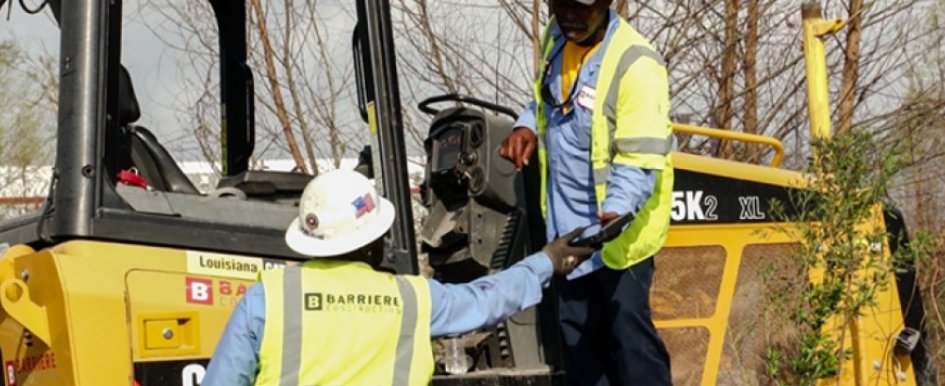
An effective equipment inspection process is vital in heavy construction, but when paper forms drive that workflow, contractors are at a disadvantage when it comes to improving uptime, safety and maintenance costs.
Trading clipboards for tablets and electronic forms creates a real-time connection between the maintenance team and the jobsites. Electronic forms make it easier to collect more and better data about equipment. Immediate, online submission allows the maintenance team to take action sooner and work more efficiently.
“The biggest factor, when we relied on paper, was getting the information back from the field in a timely manner,” said Heath Wahden, chief financial officer at Barriere Construction. The Louisiana-based company relies on more than 200 on- and off-road assets for heavy construction and paving. Barriere Construction now uses B2W Inform for electronic data capture and analysis in combination with the B2W Maintain maintenance management solution.
“There was a gap of sometimes a week or even 2 weeks in getting information to our equipment coordinator, so he could see what was going on in the field and schedule the work before it became a critical failure, and the equipment stopped working,” Wahden said.
The average time to complete for identified repair work is a key performance indicator tracked by Barriere Construction. Wahden said the electronic inspection process has helped the company drive this number to below one a week.
The Right Forms Deliver the Right Data
At Barriere Construction, as is the case at many construction companies, foremen used to maintain a large library of paper inspection forms. Still, they struggled to keep up with updates and have the correct form on hand for each specific piece of equipment. That scenario leaves contractors with two bad options. They can use a generic form or the one closest to the one they really need. Neither choice will deliver accurate, thorough information.
With an electronic solution, the library of forms is online and available from mobile devices. Forms can be customized to capture the necessary information about each asset. Editing is easy, and publishing is instantaneous, so foreman and operators in the field can always access the right form.
“With paper, the operator had a form that was generic across all machines,” said Ben Tucker, director of equipment and facilities at Barriere Construction. “Now, they have a specific inspection form for each type of equipment. From an equipment manager’s standpoint, you’re getting to the details of your piece of equipment, whereas with a generic form, you can’t get to the specifics.”
Faster & Easier in the Field
Ask employees on any construction site what they like least about their jobs, and there is a good chance paperwork will be at the top of the list. Filling out forms, including inspection forms, can be seen as a time consuming distraction from “real work.”
Electronic forms do not eliminate the disdain for paper work, but they minimize it. The forms are easier and faster to fill out and submit on a mobile device. They don’t get lost or damaged. The follow-up conversations to decipher handwriting or clarify information disappear. A built-in audit trail can even eliminate doubt about where a form is in the process, who submitted or approved it, and when.
Tucker reports that operators and foremen at Barriere adapted quickly to iPads and appreciate the added benefits to them.
“They see that the information they are filling out is needed and has value and that someone is going to respond,” he said. “They know it’s getting turned in and it’s not in someone else’s hands for a week or two. You can get it fixed within a week’s time now.”
More & Better Data
With paper forms, the quality of the data invariably depends on the effort and interpretation of the individual filling it out. Operators and supervisors are free to leave out information or an entire field by accident, or if they feel it is in their interest to omit information. One might fill in the job, equipment and date fields as “Main St. Extension,” “Volvo Exc,” and “Oct. 5,” while another fills in the same fields as “Job 8563-12,” “V-473” and “10/5/19.”
The result is inconsistent or “unstructured” data that leads to errors and makes creating reports a difficult, manual process.
That doesn’t happen with electronic forms. Fields can be made mandatory, preventing the form from being submitted until they are filled in. Drop-down menus, check boxes, radio buttons and other features ensure accuracy and consistency.
Forms fields can also be linked or “data bound” to a central database. For example, on an inspection form, drop-down menus for the name of the asset, the jobsite and the operator filling out the form can be linked to a centralized list of equipment, jobs and employees. Operator “John Smith, Jr.” is identified correctly every time and not listed as “Johnny,” “J. Smith,” “Smitty,” or any other variation on various forms.
Electronic signatures, time stamps and GPS tracking help to validate when and where electronic inspection forms were completed, and the ability to add photos or video clips is a major benefit.
At Barriere Construction, equipment operators frequently take a photo of a defect or part that needs attention when they fill out an electronic inspection from using B2W Inform. That can be faster and much more informative than trying to compose a long written description. Maintenance managers can then upload the image into the electronic work order created with B2W Maintain, so mechanics actually see what they are up against before they arrive.
Data Drives Uptime
Equipment inspections are ultimately intended to improve uptime, safety and maintenance costs. Electronic forms support those goals by minimizing the critical interval between when a maintenance issue is detected and when it can be corrected. The typical one- or 2-week journey from the field to the shop for a paper form gives way to instant submission.
“We were finding that a lot of this information was getting lost in the trucks of our foremen and supervisors and really slowing down our ability to effectively schedule and repair our equipment,” said Wahden.
“You would give operators a piece of paper and then you would have to wait 2 or 3 weeks to get it back,” said Tucker. “Now you can get everything in real time. You’re cutting out time lapse, which keeps the operations team in the field happy.”
Small problems get corrected before they become big ones. Maintenance teams armed with that real-time information can plan and prioritize their work more efficiently.
Identifying trends and completing repair work more efficiently can also cut downtime and maintenance costs. Timely inspection reports delivered in a structured, electronic format makes it easy for contractors like Barriere Construction to aggregate and analyze the information, identify trends and take corrective action that is driven by data.
Analysis of repairs over several months, for example, could identify operators who may need more training to operate the equipment properly. A record of similar failures on a specific part or subsystem might indicate that routine maintenance is not being performed correctly. Those kinds of trends might never be recognized if the information was trapped on paper forms and filed in a drawer.
“We’re not only getting information faster and completing repairs faster,” Wahden said. “We can also track and trend the different elements that are collected on the forms and provide meaningful trend analysis to predict issues with pieces of equipment.”