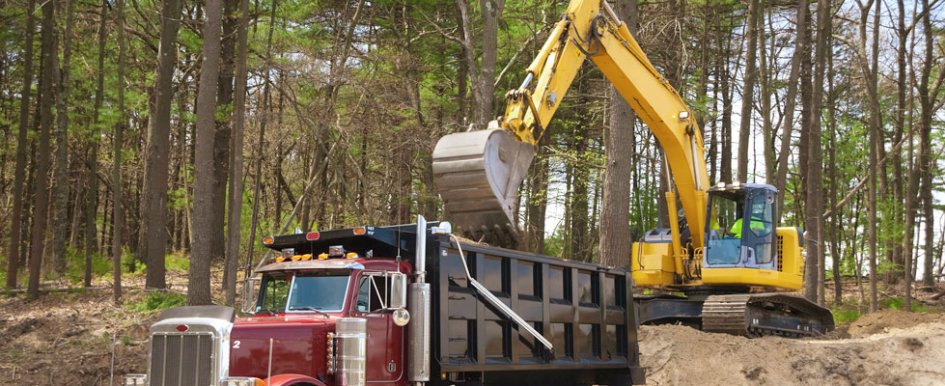
Maintaining asset visibility is one of the biggest challenges for construction fleet managers. Whether a manager is on the go, at the office or responsible for multiple locations, they must have a way to monitor assets in real time. While spreadsheets and whiteboards limit visibility and hinder communication, technology has made it easier for fleet managers to stay connected to their assets, equipment and team members.
The Power of Mobility
Technology has transformed the way our society stays connected. With virtually everyone having access to a mobile device, it’s easier than ever to communicate. Real-time communication enables fleet managers to monitor assets, collaborate with their team and measure key fleet metrics. Many business owners are taking advantage of mobile solutions like fleet and equipment management software. Eikenhout, a building materials provider that has been in operation since 1894, adopted fleet management software in 2016 and has used it to boost data visibility and ensure safety and compliance while streamlining collaboration on maintenance tasks.
As a building materials provider, Eikenhout operates over 160 assets across nine locations, including a variety of medium and heavy-duty trucks, specialized crane trucks, Moffett truck-mounted forklifts and SkyTraks. With many, widely dispersed assets, the company required a solution that would help them track assets in real time, automate maintenance workflows and improve team safety and compliance.
Although investing in software may seem like a substantial cost, an initial investment in construction fleet and equipment management software can produce a fruitful return on investment. Software provides increased data visibility, making it easier to manage daily operations and gain insight into maintenance, expense and performance metrics.
Uncovering Issues with Electronic Inspections
Staying informed of vehicle and equipment issues is difficult when you’re managing a dispersed construction fleet. Not having a solution to conduct inspections or waiting on operators to deliver paper inspection forms at the end of the week isn’t just inefficient—it can be costly. Issues can compound without your knowledge, causing extended downtime and expensive repairs.
Instead of waiting to sort through inspection results, managers can eliminate communication bottlenecks by having operators complete an electronic driver vehicle inspection report (eDVIR). Completing an eDVIR takes a fraction of the time of paper inspections and increases clarity in reporting by allowing operators to add photos and comments. Operators can identify issues and instantly relay information from the field to management or the back office.
Failure notifications allow managers to understand issues and launch maintenance workflows to avoid increased downtime. Going digital also enables managers to tailor inspection forms to specific equipment types. Having real-time inspection results with detailed, relevant information ensures you have all the information needed to manage repairs.
In addition to managing maintenance, eDVIR helps companies enforce safety measures and stay compliant. “Noncompliance is not an option for us,” said Curt Van Heuvelen, Eikenhout safety and training coordinator. “[It] is a very easy system to access and helps make sure we are compliant with government regulations.”
Tailoring inspection forms to cover specific criteria helps promote jobsite safety and compliance. To stay in line with government regulations, the Eikenhout leadership team created a custom form to ensure safety when bringing a piece of equipment onto a property.
Implementing a Proactive Maintenance Process
Yellow iron is expensive to repair, but it’s even more expensive to replace. Construction fleet managers know the importance of maximizing equipment’s life span, but keeping up with maintenance tasks is easier said than done when you’re juggling a dozen other tasks. Utilizing mobile software to keep up with maintenance tasks and stay informed of issues is the easiest way construction fleet managers can proactively manage asset maintenance. Software and mobile apps automate repair workflows and keep an organized record of service history.
One of the best ways to proactively manage vehicle and heavy equipment maintenance is to create preventive maintenance schedules in fleet management software. Managers can automate service reminders based on meter or time intervals. A notification is sent when service is due soon, allowing managers to schedule maintenance around project needs to avoid costly downtime.
“The system automatically generates service reminders based on a time or mileage schedule, so the manager or dispatcher knows it’s coming and can schedule that particular asset to be out of service on a particular day,” said Van Heuvelen.
Whether your team is conducting routine or emergency maintenance, collaboration is essential. While you can’t physically be everywhere at once, software allows you to collaborate with your team in real time and manage issues from anywhere. With software and a mobile app, your entire team can relay information instantly to solve issues. Users can comment on work orders, access service history and track issues from start to finish.
Fleet and equipment management software is a hub for all maintenance information, from work orders and issue management to expense tracking and inventory management. By managing asset maintenance in a single system, you can maintain a comprehensive view of operations and track expenses in granular detail or at a high level. Managers can calculate total cost of ownership and make data-driven decisions to improve their bottom line. “With just a few clicks we can get a lifetime cost for different assets within our fleet,” said Van Heuvelen, “We can identify which truck, trailer or piece of equipment is costing us too much money. It’s made the process much more scientific.”
Maintaining Visibility of Small Equipment & Tools
Construction fleet managers aren’t just responsible for rolling assets. Small equipment and power tools are just as important and treating them similarly to your equipment and vehicles ensures you maintain an accurate inventory count and keep your team productive.
Leveraging a solution that allows you to track both heavy construction equipment and small construction tools centralizes asset data helps to keep you well-informed. Managing the details of your tools and equipment with equipment management software provides comprehensive visibility and expedites processes like tool checkouts to increase team productivity.
Mobile equipment management apps enable operators to conveniently check out equipment without being particularly tech-savvy. Instead of paper sign-in sheets or cumbersome barcode scanners, operators can use their phone or tablet to scan equipment tags, barcodes, QR codes or near field communication (NFC) stickers. Once scanned, operators can quickly assign themselves to a piece of equipment and begin their day. Not only does this increase their productivity, but it also provides managers complete visibility into equipment status and records an audit trail of tool usage.
By overseeing operator assignments in equipment management software, you know where your tools are and who is using them at all times. Not only does this provide you with peace of mind, but it makes it easier to hold your team accountable.
Replacing a tool or piece of equipment may not seem like a big deal on its own, but prices add up quickly. With software, managers can easily see who used a piece of equipment last, and when items are missing or damaged, the right person can be held accountable. Centralizing small equipment data in software allows managers to easily control inventory and ensure accuracy. Managers can maintain a bird’s-eye view of inventory, including equipment location, status and value, in a configurable dashboard.
Whether you manage heavy machinery, small equipment or a mix of the two, leveraging technology is the best way to collaborate with your team and monitor your dispersed fleet. Aggregating fleet information in an easy-to-use software gives you the tools you need to increase efficiency and make informed decisions to improve operations and maximize your return on investment.