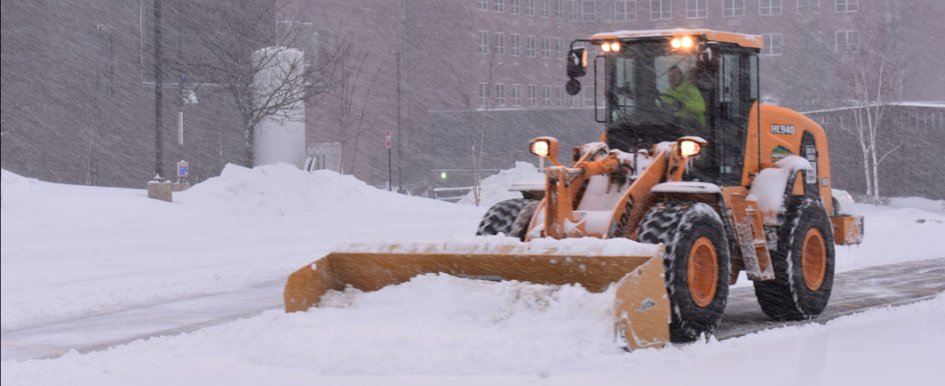
Whether or not you continue operating through the winter months, winterizing your construction equipment is crucial for protecting your investment in those machines and the future business they represent. Use the following as a checklist for your equipment walk-arounds this winter.
1. Batteries
If your construction equipment goes unused for a long period of time, you will need to properly store the battery away from frigid temperatures. Batteries can lose up to 35% of their power at 32 degrees Fahrenheit and as much as 60% at 0 degrees Fahrenheit. To prevent the battery from draining in the cold temperatures, you should test its voltage before storing it inside.
When the equipment is to be stored for long periods of time, it’s a good practice to remove the batteries and store them in a protected building out of the weather. If they are serviceable batteries, test them to be sure that they are still serviceable, and, if so, add distilled water and place them on a trickle charger.
2. Tires
Daily preventive maintenance for tires is a year-round job, which becomes even more important as temperatures begin to drop. During the winter months, check the air pressure of your tires and look for signs of wear and tear frequently.
Tires tend to deflate quickly in colder temperatures—giving track-mounted equipment a winter advantage over tire-mounted equipment.
3. Grease Points
Grease is the lifeblood of all pins and bushings. Grease all grease points thoroughly, making sure to have good coverage for winter. Don’t forget to grease the axle hubs, too.
The operator’s manual will identify each grease point and provide recommendations for quantity and grade of grease. If multiple operators are using a single machine, you can flag less obvious grease points with orange paint to remind all users to perform this task.
As with undergreasing, overgreasing can also be problematic. One to three shots of grease is typically plenty to do the job. Using more wastes money, presents a potential environmental hazard and can cause a considerable mess.
Once the unit is removed from storage, grease again. Grease can become hard and laden with moisture, so pushing the old out and purging with new will be sure to protect the machine.
4. Fuel & Additives
Using an anti-gelling additive in diesel fuel can improve your engine start-up in cold weather. This can also improve cold flow by preventing gelling and will even clean deposits from fuel injectors, combustion chambers and intake-valve deposits. These additives are readily available at any local dealership or service shop.
Change the fuel filters and fuel separator filters to be sure no moisture has been retained that might cause problems later on. Moisture in the engine can occur when the engine is hot and the outside temperatures are very cold.
Moisture may especially form in the fuel when the equipment has been sitting and can occur as quickly as one weekend’s time. If the fuel does begin to gel, it’s quite possible that the gelled fuel will clog the fuel separator.
Construction equipment fuel tanks typically have a drain plug in the bottom. When the unit sits for any period of time, the water settles to the bottom of the tank, as it is heavier than fuel. So, remove the drain plug and drain the tank until water no longer comes out.
5. Engine Oil, Coolant & Hydraulic Oils
Change the oils in your construction equipment before and after the winter months. During the winter, use low-viscosity oils that will flow with less resistance. This includes oils for the engine, transmission, differentials and hydraulic system.
Drain intervals are not dictated by hours but have a maximum time that the oil should sit. You should refer to your operator’s manual, but a good rule of thumb is to drain oil after 12 months of accumulated time, even if the unit has been running.
Most diesel engines today come with glow plugs or heating grids, which are nothing more than an element similar to the type you see in electric heaters, but a bit heavier duty. A heating grid preheats air going into the internal combustion chamber, which heats up the engine to a suitable temperature for combustion.
Otherwise, when cold fuel is sprayed into the chamber, it can gel and adhere to these parts. Hard starting and inefficient combustion occur with potential for damage to plugs and cylinder heads.
Many diesel engines come equipped with built-in, electric-powered block heaters to keep the engine block warm overnight. A diesel engine needs heat to ignite the fuel since there are no spark plugs, and this heat comes from the compression of air in the cylinders. When starting up in cooler temperatures, the heat from compression needs a little help—the grids provide this by heating the intake air.
Once the engine has been running a while, the heat from combustion warms the cylinders, and no additional heating is needed. However, those who live in colder climates will also need to install oil pan heaters. An oil pan heater makes it easier to start the engine and preheats the engine oil. When cold, oil becomes very thick and difficult to pump.
Upon start-up while using an oil pan heater, warm oil is instantly pumped to the critical wear points in the engine. This protects engine components, extends battery life and reduces emissions, while contributing to operator comfort inside the cab by allowing the engine to get hot sooner.
The ideal coolant ratio is 50-50 coolant to water, but in cooler weather, it is suggested that you try using a 70-30 ratio instead. This will prevent the water from freezing.