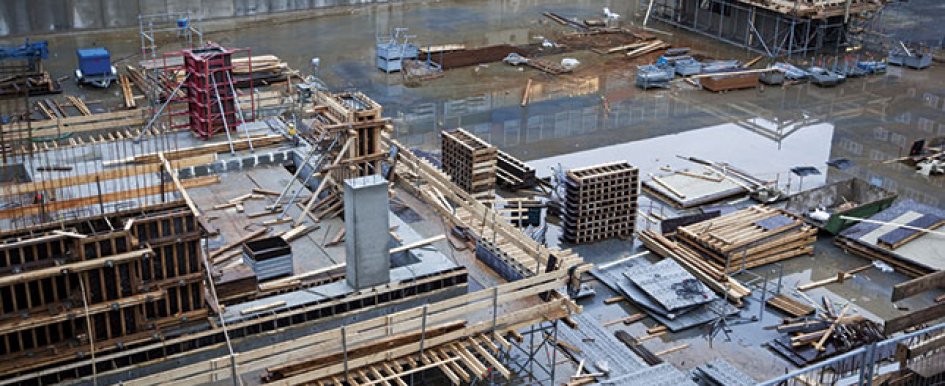
Every contractor and construction professional knows the three top priorities of a project: Finish on time, finish on budget and maintain profitability. Professionals also know that countless threats endanger each of those priorities. Water damage, for example, is a high-risk threat that can delay a project, incur significant expenses and damage a contractor’s reputation. Understanding both the risks associated with water damage and best practices for mitigation will help contractors effectively manage and reduce their exposure to these risks.
Consequences of Water Damage
Finishing on time and remaining within budget present an uphill battle once water damage has occurred. Not only are you compelled to potentially employ a crew for longer than expected, but the start date on future projects could also be pushed back. In addition, contractors may face expenses associated with cleanup and rebuilding. Those costs can include renting additional equipment to remove damaged materials, replacing raw materials and securing equipment and specialists to expedite the process of drying impacted areas. Even though many of these costs may be covered by insurance, contractors often incur additional expenses that can impact their profitability. If a project has been delayed and pushed over budget, it can become a black mark on an otherwise spotless reputation.
Prevention and Mitigation
Water damage losses can be caused by a number of events, from unprotected openings that expose contents and property to the weather, to failed pipe sections or incomplete drain fittings. The extent of damages is usually determined by the time it takes to detect the situation and the water’s ability to move through the structure and cause damage, both horizontally and vertically.
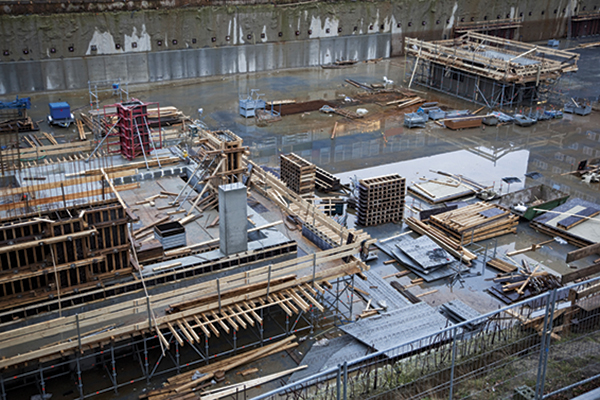
Three straightforward best practices can help manage risks associated with these common exposures: conducting tests and inspections, utilizing available protective resources and engaging the right professionals.
Conducting Tests and Inspections
While water damage can be triggered by weather, it can also be the result of incomplete pipe installation and preparation. For this reason, contractors should ensure that pipes are always closely inspected and tested before water enters the system. Pipe joints are particularly vulnerable depending on the way they are built. Increasingly, joints are being crimped rather than soldered, and while crimping can be effective, it makes quickly performing a visual check to ensure the fitting was made properly more difficult. For this reason, some contractors have moved to a marking system for tradesmen to indicate that the crimp has occurred. No matter which joint method is used, an air test can help identify incomplete fittings and other issues before water enters the system.
Engaging a quality control inspector to thoroughly inspect the pipe systems is also important. Beyond the air test, inspectors will know where to look for weaknesses in the pipe system and can determine whether any rework is needed before running the water. While this might not be required by local building inspectors or code officials for every job, it is an easy step that can help decrease the risk of water damage and provide significant piece of mind.
Tests and inspections of pipe systems are more than simple boxes to check on a contractor’s to-do list. They are an early defense against water damage and should be treated seriously. Before running water through the system, an on-site manager should be required to approve any and all pipe tests.
Utilizing Resources
Even after pipe systems have been test-d and inspected, a water incident is still possible. However, some simple solutions can help contractors avoid and minimize damage.
Contractors can avoid water damage by protecting exposures both when the construction crew is on-site and when the jobsite is unmanned. In the face of bad weather, install a sturdy, secure, temporary roof over elevator shafts, stairwells, tower-crane openings and mechanical openings.
Installing drain screens is also imperative, as drains can become clogged by debris entering the drain system, and plugs of debris can create physical shock as they move through the system, ultimately causing pipe joint failure.
Floors also should be protected by maintaining waterproofing and sealing floor penetrations. If floor penetrations, such as elevator shafts and stair towers, are left open, they should be diked to prevent water from flowing from one floor to another.
These measures can go a long way in protecting the project from water damage associated with pipe systems failures and extreme weather. However, even with all of these practices in place, contractors should use technology to help detect these events.
Monitoring systems have evolved in recent years to be more dependable and cost-effective. The protection they afford a construction site can far outweigh the cost to purchase and monitor these devices.
Flow alarms, for example, can help identify pipe system issues. Water flow that is detected through the pipe when it should not be flowing at all signals an alert. This notification draws attention to what has gone wrong, and it can also identify where the issue has occurred. Other alarms will signal when water has reached a specified depth on the floor of the basement, at the bottom of an elevator shaft or in another exposed area. The benefit of these alarms is that you will be notified of flooding, even if it has nothing to do with the pipe system.
These alarms can also help you monitor other water threats throughout the duration of the project. For example, wireless central station electronic monitoring systems are a relatively small, one-time investment that can be moved between jobsites and that monitor for not only water, but also theft and vandalism. Given that an undetected water damage claim can cost millions of dollars, a monitoring system is a smart, low-cost investment.
Engaging Professionals
When it comes to risk management, contractors can benefit from working with a risk management professional who can help identify and mitigate risks specific to your jobsite and project. When negotiating a construction budget, working with a risk professional to conduct on-site assessments can be included and accounted for in the budget.
The client, who wants to get the project completed on time, will understand the benefits of hiring these professionals. Your insurance agent or broker and insurance carrier should have risk control professionals on staff who are well-versed in your industry and able to make recommendations to help you avoid certain exposures.
While water damage is not a new risk to the construction industry, contractors must fully understand its loss potential in order to protect themselves against it. After all, finishing on time, on budget and making a profit are goals that should not be left to chance.