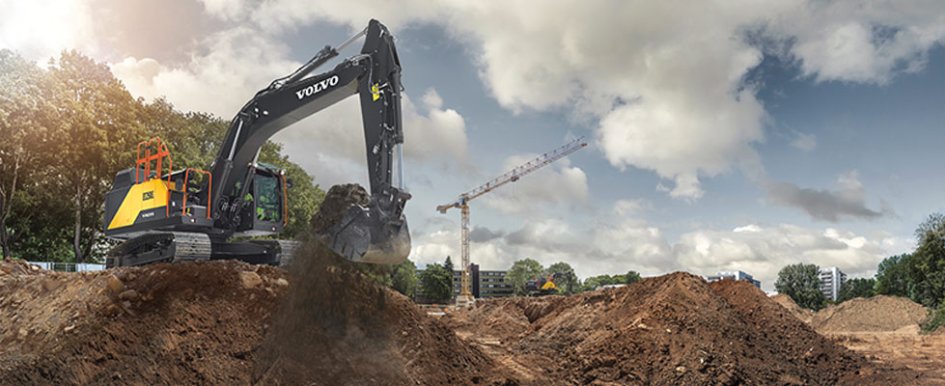
On today’s construction jobsites, it can be cumbersome to keep projects moving forward safely, quickly and in sync — but not if you have machines and tools that can help you orchestrate when, where and how you work.
It all begins and ends with data — from the inputs that indicate whether a machine is being operated safely to the back-end reporting that helps a fleet manager determine whether their company needs to upsize an excavator to fill more trucks throughout the day.
Understanding the various ways you can obtain, analyze and act upon machine data will make you a better business owner and support your bottom line. So let’s take a closer look at telematics, machine control, connected systems and some real-world examples of their use.
Telematics Should Be Foundational
Telematics-equipped machines provide the type of data that managers can use to make their jobsites smarter. That intelligence, in turn, helps make operators more productive while keeping costs down. It also helps ensure that everyone gets home safe at the end of the day.
So how do telematics systems work? They use GPS and other technologies to send and receive real-time equipment data that you can use to make more informed decisions. The data is analyzed and used to provide insights on everything from idle times and fuel efficiency to maintenance alerts that prevent costly downtime. They’re also what allow in-cab machine control systems to function.
For example, if a large amount of dirt or rock must be moved for the construction of a new highway, it’s important for the excavator(s) to load the haul trucks with optimized loads without causing the trucks to sit idle, waiting their turn. If these machines are equipped with on-board weighing systems, they can use telematics data to ensure optimal loads for every cycle. Real-time insights into the bucket loads can help operators eliminate overloading, underloading, reweighing and waiting — all things that waste time and burn excessive fuel.
Building Upon the Foundation
A system like this is only the tip of the iceberg. There are many others that help machines trench or grade more precisely, accurately compact aggregate or asphalt to target density requirements, map machine position to help prevent accidents and inefficiencies, and so on.
Machine control for excavators is a great example. Because excavators are used on such a wide range of construction and mining projects, they rely heavily on these systems for improved accuracy. There are simple functions that show operators on an in-cab display when target depth/slope levels have been achieved to prevent costly rework. There are also more complex functions like automated boom and bucket movements that make the digging process more efficient and accurate using a single lever. With these systems, excavator operators can complete various tasks with incredible accuracy in a fraction of the time normally spent using conventional methods.
Telematics systems are also used to optimize operations beyond automating machines; one example is the load-out process. You can optimize this process by digitizing the workflow from load order to load ticket. This connects the loading machine, the truck and the site office through real-time digital communication, which improves productivity and reduces costs for administration, misloads and fuel consumption.
To take it a step further, you can get real-time information shared directly to your mobile device or desktop to keep track of a range of activities, people, sites and/or machines — no matter the brand. Tools like these can help production managers, site supervisors and even subcontractors effectively manage different projects on a jobsite so that everyone stays on target and on budget.
Using Machine Data as a Teacher
One of the biggest advantages of machine control systems is that they help operators of any skill level or experience achieve higher productivity and efficiency more consistently — and they can do it much faster because the machines provide real-time guidance as they work.
From time to time, even experienced operators can get into bad habits and misuse their machines. But managers who use telematics can receive reports that include a rundown of potential machine misuses. They can see — by machine and for their entire fleet — instances in which an operator is doing something they shouldn’t, such as high-speed shifts on wheel loaders, using the wrong work modes on excavators and overuse of differential lock engagement on articulated haulers.
Catching operator issues like these can lower costs, increase uptime and identify potential training needs — all of which can help keep project costs down. And for those who worry about the risks of on-the-job training, simulation-based training and augmented reality can build operators’ skills effectively before they even hop in a cab.
The Impact of Data on Decision-Making
Telematics can also improve resource allocation of both machines and people, enabling more accurate budget forecasting. How?
For machines:
- They enable real-time tracking of equipment location and utilization, allowing site managers to quickly identify which machines are in use and which are idle. From there, machines can be moved around to different jobsites to optimize their utilization.
- By monitoring equipment health and performance data, telematics can predict maintenance needs to prevent unexpected breakdowns.
- Insights into how equipment is being used on-site can lead to better decisions on whether to rent, buy or simply reallocate existing machines. Telematics data can show if a piece of equipment is underutilized or overburdened, guiding these decisions.
For employees:
- Telematics systems can track the operation of equipment by different operators and help allocate the operators best suited for specific pieces of equipment or certain tasks.
- By monitoring safe operating practices and identifying potential hazards in real time, telematics can help ensure that safety personnel are positioned where they’re needed most to help reduce the risk of accidents.
For budget forecasting and planning:
- Detailed reports on fuel consumption, idle times, maintenance costs and more help site managers understand the true cost of operating each piece of equipment. This allows them to forecast budgets with more accuracy.
- Telematics data also provides insights into how long tasks actually take and the resources required to complete them. This helps fine-tune project scheduling and resource budgeting to reduce the risk of project overruns.
Navigating the Challenges
While telematics systems offer a wide range of benefits, they also come with some challenges. These systems collect a large amount of data related to equipment operation, location and operator behavior, which can make data security and privacy a concern. Robust encryption and secure data storage mechanisms are key.
Another factor to consider is the integration of telematics systems with existing technologies and workflows. Construction businesses often operate with a patchwork of software and hardware solutions, and integrating new telematics systems can be complex. Compatibility issues may arise, requiring additional resources or adjustments to ensure seamless communication between the telematics system and other operational tools.
The complexity of some telematics programs can also pose a challenge, especially in terms of the learning curve for staff. While these systems are designed to enhance operational efficiency, their full benefits can only be realized if operators fully understand how to use them.
To address this concern, some equipment manufacturers offer proactive telematics monitoring programs where the original equipment manufacturer and equipment dealer monitor machine data in real time for their customers and only report on critical issues that may lead to downtime, unsafe operation, etc. They also provide advice on ways to improve jobsite efficiency and productivity.
Any new technology or software comes with its own set of challenges — the good news is that heavy equipment manufacturers have years of experience with telematics under their belts. They continue to make enhancements and adjustments that are opening up this type of technology to more and more businesses. In most scenarios, the
benefits far outweigh the risks.
The construction industry is quickly moving into a new era powered by data and technology. For business owners and construction managers, embracing these changes isn’t just about keeping up with the competition — it’s about setting the pace. And those already seizing the opportunity are finding new ways to break away from the pack.