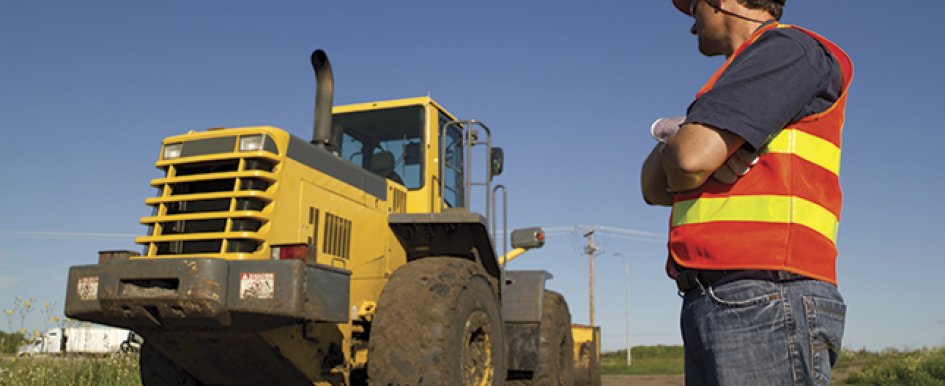
As technology continues to evolve, the construction industry evolves with it. Whether it's the latest in mobile communications, building materials and design, prefabricated and modular construction, laser technology or safety equipment, new technologies can provide more efficient, safe and cost-effective ways of operating your business. Technology can also dramatically change a contractor's risk profile and create the potential for unforeseen liabilities.
The importance of fleet management in the construction business cannot be overstated. The risks associated with transporting materials and equipment, moving workers to and from jobsites and traveling long distances to more remote locations are wide-ranging. In fact, according to the Bureau of Labor Statistics, transportation \uc0\u8232 incidents were the second-largest cause of workplace deaths in the construction industry in 2013, representing more than one-fourth of all fatalities.
Other data shows that a disproportionate amount of construction large-loss activity results from auto-related exposures. Auto liability cases generate umbrella layer exposures for contractors more than any other line of business. The implications of fleet-related exposures extend well beyond the impact on a contractor's loss experience, so it is important that contractors proactively manage these exposures.
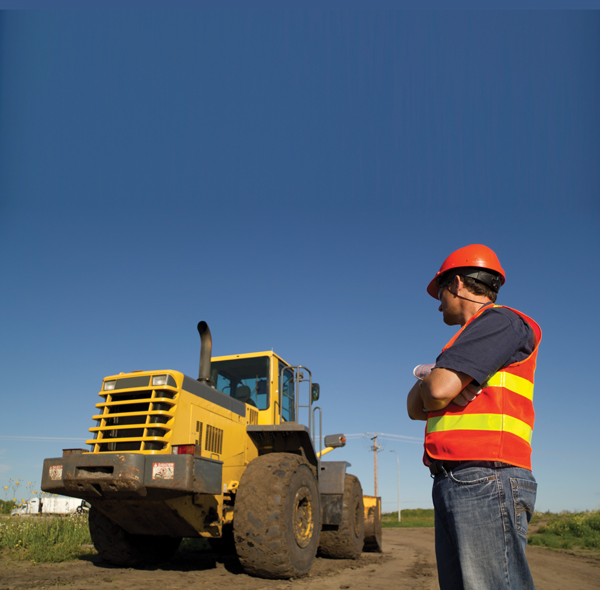
Advancements in telematics technology are changing the way construction companies approach fleet management. While many companies have increasingly adopted this technology to monitor vehicle location, performance and driver behavior, and realize benefits such as improved fuel efficiency and the promotion of safe driving habits, there are still many companies who are unsure of how to incorporate this newly available data into existing fleet management programs.
Even more companies are unaware of the potential liabilities associated with the availability of this data and the increased standard of care they may now be expected to employ with regard to safety issues uncovered. Taking full advantage of these systems can help business owners improve their fleet management strategies and potentially their bottom line, but only if careful approaches to managing the associated risks is an integral component of the overall strategy.
Telematics Implementation
Before using telematics, construction business owners should educate themselves about the products available. They must also develop a clear objective of what they are looking to accomplish by using telematics and having a clear strategy of implementing a telematics system. Is the primary focus to better manage vehicle maintenance; identify more efficient opportunities to move materials, equipment or workers from jobsite to jobsite; manage driver behavior; or all of the above?
Regardless of the intended purpose, a contractor should have a clear objective as the first step. Once the purpose is clear, a contractor's implementation strategy should include capture, analysis and management of the data, as well as application of the findings.
