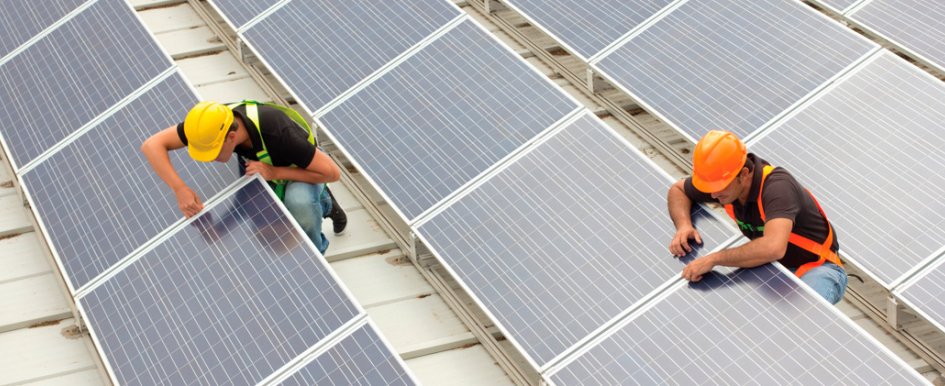
The interest in rooftop photovoltaic (PV) system installation continues to steadily increase. The growth of the solar industry has led to an investment of more than $17.8 billion in 2014. Last year alone, the U.S. solar industry installed more than 30 percent of all new electricity generating capacity—second only to natural gas. Some of the most active solar users are many of America's most well-known companies, including Walmart, Apple and IKEA.
While the contractors see that the benefits of rooftop PV systems are many, few have actually overseen these installations and may not fully comprehend the scope of the process. Understanding potential installation risks is crucial to ensure rooftop solar systems properly provide safe and efficient power.
With contractors, taking on more solar projects, it's important to consider the risk involved, whether you are a one-man operation or a multi-million-dollar firm. To address this topic, CBO spoke with Eileen Kauffman, leader of Travelers Renewable Energy Practice (travelers.com). Kauffman is responsible for coordinating Travelers' five renewable energy businesses, which underwrite risks related to multiple sources, such as wind, solar, hydro and clean technologies. Kauffman's responses below detail the steps involved in taking on a solar installation project and why risk and insurance considerations are so important.
CBO:What should construction managers do to reduce potential risks on a solar project?
EK: Construction managers can reduce potential risks by exercising due diligence in planning the work, including pre-design and pre-installation assessments, proper selection of vendors, evaluating third-party contracts and understanding various building codes and requirements for the design and installation phases. Other planning actions to consider include:
- Structural assessment to determine whether the roof and structural framing can support the new load—both the dead load and the loads imposed by wind
- Appraisal from a roofing consultant or manufacturer to determine the remaining service life of the existing roof—the PV system could last for more than 20 years
- Roof check to verify that the PV installation will not void the roof warranty inadvertently
- Consulting the service contractors who maintain rooftop equipment, such as heating and air conditioning units, and ensure that the PV design incorporates and maintains safe, adequate access
- Electrical compatibility check to confirm the existing electrical system will accommodate the PV installation and support the new electrical load
- Contact local fire department or with local building code officials about specific code and zoning requirements, fire codes, and obtaining the necessary building permits
- Weather-related risk assessment for potential hail damage, lightning strikes or snow accumulation that could heat up and slide off the roof
CBO: How should contractors approach managing rooftop solar systems?
EK: Travelers breaks down construction considerations for rooftop solar systems into three phases—design, installation and ongoing maintenance. While there is some overlap with these risk considerations, it is essential to devote appropriate time to consider them at each phase and how they can have a direct impact on the building hosting the PV system, or the people working on or around the system. No construction manager should progress to installation without devoting significant time to up-front planning, subcontractor selection and negotiation of contract terms and other agreements.
CBO: How should managers deal with licensing requirements and certifications when evaluating subcontractors and other third parties?
EK: Selecting subcontractors and third parties is one of the most important aspects of any PV project because the solar provider or engineering and procurement contractor (EPC) controls the overall quality of the installation. Before any work begins, it is important to conduct background checks on the solar installers. Ask for references and then interview potential candidates about safety and quality control. A written safety program is a good reference document, but businesses also need to be sure the installers have a safety-first culture.
As a first step, construction managers should ensure all necessary licenses and certifications are current. The solar industry is relatively new and therefore only a few states have licensing requirements for trades, such as electricians and roofers, involved in photovoltaic installations. Consider selecting professional installers certified by the North American Board of Certified Energy Practitioners (NABCEP), a trade organization for solar installation contractors. NABCEP certification can help identify contractors with the technical and safety knowledge and skills specific to solar installations, and should instill a higher degree of confidence. Construction managers can also consult references or contact the local building department and inquire about the department's experience with particular installers or subcontractors involved.
CBO: What agreements should managers have in place with solar installation companies and subs?
EK: Ultimately, construction managers can be held responsible and financially liable for mistakes made by solar installation subcontractors and other service providers. In order to minimize their exposure, construction managers should draft a written agreement that addresses the risks involved in the installation and maintenance of a solar array—sometimes referred to as "contractual risk transfer"—confirming how the construction manager and their subcontractors will take responsibility for claims and damages resulting from the work. Legal counsel should review all contracts, including:
- Indemnification agreement
- Insurance requirements, including detailed types of coverage required and minimum insurance limits needed
- Certificate of insurance
- Terms requiring use of fall protection and plans for safe roof access
Construction managers must also ensure that subcontractors have their own workers' compensation insurance in the event of an injury.
CBO: How should managers counsel developers and property owners on ongoing maintenance?
EK: Inspection is critical to a solar PV project. Managers should consider hiring a third-party engineer to serve as a witness or inspect the PV system to account for any discrepancies, from initial design to final installation.
Once installed, a proactive management program should include ongoing inspections and maintenance to help insure the overall reliability of a PV system. While a solar array does not have moving parts like a wind turbine, these systems are exposed to constantly changing environmental conditions, such as ultraviolet light from the sun, extreme temperatures, high winds, heavy rain, blowing snow and hail.
Maintenance is more than washing dirt off solar modules. Visual inspections should identify defects, such as discoloration, delamination and broken glass, as well as excess soiling, bird droppings, and removing accumulated leaves or debris from the roof. Inspections should check the racking and mounting systems for corrosion, sagging and any movement across the roof.
To ensure devices are not creating abnormal heat that could cause premature failure or become a fire hazard, inspections should also include opening up combiner boxes to look for any corrosion, and performing thermographic scans of inverters, combiner boxes and disconnects.
As with any contingency planning, working with the local fire department officials as partners prevents a small fire from turning more serious and establishes sound procedures. Businesses should provide emergency responders with system drawings that clearly identify the location of any rapid shutdown equipment, disconnects and ladder access points.