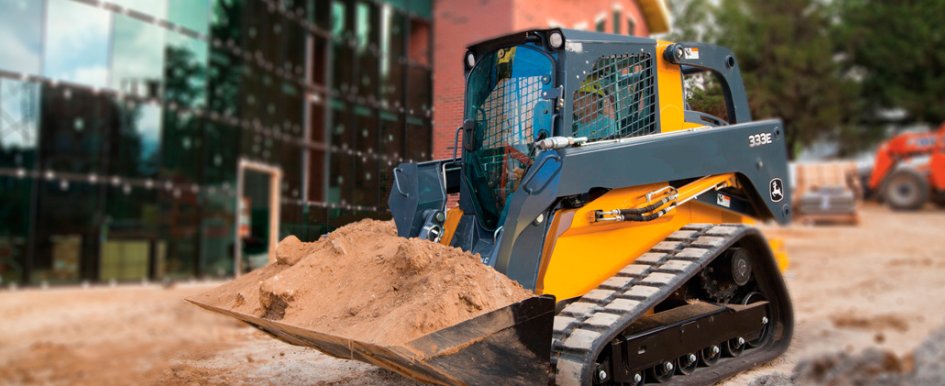
For owners and operators, machine maintenance is a necessary evil. While daily inspections may take time out of each day, it is better to find issues early than let them grow into bigger problems down the road. However, there are several simple tips that can be used to shorten the time and effort spent maintaining your machine.
1. Gain Easy Access
Prior to starting the day, the first step that every operator should take is a walk around the machine, checking the machine for debris, loose connections and fluid levels. This process can be simplified by choosing a machine that has easy access to major maintenance points, such as oil, fuel and filters. Also, take time to clean coolers and debris from the machine. Optimal cooling improves productivity and avoids unscheduled downtime. Some machines feature panels that can be quickly removed without tools, which simplifies scheduled maintenance and repairs.
2. Approach from the Bottom Up
Whether you are operating a compact track loader or wheeled skid steer loader, it is important to maintain the wheels or track in order to extend the life of the wearable. When purchasing a machine, pay attention to the undercarriage. The design of the undercarriage can reduce the load on the rubber track. Look for an open design that sheds materials and allows for easy access when digging out the tracks.
Prior to beginning work for the day, inspect the track or wheels for damage. With tracked equipment, it is critical to check track tension weekly, as improper track tension will shorten track life. If you are using a wheeled machine, make sure that the tires are properly inflated. A deflated tire can affect the performance of the machine, and a flat tire in the middle of a workday can cause unnecessary delays. During usage, make sure the path is clear and be careful about what surfaces you drive on, avoiding anything that may damage the track or tires. Avoid excessive counter rotation, as it will accelerate tire and track wear.
3. Balance Fluids and Maintenance
Fluids are the lifeblood of the machine, so operators should always be aware of what they are putting in their machines and how much of it is going in the equipment. Make sure you are putting the recommended amount of fluid in to the machine—too little or too much fluid can affect the machine's performance. When it comes to fluids, operators should avoid cutting corners to save a few bucks in the long run. Follow the manufacturer's recommendations for fluid selection. Follow the manufacturer's recommendations concerning air filters, too. While it may be tempting to regularly check on the air filter to ensure performance, avoid self-maintenance unless the machine prompts you with the air-restriction indicator. Even though it seems like a simple task, you may damage the air filter and fail to install it properly, leading to bigger costs due to engine malfunction. Always follow your manufacturers' service intervals carefully to limit potential damage to the machine.
4. Ensure Clean Input
Clean fuel is a must in order to ensure proper operation and to extend the life of the fuel system. It is important to be aware of what you are putting into the system in order to decrease the infiltration of dirt. Only refill machines from a clean source. While it is impossible to completely eliminate dirt, most manufacturers design the fuel tank to capture dirt at the bottom of the tank near the drain plug.
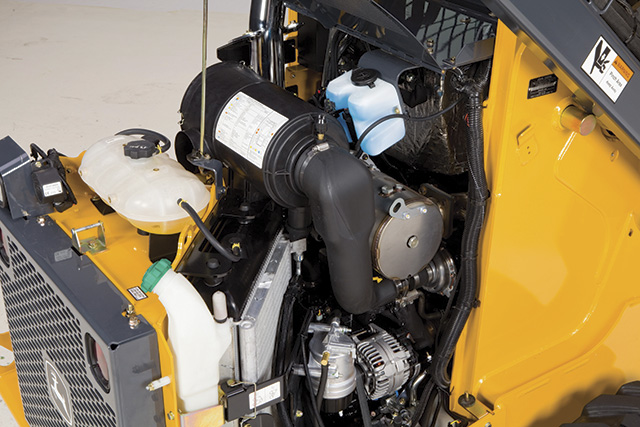
5. Improve Uptime
In addition to what you are putting into your tank, consider optional accessories that not only extend the life of your machine, but also make maintenance easier to complete. An auto-tension serpentine is maintenance free and never needs adjusting. Because the tension is always correct, it has a longer life span, which allows for longer intervals between replacements. Additionally, look for machines that do not "stack" the coolers, so that both hydraulic and engine coolant receive first-pass cool air. This feature allows for improved cooling and less buildup of material between coolers.
Another accessory that can positively impact your machine is a variable-speed cooling fan. It provides quicker fluid warm-up and uses less engine horsepower compared to an engine-driven fan, allowing more overall horsepower to be available to the rest of the machine. With less engine horsepower used to cool, operators can decrease the amount of fuel burned significantly. Also, consider a reversing fan that automatically reverses periodically to blow lose material off of the coolers.
6. Monitor regularly
Today's machines are much more sophisticated than their predecessors, allowing operators to be more aware of maintenance needs. Almost every manufacturer on the market has some type of diagnostic tool available. Take advantage of these tools to make maintenance easier. Monitors provide more information than basic gauges, making it easier to identify and resolve issues quickly. While the amount of information varies from manufacturer to manufacturer, consider diagnostics and their timesaving benefits when evaluating machines.