with the bypass and the multiple components. It was pretty complex, so it was important to have a good team in place,” said Jeff Laney, project manager for Wickersham Construction. “Our previous experience with both CDM Smith and with the Xylem team gave us the comfort level we needed.”
The North Sewage Pumping Station is designed to receive influent from three different lines: a 120-inch, combined sewer and storm water line from the city; and two sewer lines—one 30-inch line and another 24-inch line—each coming from different area municipalities. The average flow into the pumping station is roughly 9 to 12 million gallons per day (MGD), with the capacity for twice that in case of a storm event. As a result, the team designed a bypass that could handle upwards of 24 MGD, a precautionary measure to ensure that increased flow could be handled, even in the unlikelihood of a 100-year storm event.
Temporary Bypass with Permanent Capabilities
The team needed to be sure that every detail was addressed with the bypass. They couldn’t risk a sanitary sewer overflow (SSO) caused by a failed pump or a power failure. As a result, there were multiple backup precautions taken to ensure 100-percent uptime and optimum efficiency. “We needed a temporary solution that would be in place 3 to 6 months, but it needed to have permanent substance,” said Laney. “The concern is that a temporary solution might have less staying power, and falter along the way. But the bypass design was very strong, and we had every confidence it could do the job for us, as long as it took.”
To move that much wastewater, Xylem recommended that Wickersham rent six Godwin HL250 pump sets with 12-inch discharge flanges. Four of the six units were electric pumps, and they were established as the primary pumps for the project, running from a temporary power line. Each pump was installed with a variable frequency drive (VFD) unit, in order to control pump speed and enhance power usage.
For additional energy savings and to optimize efficiency, the bypass design called for the pumps to be installed and to be started sequentially, only kicking on as needed. Each pump was set up with a level transducer, which was preset to turn the pumps on and off, depending on the fluid level in the wet well. The pumps were only activated if increased system flows called for additional pump activity. During typical daily flows, one, or possibly two, pumps would be running. As many as three or four pumps would run during higher, peak-flow activity. To ensure the electric pumps would work in case of a power outage, a backup generator was installed to kick on should the temporary power line be disrupted. The other two pumps that were implemented into the design were diesel-driven, and were put in place as redundant backup pumps to kick on automatically, should any of the four primary pumps fail. The bypass around the pumping station turned out to be approximately 400 feet long, and comprised of twin discharge lines of 24-inch, HDPE pipe. Each discharge line was fed by two pumps, and the lines tapped into the 36-inch, force main 400 feet downstream, on the way to the Lancaster AWWTP. The team installed flow meters in each of the twin lines.
The data from the flow meters fed into a PLC controller and the plant supervisory control and data acquisition (SCADA)system, alerting plant operators to the amount of flow that was coming their way from the bypass. This would allow the facility to adjust their influent flow rate, should there be spikes or drops that needed to be handled one way or the other. To ensure that flow rates were monitored and that the bypass pumping operation was handling the flow, the team installed high-level floats with auto-dialers to alert Wickersham personnel and the project foreman when the backup pumps kicked on again.
Why Rental Is Key for a Temporary Solution
After years of working with the city of Lancaster and careful planning, designing and implementing the expansion of the Lancaster North Sewage Pumping Station, the team was able to activate the bypass pumps on June 22, 2016. The actual construction component of the upgrade and expansion of the station could actually begin in earnest, and it was expected to take 3 to 6 months.
For the duration of the project, Wickersham rented the pumping equipment, piping and accessories. This allowed Wickersham to minimize costs, paying only for the equipment and services they needed. They also didn’t have to worry about the maintenance and upkeep of the equipment long term, unlike had they purchased it outright. They could also focus on their core business and their primary part of the project—the pump station upgrade and expansion.