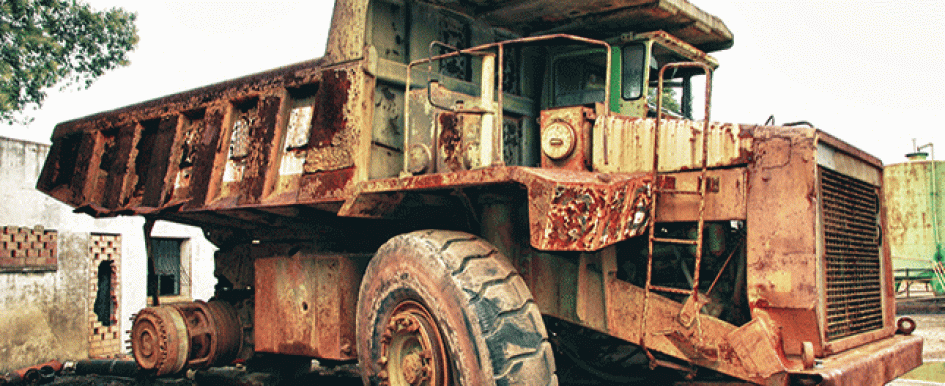
In the construction industry, physical assets are key to company operations and productivity. Employees and managers depend on equipment and tools to efficiently complete projects on schedule and on time. Many contractors, however, are killing their equipment without even realizing it. As a business owner, you may not completely be aware of the status of your equipment on jobsites. While employees may update you as best they can, information can slip easily through the cracks. Fortunately, remote monitoring can extend the life of your equipment, increase productivity and save your assets before it’s too late.
Equipment Killer 1
Performing maintenance only when major repairs are needed
If machines receive maintenance only when a major repair is required, construction business managers will likely experience more major and costly repairs compared with individuals who perform routine maintenance. For example, system contamination is the leading cause of more than 70 percent of hydraulic system and major component system failures.
However, contractors can avoid these issues and ensure their equipment lasts longer by employing proactive maintenance. Caterpillar’s SOMA (Site Operation Maintenance Advisor) reports that construction contractors can increase major component life by 62 percent simply by improving maintenance practices from average to excellent.
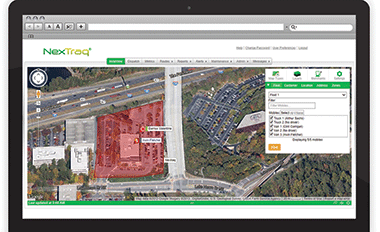
Well-maintained assets contribute to both a reduction in operational costs and enhanced employee safety. In contrast, construction equipment that is overused or improperly maintained can experience failure. In fact, more than 1,000 construction workers are killed each year from using machinery that malfunctioned due to lack of maintenance and repair.
Remote monitoring solution: Automatic maintenance alerts and maintenance schedules
A GPS tracking solution can provide remote monitoring with automatic maintenance schedules, logs and reports and offers an easy way to track maintenance automatically. These features can extend the life of an asset, save companies money on costly repairs and help improve operator safety. Alerts, which can be set based on engine hours or miles driven, can reduce equipment wear and tear, ensuring that the machines are running at their most productive and efficient levels.
Equipment Killer 2
Stolen or lost assets
Some pieces of equipment, such as expensive cranes, are left on jobsites overnight without supervision. These assets are a major target for theft. The National Insurance Crime Bureau’s (NICB) 2012 Equipment Theft Report states that annual estimates of the cost of equipment theft vary between $300 million and $1 billion. Wheeled machines and loaders are reported stolen most frequently, and the average estimated value of a stolen piece of equipment is $17,400.
If a piece of equipment goes missing from a jobsite, construction companies must compensate for the cost of replacing the asset and the lost revenue due to decreased productivity while that asset is unavailable for project use.
Remote monitoring solution: Remote asset tracking
Asset tracking technology allows construction companies to monitor their equipment in any environment, including remote construction sites, no matter how rugged the piece of equipment may be. A geofence, which is a virtual parameter, can be set up around a certain location. If assets move from that designated location, motion sensors within the hardware will trigger an immediate alert, which is sent directly to the project manager or designated contact. Alerts also can be set up for assets that are supposed to remain stationary. If the asset moves, management will receive an instant notification. This helps pinpoint the asset and stop unauthorized use or theft. If an asset is stolen, the tracking capabilities allow operations to return to normal as quickly as possible.
When evaluating GPS tracking solutions, companies should be sure the GPS hardware offers both cellular-based devices as well as satellite-only options. This ensures the assets can be found, no matter how remote the location. Contractors also should ensure that tracking devices are efficient and resilient enough to be installed on the outside of the asset and that they can withstand any type of condition.
Equipment Killer 3
Not monitoring asset extensions
If a construction company uses assets with functions that run off an auxiliary power source, the equipment manager may have information only on the usage and efficiency of the main motor, not the part of the equipment he or she needs to know about. For instance, if a company is using a cement mixer, they will need information both on the truck and the mixer itself. Though the truck may run efficiently, the mixer may not. Without a complete
picture of the efficiency of the entire asset, a contractor may not be aware that the mixer is experiencing problems.
Remote monitoring solution: Power takeoff sensors
Construction business owners can use power takeoff (PTO) sensors along with reports and alerts to monitor any extension of the vehicle used in the working process. For example, if the cement truck is idling but the cement mixer is being used, the equipment manager can see those details and gather a complete picture of asset operations. Managers can receive instant notification when employees engage the vehicle’s PTO mechanism.
In addition to standard vehicle data, reports provide information detailing the time, location and duration of equipment usage. This allows management to validate jobs by better understanding PTO usage and providing data on sensor activity.
Equipment Killer 4
Equipment deterioration due to adverse weather
Weather is unpredictable, and an unplanned storm or dramatic change in temperature can disrupt a project for the day. If certain pieces of equipment are left uncovered during severe weather, asset deterioration can intensify and lead to additional repairs or replacement. Without mobilizing certain equipment to prepare for adverse weather, the outcome will be out of management’s control.
Remote monitoring solution: Weather map overlays
GPS tracking and remote monitoring solutions offer features that allow construction business owners to use local Web map service (WMS) and overlay geographic information systems (GIS) maps onto existing maps.
When considering remote monitoring options, be sure your solution includes overlays such as temperature, Doppler radar and cloud cover. These features can ensure you are aware of imminent severe weather so you can
protect your equipment.
Equipment Killer 5
Delayed equipment updates from the field to the office
As a business owner or equipment manager, you may not be on the jobsite every day. If an asset is broken or experiencing problems, construction companies rely on employees to update the appropriate contact regarding needed repairs. While employees may make an effort to relay information about repairs, communication between the field and the office often is delayed. This can increase the downtime for an asset, reducing on-site productivity and endangering employees.
Remote monitoring solution: Mobile updates to the office
Many GPS tracking and remote monitoring systems offer features that allow employees to update the office quickly regarding the status of an asset via a mobile application or through the system. Such mobile applications allow workers to report maintenance issues using their smartphones or tablets, reducing the amount of time it takes for a machine to be repaired. Employees also can update odometer readings remotely, keeping equipment managers aware of needed preventive maintenance.