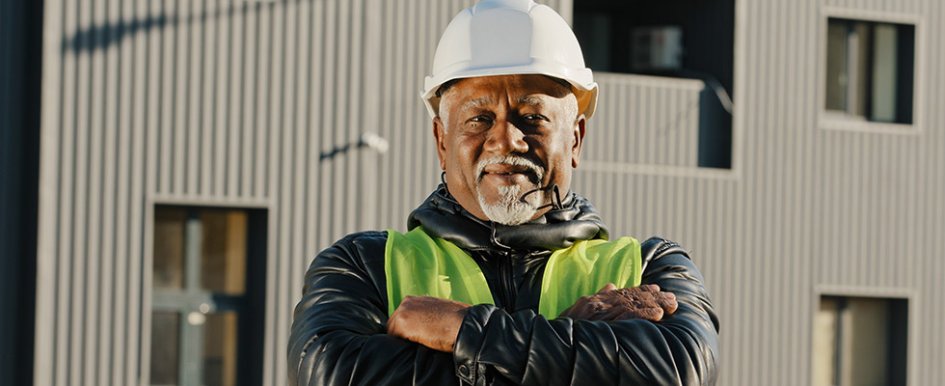
The U.S. engineering and construction (E&C) industry began 2022 on a bright note after achieving strong growth of 8% in construction spending in 2021. While the value added reached $1 trillion in second quarter (Q2) 2022, gross output stood at $2 trillion in Q2 2022 compared to $1.9 trillion in Q2 2021. But a closer look at current market dynamics suggests that 2023 will likely experience differentiated growth rates across different industry segments.
On the one hand, the nonresidential segment is likely to be buoyed by funds entering the market from the Infrastructure Investment and Jobs Act (IIJA) and the CHIPS and Science Act of 2022. The CHIPS and Science Act provides $52.7 billion for American semiconductor research, development, manufacturing and workforce development and is expected to drive construction in 2023 and beyond.
On the other hand, residential construction companies are relatively more pessimistic about the industry outlook for the next year compared to other segments. The residential segment may witness sluggish growth due to weakening consumer demand. So, while some segments may be more bullish than others, there are headwinds, such as inflation and supply chain issues, which may continue to affect the industry overall in the coming year.
The construction industry is expected to continue feeling the effects of increased prices — from the rising prices of steel, lumber and fuel to the increased cost of skilled labor. As a consequence, the industry could experience project completion delays, increased construction costs and reduced profit margins.
1. Market Dynamics
Industry segments experience different growth trajectories & increased competition
2023 could be a different year for the industry, with heightened uncertainty due to high inflation, rising interest rates and bifurcation across various industry segments. Companies are keeping an eye on how their backlogs will play out in 2023, especially during the second half of the year.
While many companies have substantial backlogs, specifically in energy-related construction (e.g., liquefied natural gas [LNG] facilities) and data centers, as they get through the back half of 2023, they may see a potential impact of economic slowdown on their deliveries. Construction activity has broadly started declining due to rising interest rates and deteriorating fundamentals for commercial real estate. An uptick in interest rates raises project costs as input prices increase. Also, an increase in material and compensation costs reduces contractors’ profit margins.
These dynamics will affect some sectors more than others (Figure 1). For example, homebuilders, infrastructure contractors and industrial plant developers will have different growth trajectories. For instance, the Dodge Momentum Index (DMI), a monthly measure of the initial report for nonresidential building projects issued by Dodge Construction, fell 1.2% in August 2022 to 171.9. While the commercial component of the index increased by 1%, the institutional component decreased by 5.6%.
Housing construction in the U.S. slowed down in August primarily due to high interest rates, supply chain constraints and decreased housing affordability. According to the U.S. Census Bureau, building permits fell by 10% to 1.5 million in August 2022 from the previous month. With the Federal Reserve further tightening interest rates to combat inflation, housing construction and permits will likely remain volatile. Additionally, mortgage rates remain high. The average rate on a 30-year fixed-rate mortgage was 6.3% in mid-September 2022, the highest since late 2008. Homebuilders will likely experience sluggish demand as real consumer spending is forecast to fall in 2023 amid an uncertain economic environment.
By contrast, companies building infrastructure projects are likely to remain relatively insulated from the economic slowdown, driven by strong infrastructure buildouts, and the substantial project backlogs developers and contractors have in their pipeline.
In addition, the next round of $1 trillion in IIJA funding enters the market starting October 2022 for several projects. However, labor shortages, wage inflation and ongoing supply chain constraints may slow this growth.
Moreover, developments in the global E&C market, such as how companies deliver projects and what regulations and standards they use (e.g., building information modeling, or BIM, standards), are likely to impact the U.S. market.
Since the International Organization for Standardization (ISO) published its first global BIM standards in 2019, several countries have made the use of certain BIM standards mandatory. As standards, such as ISO 19650 (an international standard for managing information over the whole life cycle of a built asset using BIM), become more consolidated and widely adopted, they are expected to drive growth in the U.S. market when U.S. companies adopt those standards from regions such as Europe, Australia and Canada.
There is also an ongoing shift in mergers and acquisitions (M&A) with increased activity by private equity (PE) investors to buy subcontractors and form synergies and economies of scale. M&A activity by PE investors in construction registered a deal value of $11.8 billion in 55 acquisitions between January and August 2022.