Transparency is a vital component of any implementation strategy. Being open and honest with drivers can help the rollout and secure buy-in. Getting employee feedback and buy-in at the earliest stages is an important step to help avoid eroding trust.
When explaining telematics to employees, it is essential to communicate that an effective program will recognize good performance with positive feedback, rewards and praise. Furthermore, in the event of management receiving a complaint about an incident or a driver, telematics data can help exonerate that person and verify his or her version of an incident. Drivers can benefit in other ways, too, including better communication with the company, navigational support and apps to make their work more efficient. Making drivers aware of these benefits can also help gain their acceptance.
Data Management
Specific telematics products can vary, but in general, the systems can provide detailed information about routing, engine performance, fuel economy and driver behavior. Remember that implementing a telematics program requires not just an investment in technology, but also an investment in a safety and risk management strategy. It may take time working with the telematics provider to achieve the right level of data for a construction business owner to derive meaningful trends and insights.
Once an owner organizes the driving data to meet company needs, the next challenges are interpreting the data, making the results actionable and consistently enforcing the driver safety program throughout the entire organization. The approach will be different for every fleet, and having a clear understanding of your objectives can help you develop the right plan and level of accountability.
For example, accelerometers built into many telematics devices measure risky behaviors, such as speeding, hard braking and fast turns that can lead to accidents. When aggregated, this data can be useful in understanding drivers' behaviors and identifying those who may need coaching. In addition, it creates the opportunity to intervene if the data suggests unsafe driving behaviors or vehicle use outside company guidelines. In these situations, it supports a risk manager's ability to take prompt steps to enforce driver safety protocols and a consistent system of accountability for all violations of a company's driver use policy.
Construction business owners should designate an internal point person who understands the company's telematics system, the company's vehicles, its drivers and their daily activities. This designated person should review the data and relay the relevant findings to managers, and be able to identify which situations warrant coaching and which warrant intervention.
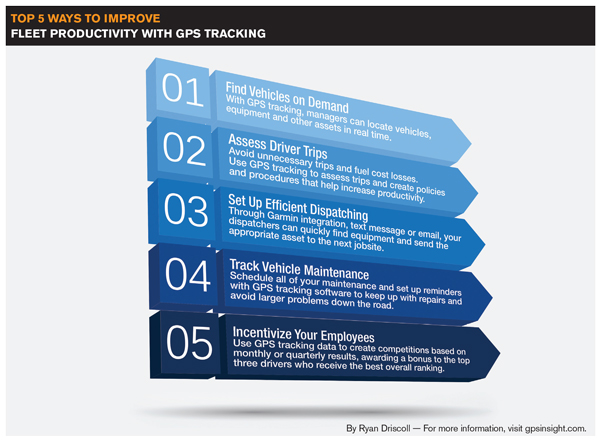
Driver Coaching
When construction managers deliver feedback about performance data to drivers, they have a valuable opportunity to influence individual conduct. Improving drivers' skills by providing feedback to all drivers, even when they don't exhibit risky behavior, may elevate the entire fleet's performance and risk profile. Furthermore, providing feedback to all drivers can help eliminate any stigma felt by those identified as needing improvement. Providing feedback is a best practice that can lead to significant results.
Specifically, a 2014 report from the Federal Motor Carrier Safety Administration supports the conclusion that driver awareness alone does not change performance. Instead, companies should combine it with sustained and consistent feedback to all drivers. The study involved monitoring driver performance and fuel efficiency for a fleet of 46 heavy-duty trucks—a mix of day cabs and sleeper cabs—for a year, encompassing more than 50,000 driver hours. While all drivers involved were monitored, only certain ones received feedback, coaching and, at certain points of the study, financial incentives for good behavior. The study showed that when drivers received feedback about their driving performance, the frequency of unsafe events decreased by almost 50 percent. As an added benefit, it was also shown that fuel economy improved by up to 9 percent.
Commercial fleets were the early adopters of vehicle telematics and on-board monitoring. Over time, these companies learned the important lessons of building effective telematics safety programs. Construction companies adopting these systems can greatly benefit from this knowledge. The mistake that many companies continue to make is assuming that simply implementing the monitoring aspect of telematics will improve driver behavior.
Working with an insurance carrier that specializes in construction risks and understands how emerging technologies impact a contractor's risk profile is an effective first step in planning and implementing a telematics strategy. This includes insights on effective hiring practices for those employees who will drive vehicles, training programs on data analytics and interpretation, and other best practices to get the most out of these systems.
Without a well-defined strategy, including updating driver-use policies, obtaining employee buy-in, empowering risk management professionals to address unsafe behaviors, and incorporating feedback and coaching, a telematics system is less likely to have a positive impact on safety and could become a lost opportunity for construction managers.