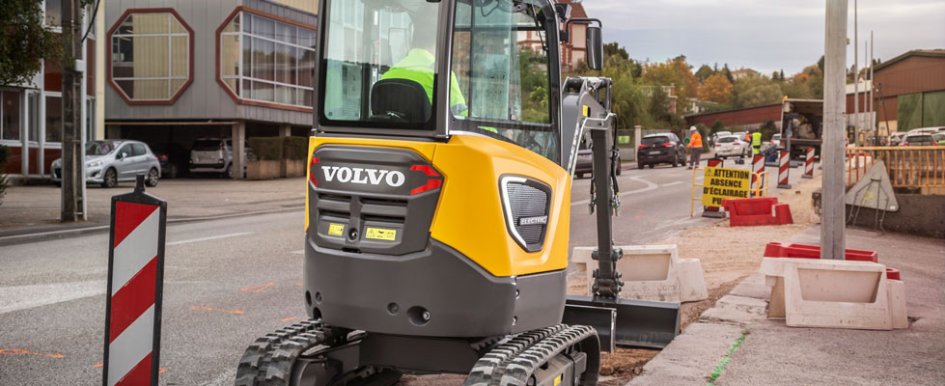
Each year, we see exciting innovations move from conception to implementation on construction jobsites and in construction businesses. As more original equipment manufacturers (OEMs) make progress toward equipment electrification, it is essential to understand the research and development that led us here and what challenges and opportunities exist moving forward.
Four major trends drive the shift toward electromobility — or electrification — as a possible alternative fuel in many industries. The one that everyone is currently talking about is the push toward sustainability. Electric vehicles significantly reduce machine emissions, which alone is a worthy enough reason to continue the work. However, it’s also important to ensure that the new sustainable paths are economically sustainable as well.
The second major driver — related to sustainability — is political change. Over the past decade, we have seen a number of government programs and incentives come out to promote sustainable changes. A recent example: 15 states and the District of Columbia have committed to being 100% emission-free by the year 2050. If we’re going to meet those targets or even come close, technology and research have to get behind the effort.
The third trend is urbanization. In 1950, the United Nations estimated that 30% of the population was urban-based and 70% was agrarian. Today, it has basically reversed. This means that the processing of raw materials at rural sites is done by 30% of the population, and those goods are shipped for consumption by the urban 70% in the cities.
That is a massive change in transportation needs, raw material processing and where we see work taking place. This trend could lead to things like remote operations, where the operator controls a machine from a simulator at an urban office many miles away. Alternatively, jobsites may evolve to fully autonomous operations, where no operators are present.
And the final trend is, of course, technology. As electrification and automation technologies develop, we are able to produce efficient, workable machines that we couldn’t have built just 10 years ago. The exciting thing is that innovation opens up new business opportunities and ways of using equipment.
Equipment customers will be the ones to discover a lot of those new applications and bring them forward. New applications for electric equipment are already prevalent because it’s silent and emission-free. So, the future is not so much how we can do today’s jobs better, but how we can do new jobs and what new technologies are going to come along and complement these starting points.
What’s Next?
Considering all of this, we must keep our research and development focused on what society needs. It is not research for research’s sake or to discover new things—it is applied research to solve real problems. There will be several different technologies and companies coming together and figuring out new and better ways to do what they do today, plus new applications at the same time. It’s an industrywide effort, and every company plays a part in that movement.
Volvo has done a lot of work on electrification over the last few years. For example, the company ran the electric site in Sweden. It took an actual working quarry and electrified all the machines on that quarry and then ran the operation the same way conventional machines would have done it to see how they compared. Volvo had automated machines, grid-connected machines, battery-powered machines and hybrid machines.
With that site, the company proved that technology has matured to the point where you can be competitive with a conventional site and take advantage of some of the efficiencies and benefits of this new technology.
The OEM is now working on commercializing other jobsites, and has opened up prebooking on the first two fully electric machines: a compact excavator and a compact wheel loader. Customers have many questions on how these machines compare to conventional diesel machines. The truth is that they have comparable power, digging capabilities for the excavator and tipping loads and dump heights for the loader.
But what gets really interesting is during conversations with customers about the unique features of an electric machine. Not only can it do everything a diesel machine does, but it can also do other jobs that a diesel can’t do, thanks to reduced noise and emissions. And when they get thinking about that, that’s where the creative ideas come out.
Some contractors question how electrification influences the machines’ maintenance and, ultimately, the total cost of ownership (TCO). When you consider that these are the first machines going out into the market, the TCO comparisons and the maintenance comparisons are actually very good. In the testing, they’re coming out superior to a lot of diesel machines because electric machines have fewer moving parts, and using connective technologies, we can monitor the function of these machines very closely to fix any issues before downtime occurs.
The more we develop these new technologies, the lower the cost of ownership will go. They are expensive machines, but the benefit is the long-term return on investment and what they can do that conventional diesel machines can’t do. We’re not, by any stretch, saying diesel machines will disappear (though we hope to see increased use of alternative fuels), but there is also a place for these new technologies to come into the construction market.
There’s Still Work to Do
There are still challenges to keep working on as electrification evolves. For example, electric components may not be from the same suppliers that OEMs use for diesel components, so entirely new supply chains and companies will be coming to the market.
Wireless service to connect all of this equipment is another huge task to organize. It’s easy to gather information, but it is a waste of time if you can’t do anything smart with it. Furthermore, the charging infrastructure will need to grow exponentially. Several cities have initiatives to develop their own charging infrastructure that we will have to make sure equipment can plug into in the near future.
Finally, we will need to educate and adapt our workforce to new jobs and a new way of working. Some people are afraid of this, but I see it as a tremendous opportunity because the jobs will be safer, more comfortable, more productive and use new technologies that the newer generations are comfortable with and enjoy.