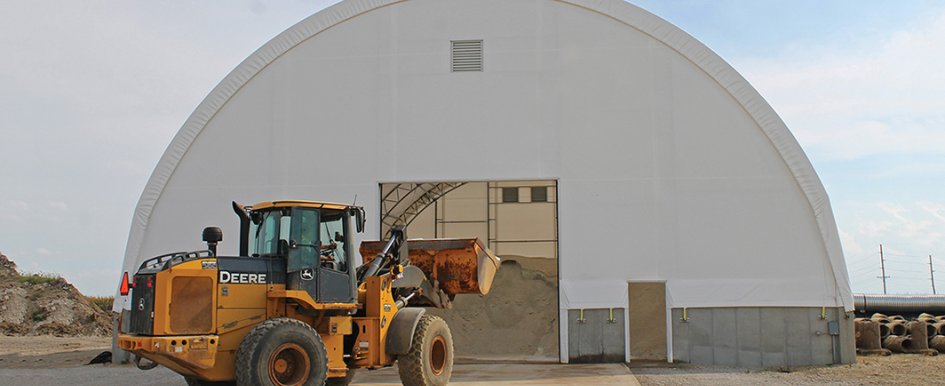
Construction companies maneuver around tons of challenges. Long-term projects can face shifting weather patterns and municipal regulations that make a construction job challenging, and in an industry that has long-term structural needs, construction companies have a variety of reasons to consider building a temporary structure that can follow a company to new jobsites. For companies that are on the move, a fabric structure is an exceptional option for long-term building projects, because it can provide durability and invaluable protection while also minimizing environmental impact.
Of course, the biggest benefit of having a fabric structure on the jobsite is being able to work through and provide protection during adverse weather. Instead of losing days of work during spells of rain, many contractors that have integrated a fabric structure are able to stay productive and keep their projects moving. While this is certainly a benefit to just about any building option, fabric structures separate themselves in a number of ways.
Overall, fabric structures are often preferred for jobsites because of their durability and quick construction time. The temporary nature of a fabric building can also help businesses avoid typical property taxes or lengthy municipal approval processes. These buildings take significantly less time to construct than traditional wood or metal buildings, which is an ideal building characteristic for construction companies that want to increase work and take on new jobs as quickly as possible. The entire construction process can take as little as a few days, whereas traditional buildings may leave businesses waiting for months.
Fabric buildings come with a variety of foundation options that make the building adaptable to many different terrains. Some foundations options for fabric structures include poured concrete, blocks, pony walls, containers, piers or anchoring systems. Each foundation option has its advantages. For example, construction businesses that require extra storage may choose to build on containers to add extra space for materials. Metal containers create a sturdy foundation that also provides a place to lock up tools and valuable equipment when the day is done.
Contractors tend to choose an anchor foundation when designing their structure. Anchoring systems generally don’t require excavation, and if excavation is required, it is minimal. Since there isn’t a need for poured concrete or other permanent foundations, once a structure has been removed, the jobsite can easily go back to how it was before the structure was erected. Anchoring systems are easily drilled into the ground and can be removed, ready to follow the company to the next site. Some companies even offer anchoring systems that minimize the environmental impact a structure will have.
A number of companies want to be noted as a green company—one that helps minimize environmental impact by using recyclable materials and sustainable practices. Such companies apply for Leadership in Energy and Environmental Design, or LEED. Fabric structures are environmentally friendly even beyond their anchoring systems, and can be an easy and effective way to improve a LEED score.
The fabric covering on these structures lets natural light filter through the material. This creates an environment that is well lit and doesn’t require electricity. This is not only a sustainable feature, but also one that lets companies nearly eliminate the monthly costs of artificial lighting. A number of companies also offer fabric covers that are made of recycled materials or are themselves recyclable, allowing them to be safely disposed of at the end of their life.
One of the greatest challenges facing construction sites is water damage. Water damage to building materials or during construction can negatively affect the quality of a project. When moisture compromises building materials, they must be dried, which delays work and lowers productivity. Water problems can be expensive to identify and fix once construction gets going, so finding an affordable solution, like a temporary fabric structure, can help save time and money.
Fabric structures can also help to reduce the accumulation of moisture that is inherent in so many traditional buildings. Traditional buildings are sometimes poorly designed, allowing moisture to collect inside. Fabric structures provide plenty of natural ventilation that allow the building to stay dry year-round. With design features, like open ends, extra large doors and roll-up sides, contractors can easily create a structure that won’t accumulate moisture. If that isn’t enough, an HVAC system or a customized ventilation system can be added to further combat moisture.
Construction companies have a lot of moving parts that make adding a temporary structure to a jobsite a smart choice. It is virtually effortless to design and construct a fabric structure, and while they can be reused and easily moved from project to project, they are durable enough to be used permanently. Protect materials, employees and increase workflow by considering adding a fabric structure to a construction site.