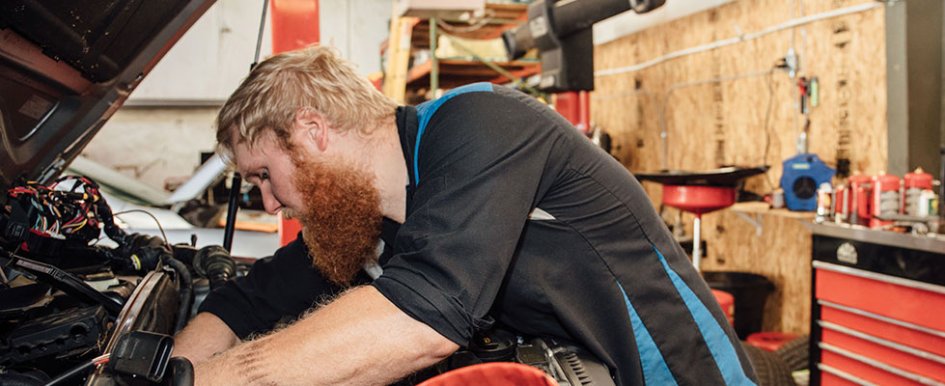
One of the greatest costs in operating a construction fleet is asset maintenance and repair. Coming in second only to fuel, service spend on average takes up roughly 22% of a fleet’s budget, according to Fleetio’s recent benchmarking report. But is it more cost-effective to manage maintenance and repair services in-house rather than working with third-party shops?
Like most things in life, the answer can be … complicated. While servicing assets in-house can be cost-effective for localized fleets, that may not be the case for those operating across a larger region. A lot of the deciding factor also depends on resources. Does the company have the facility, tools, labor hours and workforce to handle in-house servicing?
Chuck Metoyer, a veteran fleet manager, has experience on all sides. He moved from farming out all maintenance and repair services, then to a blend, and he finally settled to primarily handling everything in-house. “It was kinda rough [outsourcing] because I was just using an Excel spreadsheet to keep track of everything, [so it] was really, really hard to keep track of stuff,” he explained.
“Once we moved into this new building, we [had] our own facility here in-house, so we could do all the oil changes. That’s what I actually started out with at first. We’re not going to do any major work; we’re just going to do the oil changes, and we’ll farm out the major work to other shops.” This process was in place for about two years before Metoyer realized he could boost productivity by moving all maintenance and repair service in-house.
“The only thing I farm out now would be alignments and body work, and that’s it. Everything else is done here in-house.”
While choosing the option that best fits the fleet’s — and business’s — needs is largely situationally dependent, investing in moving maintenance and repairs in-house can pay dividends. Let’s look at a few pros and cons of in-house service.
The Pros
1. Better Operational Flow
Operational flow can be a “vibe” of sorts. It’s a rhythm that departments get used to and rely on. Performing services in-house allows the technicians and fleet managers to attune to that rhythm in such a way that it reduces productivity blockers. This includes things like ensuring optimal parts inventories, scheduling for minimized disruption and guaranteeing that priority service gets handled in a timely manner. Having insights to the whole fleet operation, from where an asset is located to where it’s needed and when, can help construction fleets schedule maintenance or repairs to improve both safety and productivity while minimizing the risk of further component damage.
2. Intimate Knowledge of Fleet Assets
Between technicians and operators, construction crews just know their assets better. That means when an operator hears a novel noise or feels a difference in a vehicle’s suspension, they’re likely to raise the issue. And because steadily employed technicians have likely worked on the vehicle before, they can easily determine the cause of the issue, especially with access to robust service data. This process becomes even easier for fleets using maintenance management solutions, like fleet management software (FMS) integrated with telematics, as they can reference sensor data associated with a particular issue and attach sensor data snapshots to work orders, expediting the service process.
3. Improved Cost Control
Your shop? Your rules. From parts purchasing to choosing shop equipment that streamlines operations — while helping to improve technician safety — to scheduling for minimal downtime, cost control is more in your hands when performing services in-house. Not only can you see and adapt to trends like poor-performing replacement part brands, but you can also invest in shop infrastructure that cuts down shop-related downtime.
“We used to waste a lot of time taking front rotors off the trucks. It’s a time-consuming job,” said Metoyer. “A vendor came in with a brake lathe that [let you] cut the rotors on the truck without taking it apart. That just cut that job down to half the amount of time it normally takes. We can do three or four in a day versus one.”
