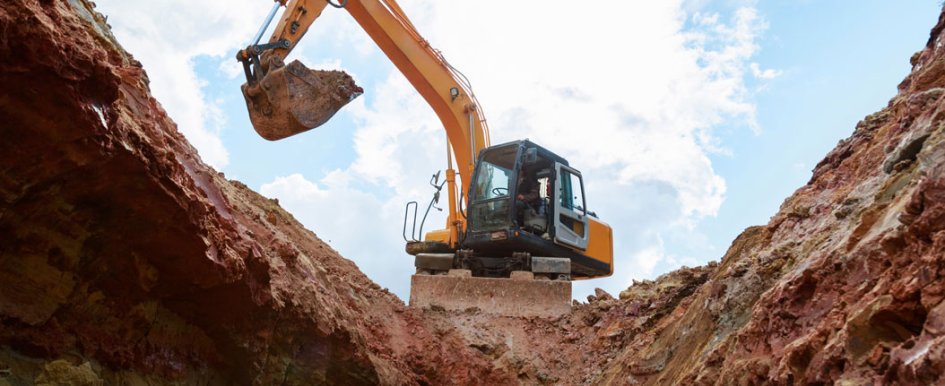
How a contractor chooses to excavate on a jobsite can make all the difference in the project outcome. When one considers that 30 to 40% of all excavations lack the appropriate protective solutions, it should come as no surprise that projects are often over budget and overdue. When the very real risk of injury or death is factored in, a lack of proper protection makes no sense at all.
Appropriate trench protection solutions and safety training are the difference between a safe, productive jobsite and putting your project at risk. The time spent in choosing the right protective system and ensuring that the team is up to date on training is an investment in project success.
The Occupational Safety and Health Administration (OSHA) mandates that a protective system be used any time an excavation is at a depth of five feet or more.
With four types of workable, OSHA-approved protective solutions available—sloping, benching, shoring and shielding—contractors will be safest and most productive if they learn how to select the most effective system for a given jobsite.
A protective system has multiple components, all of which factor into the selection and installation processes. It starts with aligning the system to the soil and jobsite conditions. This is followed by thorough inspections throughout the project and mandated safety training. In addition, there is a balance between keeping the project moving and knowing when to call on the expertise of a professional engineer.
Key Trench Protection Considerations
As a company assesses a project, here are four considerations to help align the right protection system with the job.
- Start with soils—Soils are probably one of the most important factors to consider. Properly identifying the soil type will help the competent person select the appropriate protective system. Sloping and benching angles vary for different types of soil and the depth ratings of shields and shoring change from one soil type to the next.
- Dimensions/working area required—Consider the necessary dimensions of the excavation, depth, length and width. For example, a large installation, such as an electrical vault, needs a different protection system than an installation of a long, linear gas pipe or water main. Then, think about the working area available for the employees. Is there enough room for them to safely complete the task? Lightweight aluminum boxes and vertical hydraulic shores are both commonly used options, but the working area available within those protective systems is physically very different.
- Conditions in the surrounding area—Another important consideration is the conditions in the working area. Factors such as existing utilities, adjacent structures, surface encumbrances, overhead obstructions and groundwater issues must all be considered when selecting the best protective system for the job. For instance, the use of a sloping or benching system often requires a mass excavation of dirt, which means an area large enough to house the pile is needed. This can pose a unique challenge in urban environments, where workspace is limited. Crews working in these environments may need to come up with a creative alternative.
- Machinery available—The machinery that is available on a jobsite greatly changes the options of protective systems which can be used. For example, the dimensions of an excavation and the soil conditions may warrant a steel trench shield. However, if the only machine on the job is a backhoe (which can’t handle that kind of weight), an alternative method would need to be considered, such as aluminum boxes or hydraulic manhole braces and sheeting.
When to Involve a Professional Engineer
Excavations near adjacent structures, underground utilities and roadways may come with unique and complex challenges that often require professional input. Although contractors can usually utilize manufactured systems with tabulated data, there are times where additional guidance and stamped drawings from a professional engineer (PE) are necessary.
Any excavation over 20 feet deep automatically requires the use of a PE. A PE is also necessary when there are heavy surcharges, such as heavy equipment, stockpiled equipment, roads, bridges and buildings, close to the excavation. PEs look at all the conditions for the site and develop a shoring or sloping design that will work for that specific location. Working with an experienced engineering team can speed up the process considerably.
Contractors may be reluctant to turn to a PE because they fear the PE will develop a shoring design that requires more expensive, non-standard equipment. But many site-specific designed shoring systems use off-the-shelf equipment.
Role of the Competent Person
Once a trench protection system has been selected and installed, contractors naturally want to feel confident that the shoring and shielding equipment they’ve installed to protect their workers is doing its job. This is where inspections come in.
OSHA requires every jobsite to have a competent person who has been trained to inspect trenches and identify existing and predictable hazards or dangerous working conditions in the surrounding area. The competent person is responsible for overseeing all aspects of the excavation, including the inspection of the shoring and shielding equipment.
This requires a daily check at a minimum. It is also necessary to do an inspection every time there is a change in conditions. For example, this could be a rainstorm that can directly affect the stability of the soil. It is critical for the competent person to continually monitor jobsite conditions and reclassify the soil if necessary.
Safety Training Is Imperative
Maintaining up-to-date training on safety regulations and equipment solutions is essential to keeping construction workers safe. Too often, workers doing this type of underground work think an accident won’t happen to them. And in some cases, workers may not even realize they are facing a hazard due to lack of training.
Unfortunately, accidents happen all too often. When a worker suffers a life-changing injury or fatality, the cost goes beyond citations, fines and court settlements. In the end, families are left with the burden of moving forward and coping with their loss.
When to Tap Third-Party Experts
The challenges of jobsite safety and productivity are factors contractors face every day. It can be a good strategy to tap into third-party experts which offer quality safety training, as well as other types of support outside the classroom.
As an organization looks to deploy the right trench protection system for each jobsite, consider the advantages of using third-party resources to tackle areas that are outside a company’s usual range of performance or experience. These experts can solve gaps in a variety of skills, such as providing specialty equipment, training, pre-bid analysis on protective systems, on-site consultation and engineering designs.
The fundamental objectives of trench protection systems are to advance worker safety and jobsite productivity. A well-made, OSHA-compliant and all-inclusive trench protection system tackles both objectives on two levels: equipment and personnel. With these needs addressed, contractors can not only maintain safety on the jobsite, but also produce quality work without risk to budgets or deadlines.
This article discusses common industry processes and is not intended to be a substitute for site-specific professional/expert advice, instruction and supervision. United Rentals recommends consulting with Shoring and Excavation Experts to ensure full compliance of Federal OSHA 29 CFR, Part 1926, Subpart P-Excavations and Trenches.