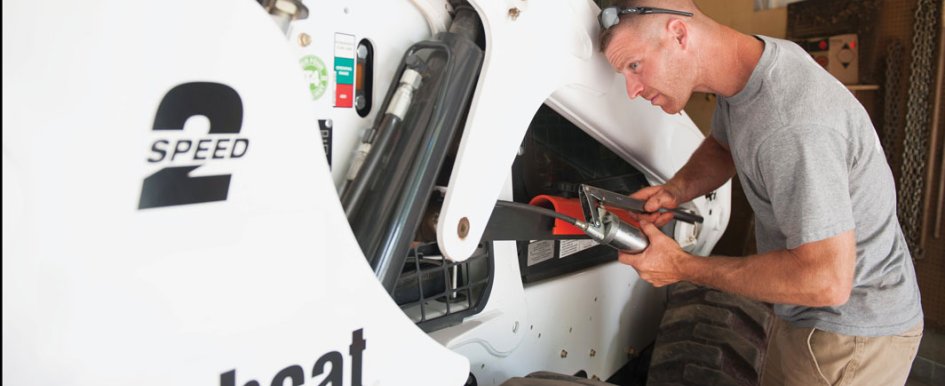
Cutting corners when it comes to engine oil, hydraulic fluid or grease might save a few bucks on the front end, but it can have a detrimental effect on equipment long term. Tier 4 emissions requirements drive much of modern diesel engine oil requirements. Low-sulfur diesel fuel and aftertreatment systems call for engine oils compatible with these elements, and manufacturers develop their engines to work with an oil tailored to their machines’ needs.
Additionally, equipment relies on hydraulic fluids for motion, and, like engine oils, manufacturers develop fluids that optimize hydraulic system and hydrostatic drive performance.
Finally, grease is tailored to the machine’s application based on aspects, such as shock loading, temperature, moisture and component serviceability. Selecting the right engine oil, hydraulic fluid and grease for a machine optimizes its operation and will allow it to achieve maximum service interval and overall service life.
Oil Classifications
The American Petroleum Institute (API) has developed a classification system that sets minimum specification requirements for engine oil. Oil categories for use in diesel engines begin with “C.” CK-4 oils, which the API introduced in 2016, are formulated for high-speed diesel engines and are designed to meet 2017 and newer on-road and Tier 4 nonroad emissions requirements.
CK-4 oil formulations work with modern low-sulfur diesel fuels up to 500 parts per million (ppm) and help protect against oil oxidation, oil aeration and viscosity loss due to shear. CK-4 oils also surpass the performance requirements of CJ-4, CI-4 and CH-4 oil classifications and can be safely used in engines calling for those oils. It is important to always use a high-grade oil that meets or exceeds the API classification of your engine.
Viscosity Matching
When selecting an engine oil, ensure the viscosity rating, set by SAE International (initially established as the Society of Automotive Engineers) is suitable for the outside temperature of your jobsite. Your equipment’s operation and maintenance manual should outline the recommended oil weights in various weather conditions. If you have misplaced your operation and maintenance (O&M) manual, contact your dealer for another copy to reference in these and other maintenance situations.
Many machines roll off the production line with a 10W-30-weight oil, which offers the best performance in temperatures ranging from minus 20 degrees Fahrenheit to 90 degrees Fahrenheit. A 15W-40-weight oil performs well from minus 5 degrees Fahrenheit to 110 degrees Fahrenheit.
Synthetic or synthetic-blend oils contain additives that can lengthen the time between oil changes while also extending engine life. They also provide better cold weather starting and lubricating performance, as well as additional protection against wear when jobs demand operation at high speeds in high temperatures. For example, a 5W-40-weight synthetic oil can usually offer protection in extreme conditions as cold as minus 40 degrees Fahrenheit and as hot as 120 degrees Fahrenheit.
Hydraulic & Hydrostatic Oils
The formulations of hydraulic and hydrostatic oils have been updated to meet the increased demand placed on hydraulic components. There are several types of these fluids on the market, each designed for a particular application:
- High performance—A custom blend of high-quality lubricants developed to provide peak flow at subzero temperatures while maintaining stability during periods of high temperatures
- Synthetic—Liquid technology designed to optimize cycle times and productivity, and provide good cold weather fluidity for seasonal changes
- Biodegradable—Liquid design that meets customer demand as federal, state and local governments set environmental-related project restrictions. It’s biodegradable, nontoxic and formulated to reduce the potential for environmental damage.
Grease
Most compact equipment requires operators to grease and lubricate the pivot points where pins and bushings are located. Your machine’s manufacturer should specify greasing intervals in the O&M manual, which may be online for quick reference. If applied correctly, grease can help extend the life of components and improve the efficiency of the machine. The National Lubricating Grease Institute classifies various types of grease, which should be matched to the machine’s working conditions.
- Multipurpose #2—Developed for normal applications; provides lubrication to prevent rust and corrosion, and protection under heavy and shock loads
- Heavy duty—Contains molybdenum disulfide lubricant for better adherence to all surfaces; offers water resistance, extreme pressure capabilities, pumpability in cold temperatures and good seal compatibility
- High performance/synthetic—Formulated to provide high- and low-temperature performance in severe operating conditions; intended for lube points that slide and pivot
- Chisel extreme pressure—Formulated for use in extreme pressure applications where moisture and corrosion control are critical; is extra heavy duty; remains stable in water; and offers a balance between wear protection and corrosion resistance
Oil Analysis
With the increased demands on Tier 4 diesel engines, hydraulic and hydrostatic oil, compact equipment owners may want to consider additional preventive maintenance measures, including an oil-analysis program. This program includes a comprehensive evaluation of your machine’s oils by an accredited laboratory, helping you more effectively monitor internal operating conditions.
Regularly sampling and monitoring test data can highlight trends over time, helping you detect ferrous particles, wear, contaminants and fluid cleanliness. Always consult your O&M manual for guidelines on preventive practices and remember that sampling oils can easily vary service schedules.
Factors that can impact maintenance frequency requirements include how important a machine is to your operation, as well as environmental conditions, such as hot, dirty jobsites; brief trips with heavy loads; and excessive idle times. To get the most benefit from an oil analysis program, ensure samples are taken regularly.
Top 5 Oil Analysis Benefits
1. Identify contaminants—Keep a close eye on oil conditions to identify wear-causing contamination that could negatively impact a machine’s internal operating system.
2. Ensure lubricant integrity—Inspect lubricant properties to help determine if oils are performing properly.
3. Identify minor problems before major failures—Spot oil contaminants like dirt, wear particles, fuel dilution and coolants early to help prevent poor performance and catastrophic failure, as well as protect the life of your equipment.
4. Maximize asset reliability—Putting testing and analysis data to use can increase equipment uptime.
5. Increase resale value—Validate maintenance history documentation with analysis results, which may justify higher equipment resale values.