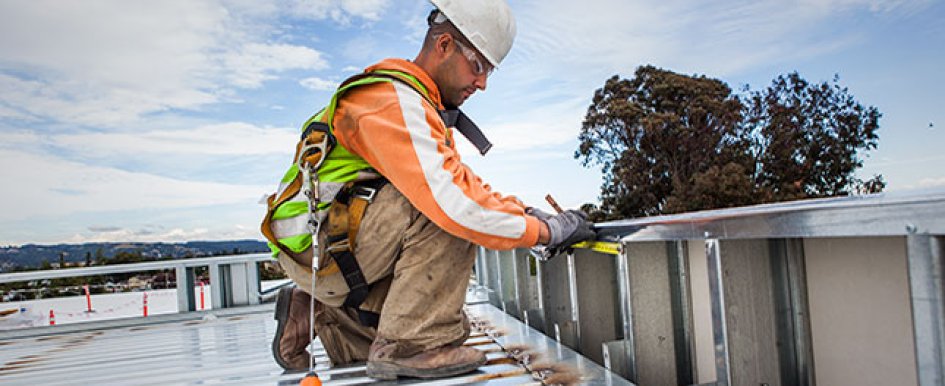
A CEO friend of mine was trying to exit a hotel. As he emerged from the designated exit stairway, he almost fell into a hole and tripped over construction debris. Spotting a contractor foreman, he reasonably pointed out that the workers were violating a host of OSHA and local codes and that the head of the state’s OSHA agency was actually meeting with his supervisors at that same hotel. This moment of politeness was greeted by an expletive and then dismissed. When the CEO returned to his office, he asked his construction managers if they had heard of the contractor. “Why, yes,” they responded, “we use them a lot.” The CEO’s response? “Not anymore.”
Many employees work alone at a customer’s site with no immediate supervision or safety professional to check for hazards and ensure professionalism. Many employees, such as journeymen electricians and certified crane operators, are trained to operate with minimal supervision. Other workers may be less equipped to individually analyze their settings. Unfortunately, both types of isolated workers may violate OSHA standards or act unprofessionally, as in the case of the soon-to-be ex-foreman mentioned above. Preventing that misconduct is more of a problem when employees—even those who are experienced—are working alone. In fact, the majority of the nearly 500 workplace fatalities I’ve managed involved experienced employees, not new hires. Experienced workers may become lax about hazards, or when fatigued, lose sight of good judgment.
An employer has some level of duty to protect its employees whether they are on the employer’s work site or working elsewhere. The employer cannot delegate this responsibility to others even when another employer controls the work site. The employer retains responsibility to protect its people—even highly skilled workers who are trained to operate alone. OSHA can cite multiple employers on the same job. For example, OSHA might cite the work site owner for creating the hazard and the actual employer for allowing its employee to be exposed to the hazard. However, a contractor can’t send a safety manager to conduct a site safety analysis at every power pole, ready-mix delivery or work site where skilled craftsmen are working alone.
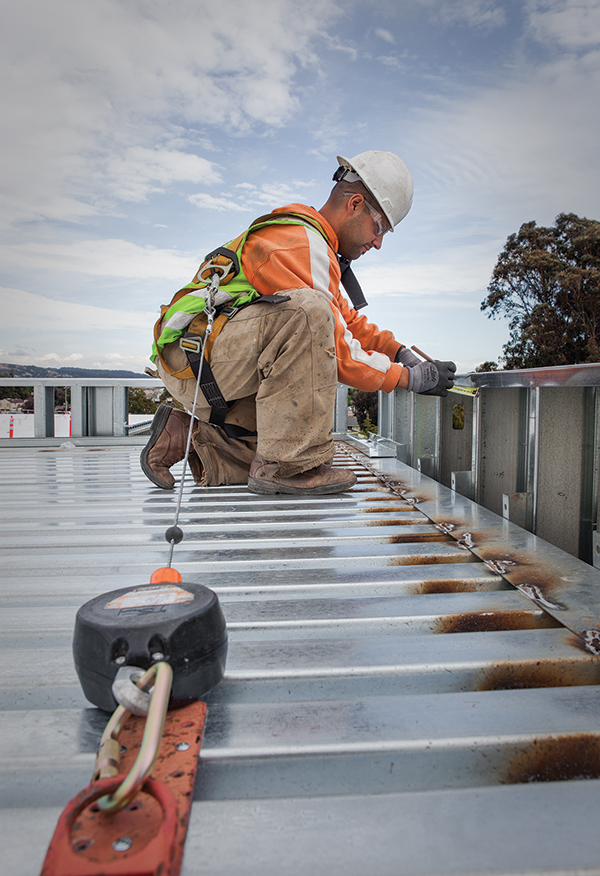
If an accident occurs, OSHA will ask the employer many of the same questions that it would ask if the employer controlled the work site or had a supervisor present: Who did the site safety analysis? How did you monitor employees and ensure that they used fall protection? Did you conduct a pre-work meeting? When did these employees last attend a safety meeting?
