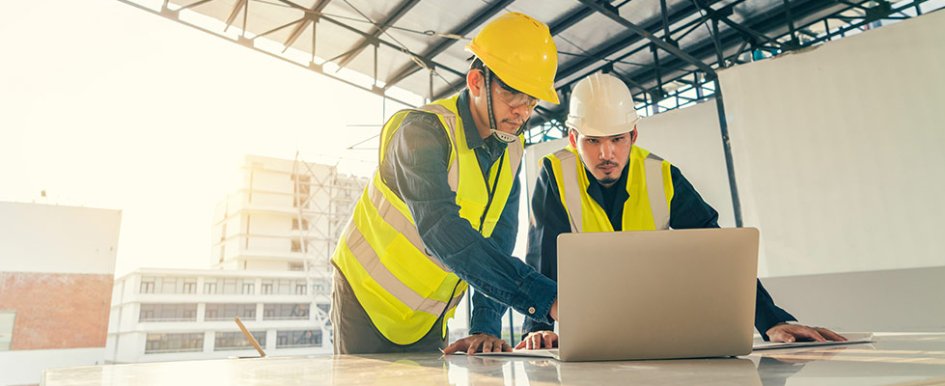
For decades, the construction industry has faced a steadily increasing struggle to attract and retain talent, but smart companies are recognizing that technology can be a big part of the solution. The lack of appeal among younger people — often driven by misconceptions — along with recessions, the pandemic and other factors have shrunk the available construction labor pool. Everyone from skilled tradespeople to CEOs are becoming harder to find.
At the same time, the volume of work available and needed is on the rise, particularly in infrastructure sectors. In some cases, contractors are passing on lucrative, well-funded projects because they simply don’t have the resources to complete them.
Long-term solutions to construction labor challenges will be multifaceted and take time to bear results. In the short term, most companies are actively enacting strategies to maintain or increase their workforce, and technology is at the forefront of those efforts. These companies understand that technology clearly allows them to do more with the same number of people. To the extent they can grow their workforce, it will also enable them to increase revenue and improve profitability. Technology is also emerging as an important recruiting and retention tool and a way to differentiate a company from its competitors in a tight labor market. Employees and potential employees, especially younger ones, are drawn to contractors who provide high-tech tools. In construction, that increasingly means software applications that make it easier to excel at satisfying, hands-on production and problem solving while minimizing paperwork and administrative headaches.
The key to doing more with fewer people is performing tasks as efficiently as possible and doing them right the first time. Nothing diminishes productivity like rework. Any technology that improves the efficiency and productivity of estimators, field managers, truck drivers and equipment mechanics is significant. The construction process starts with estimating. Since experienced estimators are one of the hardest talents to find in the current market, completing as many quality estimates as possible per estimator is vitally important. This is an area where specialized estimating software pays for itself almost instantly. Prepopulated cost databases and bidding templates, readily available cost history, automated error checks and professional-looking final estimates are just some of the many features of a well-developed and robust estimating solution.
All of this means that more estimates can be completed by the same number estimators without sacrificing accuracy and strategy.
Field foremen and superintendents represent another recruiting and retention challenge. Reporting on labor hours, equipment and material utilization and daily productivity is a necessary but significant time sink for these valuable employees. An automated field reporting system eliminates the time of handwritten field logs and timecards, moving information to the office and correcting data transfer errors that often show up in people’s paychecks or create inefficiency and rework in other workflows like scheduling and equipment maintenance. A good software solution makes it easy and fast to enter data via a laptop or tablet and to relay it seamlessly to the payroll and accounting systems
It is no secret that the nation is short of truck drivers. Without enough lowboy drivers to move equipment around, heavy civil field operations will not have the equipment necessary to complete contracted work. Switching to real-time, online scheduling software as opposed to relying on whiteboards, spreadsheets and phone calls allows the entire company to collaborate in assigning and dispatching equipment in a manner that minimizes moves. This in turn reduces the required number of drivers.
The hardest construction position to fill currently may be heavy equipment technicians. These highly trained mechanics are essential to keeping any equipment fleet operating. It is crucial that companies maximize their “wrench time” by reducing time spent preparing work orders and traveling.
Maintenance management software gives equipment managers the ability to efficiently assign mechanics, automates standard work order processes and has many other features to assist in fleet maintenance. The software also automates preventive maintenance, assisting teams in making sure that the work is done at the proper intervals. This supports a proactive culture that can actually reduce the overall volume of repair work — and therefore the number of mechanic hours — required.
These specialized software applications drive efficiency in individual workflows, as referenced above. In terms of doing more with less, the benefits increase even further when the applications work together as part of a cohesive software platform.
For example, estimating software can automatically retrieve and filter actual production rates from past jobs that were captured by field tracking software. This saves estimators a lot of time and makes them more accurate.
In the field, a superintendent who needs another crew or has a piece of equipment go down can inform the dispatcher or the shop manager via the field tracking software, reducing phone calls, voicemails and emails.
Scheduling and maintenance applications can inform each other when equipment is down for maintenance or when it is being assigned or moved. Electronic inspection forms can trigger repair requests automatically in the maintenance software.
These and other technology-enabled advantages make employees more efficient. They can also increase job satisfaction, making it more likely that talented employees will join or stay with a specific construction company or the construction industry in general.