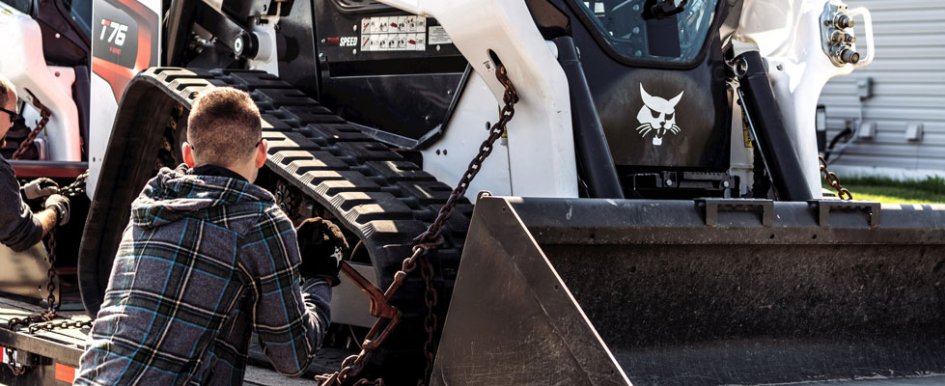
As a business owner, your plate is full — from prospecting new clients and fleet management to team member development and customer service. With your day-to-day demands, it can be difficult to find time to review or enhance your business’s safety program.
However, this is a critical component to both business operations and employee wellness. With a well-documented safety plan, you can reduce costs and the risk of injury, sickness, equipment damage and other worksite issues.
Whether you are a new business owner or a seasoned professional looking to refresh your company’s safety culture, these 10 steps, as recommended by the Occupational Safety and Health Administration (OSHA) can get you started. You don’t need to have every detail of your safety program planned out before you begin.
In fact, continually evaluating all aspects of your safety program, and adjusting as necessary will keep safety top-of-mind for you and your crew.
1. Establish safety & health as a core value
When you show your employees that working safely is not only a priority but also the default way you do business, you will see that behavior reflected in all they do. Assure your employees and crew that you’ll work with them to identify and fix any hazards that could injure them or make them sick.
In addition, learn to recognize the signs that your employees need a break or additional support — provide them with a safe environment to share concerns and ask for help.
2. Lead by example
As a leader and business owner, it’s critical to actively practice safe behaviors yourself and make safety part of your daily conversations with your employees and crew. Schedule a regular morning meeting to go over projects, equipment and any potential hazards on the jobsite.
In addition to showing your commitment to safe behaviors, take time to show your employees that you make your own safety and well-being a priority.
3. Implement an easy-to-follow reporting system
Develop and communicate a simple procedure for workers to report injuries, illnesses, incidents (including near misses/close calls), hazards or safety and health concerns without fear of retaliation. Include an option for reporting hazards or concerns anonymously.
This is a part of creating a safety-first environment where your employees feel confident that their thoughts and opinions hold weight.
4. Provide up-to-date training opportunities
Train your employees on how to identify and control hazards in the workplace. Safe equipment operation requires a qualified operator, so it’s important to train workers how to operate equipment safely and efficiently.
For equipment operators, there are a few musts no matter what the situation: understand the written instructions, rules and regulations; operate the equipment during training; and know the work conditions including materials being handled, prohibited work areas or location of underground lines.
5. Conduct inspections
Be sure to regularly inspect your workplace and active jobsites with your employees. Take turns asking them to identify any activity, piece of equipment or material that could be a cause for concern, and have them provide details. Use checklists to help identify problems and show your newer employees the right way to provide documentation on a safety hazard.
6. Collect hazard-control ideas & Improvements
A critical piece of employee engagement is active participation in your safety program. Ask your employees for ideas on improvements to the program and follow up on their suggestions. Provide them with time during work hours, if necessary, to research solutions.
Consider annual team-building activities around safety (as time allows) as a way for your employees to invest in each other, and your business, through a continually enhanced safety program. Consider how to tie your safety program to employee recognition to enhance engagement.
7. Implement hazard controls
Assign employees the task of choosing, implementing and evaluating the safety program solutions they come up with. Give them opportunities to share information about each solution and educate their coworkers — the responsibility of leading a group can provide additional leadership skills.
8. Address emergencies
Identify foreseeable emergency scenarios and develop instructions on what to do in each situation. Meet with your team to discuss these procedures and post them in a visible location in the workplace. Consider regular emergency preparedness drills to keep this information fresh.
9. Seek input on workplace changes
Consult with your employees and identify potential safety or health issues before making significant changes to the workplace, work organization, equipment or materials.
10. Make improvements to the program
Set aside a regular time to discuss safety and health issues, with the goal of identifying ways to improve the program. As mentioned above, use this opportunity as a team building exercise so your employees can actively participate in this aspect of the business.
Remember, sound and straightforward safety practices are good business. Investing in your business’s safety and the health of your employees yields a return on investment, from cost savings to positive public image. By infusing a culture and expectation of safety in your organization, these practices will become habits for you and your employees.