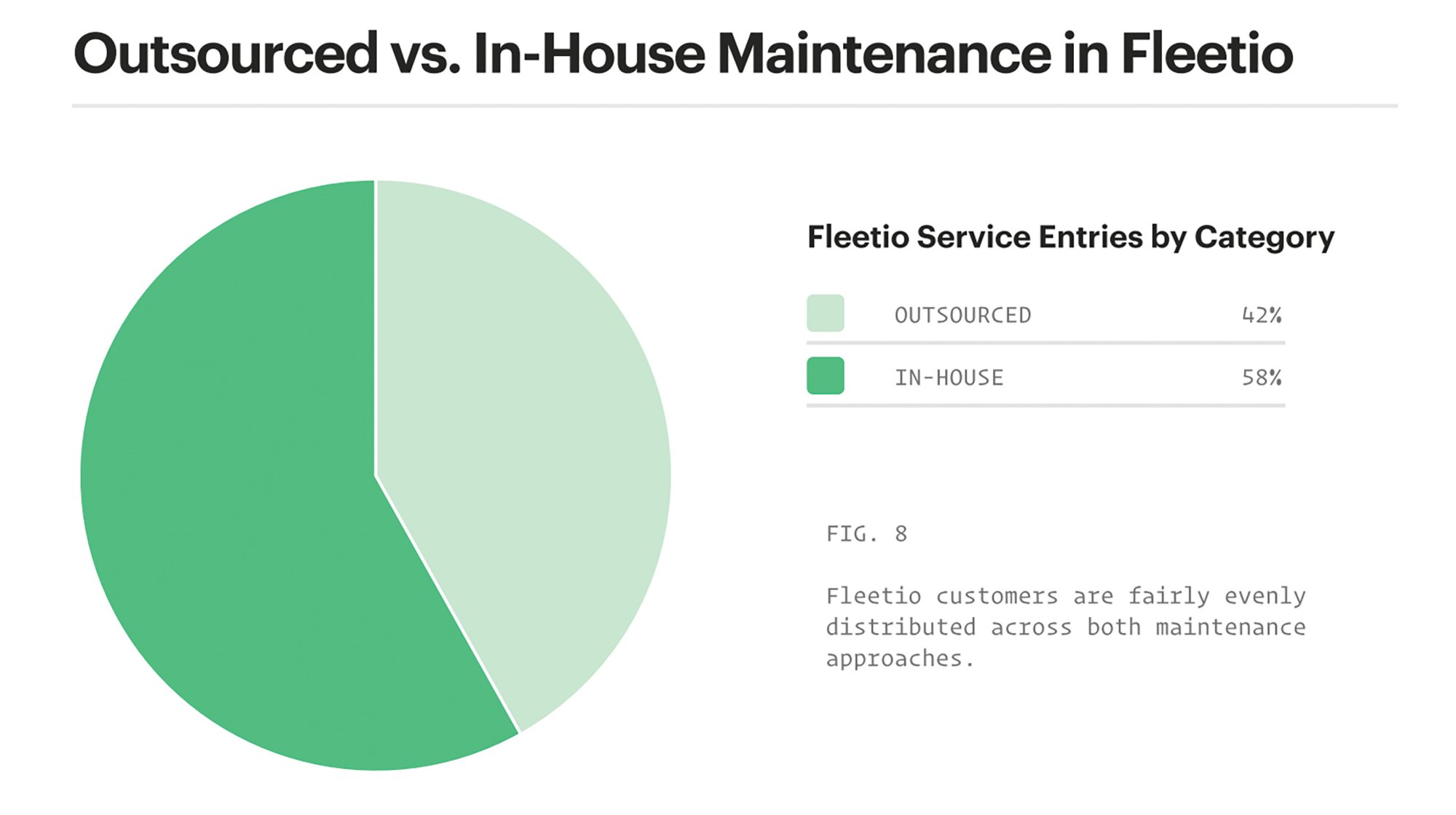
The Cons
1. Cost Barrier to Resources
At some point, everything comes down to cost. The difference is up-front versus long-term costs, and what makes the most sense for your operation. While potential savings through in-house maintenance and repairs are there for the taking, it’s also an investment in one capacity or another. Good technicians are worth their weight in gold, and retaining them — in addition to shelling out for any certifications you need them to obtain — is a necessary expense. Likewise, good equipment and tools are also a necessary expense. Outsourcing maintenance and repairs services, conversely, can help fleets save money through tiered discounts and removing the need for cutting-edge tools and equipment.
2. Cost-Attribution Challenges
According to the aforementioned benchmarking report: “Because maintenance and operational costs are so closely tied together, it may be hard to mitigate one without impacting the other.” An asset’s health can impact a project’s timeline and even drive up fuel expenses — which already makes up a whopping 50% of the fleet budget, on average. To determine service-specific costs and how they impact other aspects of the business, total operating costs must be taken into consideration. Without an efficient way to collect and aggregate this data, accomplishing cost attribution can be difficult. However, fleets can use FMS to collect, consolidate and aggregate fleet data, including total cost of ownership, to quickly determine and address issues driving up service costs.
3. Limited Flexibility
When managing asset service in-house, there may be limited flexibility around maintenance scheduling, addressing priority repairs or both. This can play a heavy role in extended shop-related downtime, leading to missed project deadlines and overtaxed techs. On the other hand, farming out specific maintenance services or emergency repairs can provide more flexibility and a quick turnaround so operators can get back on the road or to the jobsite.
Determining whether to service assets in-house, through a third-party shop or by using a combination of both really depends on your operations, availability of resources, short- versus long-term goals and, of course, budget. While making the switch is something that can be planned for in advance, consider the pros and cons and where your fleet fits into that matrix. As a significant cost center for construction businesses, minimizing fleet costs while maximizing safety and uptime are paramount to getting jobs completed on time.