You may assume that employees confer throughout the day with supervisors, dispatchers and technicians. You may have trained employees to exercise greater responsibility when working alone, but are these procedures documented? To ensure your employees maintain safe and professional conduct while on the job and to avoid violating OSHA regulations, follow the steps below.
Step 1: Train Employees To Use Good Judgment.
Employers should hold classes on using good judgment. Every day, employees work with inadequate personal protective equipment, don’t tie off, engage in horseplay and harass fellow coworkers. Employees write things in emails that are discoverable, will either be misconstrued or never should have been put in writing. You won’t be able to teach good judgment to some employees, but most employees will improve their judgment if the employer regularly discusses jobsite hazards and the employees’ roles in making wise decisions. Employers who conduct root cause analyses of accidents often determine that poor decisions were a major contributing factor. Share practical examples and stories so that the employees may learn a lesson without actually committing a foolish act.
Step 2: Determine Why Experienced Employees commit unsafe acts.
Beyond root cause analysis of misconduct, consider the psychological and cultural reasons for unsafe acts. As an example, studies show that the brain loses the ability to use good judgment in matters involving safety when a person is tired or has low blood sugar from skipping meals. One study documented that employees are more prone to engage in harassment when fatigued. Regularly remind employees that they are not considered tough when they skip sleep, disdain healthy eating habits or stay out all night—they are an unacceptable safety risk. Also explain that a majority of accidents are due to rushing, frustration, fatigue, complacency and failing to stay on task.
Step 3: Create a Mindset that encourages Employees to Do a Quick Hazard Analysis.
Continuously remind employees to always pause, consider the site or job hazards and take steps to avoid the hazards. That’s how we expect all employees to operate, but with isolated employees, you must especially emphasize this behavior. Devise processes to make this response automatic. One employer described the TRACK mantra their employees follow:
- Think through the task.
- Recognize the hazards.
- Assess the risks.
- Control the hazards.
- Keep safety in all tasks.
Step 4: Develop General Procedures for Remote Workers.
Under construction OSHA standards 1926.20 and 21, an employer must:
- (20(b)(2)) maintain accident prevention programs providing for frequent and regular inspections of the jobsites, materials and equipment to be made by competent persons.
- (21(b)(2)) instruct each employee in the recognition and avoidance of unsafe conditions and the regulations applicable to his work environment to control or eliminate any hazards or other exposure to illness or injury.
So, how does an employer meet its obligations when no supervisory or safety personnel accompany the workers? Possible actions might include:
- Document thorough job-specific training to equip the employees to recognize and avoid hazards.
- Determine the probable range of hazards employees may encounter at various types of jobs, and document that analysis actually took place. Many jobs and sites are similar, so determine the routine hazards. Go one step further and consider non-routine hazards.
- Establish a rule, procedure or form that requires supervision to pause when assigning employees to non-routine jobs or to jobs with which they are less familiar. In these situations, additional training or some type of safety analysis may be necessary.
- Require employees to complete a short and basic site safety analysis for small, remote jobs.
- Consider using tablets or phone apps for the hazard analysis and as a means of tracking compliance and providing advice.
- Establish and emphasize procedures for employers to call in when they have any questions or concerns.
- Consider whether spot checking line crews, technicians, deliveries or small crews is feasible. Do you do any sort of quality spot checks or inspect final work?
- Consider safety concerns unique to each site, such as lockout for electricians, skylights for those working on roofs or overhead power lines.
- Job safety analyses must be thorough and accurate and should consider challenges posed by customer sites.
- Sometimes a customer may rush employees or ask them to cut corners, so make sure your employees know that you will back them if they refuse unsafe demands by customers.
- Conduct regular teleconference meetings for remote workers.
- Safe behavior starts at home, so remind employees to practice the same safety skills at home as they do at work. Educate employees on 24/7 safety hazards, because your ultimate goal is to get employees to change their mentality so they actively think about promoting safety wherever they go.