The number of deals increased by around 6% compared to the same period in 2021, while the deal value soared by 297%. The industry could experience mergers and acquisitions of material suppliers and allied service providers to build local capacity and promote supply assurance.
2. Supply Chain
Increased lead times & volatile material costs pressure margins
Over the past two years, the COVID-19 pandemic, transport bottlenecks and geopolitical uncertainties have exposed vulnerabilities in the E&C supply chain. These disruptions have raised material costs, confined production and restricted freight movement. Four in five survey respondents cited supply chain disruptions as one of their company’s top three challenges in the next year.
The industry continues to observe input price fluctuations, and the volatility in material costs is driving up the overall cost of construction (Figure 2). Prices of construction inputs increased 40.5% between February 2020 and August 2022. Persistent inflation could hurt contractors who have not bought large quantities of their materials at normalized prices or included appropriate price escalation clauses in their contracts.
The ongoing disruptions are expected to drive the E&C industry toward new business models, supported by new ecosystems that bring innovative products and services to serve the unique needs of different end markets.
- Technology — For example, a construction technology company has leveraged 3D, virtual modeling and robotics for a new off-site homebuilding approach that addresses labor shortages and controls carbon emissions. To address the supply challenges and rising material costs, developers and contractors will likely leverage advanced technologies to assess strategic inventory strategy for materials and inputs.
- Ecosystem approach — An ecosystem approach can improve E&C companies’ ability to respond to disruptions and enable interoperability throughout the supply chain. Firms investing and participating in ecosystems are more likely to reap higher strategic benefits. By forming an ecosystem with Industry 4.0 providers and material suppliers, E&C companies can use data-sharing platforms to exchange real-time information with material suppliers in case of a disruption or shortage of supply.
- Heightened focus on supply chain management — E&C companies are expected to increasingly stand up supply chain management functions and build more local capacity, driving competition across the industry. Companies will likely expand capacity for the supply of materials in the U.S., get closer to customers to address supply chain constraints and be less dependent on foreign suppliers.
3. Future of Work
Talent pressures and shifting talent models lead the industry to rethink workforce strategies
The E&C industry remains significantly short of skilled workers, further exacerbated by a tight labor market. More than 82% of survey respondents mentioned a tight labor market and an exiting workforce as one of their company’s top challenges in the next year. Even though the construction industry has a strong pipeline of projects and spending, especially the infrastructure buildouts, may be challenged to meet the demand due to a persistent shortage of workers and high turnover.
Labor availability in construction continues to decline (Figure 3), driven by declining interest in the industry, an aging population, and talent pressures in “competing” industries such as technology and trucking. Many workers, especially from the younger generation, are preferring less physically demanding jobs. The number of construction workers between the ages of 25 and 54 decreased by 8% in the past 10 years, while the share of older workers leaving the industry increased.
To retain top talent, companies should consider a workforce strategy based on two pillars: a purpose-driven organization and a personalized career path. Moreover, technology adoption and innovation could help attract employees with new skills and roles such as data scientists and retain workers by encouraging them to work with cutting-edge tools. In addition, an increased focus on diversity, equity and inclusion (DEI) in hiring could yield additional talent for the industry. In 2021, only 11% of all construction workers were women, 6.3% were Black, and 2.1% were Asian. According to a Deloitte study, DEI hiring can help raise productivity, enhance organizational management, improve financial performance and increase innovation.
Addressing the tight labor market and exiting workforce amid shifting talent models will likely remain a priority for most E&C companies in 2023. According to Deloitte’s survey, 91% of respondents agree that offering a flexible and agile workforce structure can help E&C companies to attract and retain talent.
4. Emerging Technologies
Developers and contractors further invest in emerging technologies to drive efficiencies
While the E&C sector has been historically slow in integrating and adopting digital technologies, industry players are now increasingly paying attention to and leveraging emerging technologies. Most E&C companies are utilizing digital technologies to expand business opportunities and boost profits by reducing costs in the long run and enhancing project execution. Further, with increased global supply chain disruptions, increased competition, worker shortages and skyrocketing material prices, the need for digital transformation in construction has become much stronger.
Construction companies are under pressure to safely deliver high-quality projects on time and within budget despite these challenges. While external factors remain outside companies’ control, implementing new technologies can help increase visibility and tackle process inefficiencies. For instance, construction companies will likely adopt digital technologies through two IIJA initiatives: advanced digital construction management systems (ADCMS) and the Technology and Innovation Deployment Program (TIDP) related to the transportation sector managed by the Federal Highway Administration.
These initiatives will provide a total of $550 million to promote the use of digital technologies on government-funded projects. TIDP comprises research and development (R&D) and other efforts related to highways and transportation, while ADCMS is part of the TIDP and was created to advance technologies such as BIM, 2D and 3D modeling, and others. Similar programs will likely be explored across other industrial sectors such as energy and mining and metals. More than half of the Deloitte survey respondents agreed they would likely invest in digital technologies such as artificial intelligence (AI), digital twins and BIM in the next year.
Moreover, developers and contractors are likely to further invest in combined digital and physical technologies such as visual intelligence, sensors and Internet of Things (IoT) devices, robotics, immersive collaboration and drones to increase efficiency. Around 44% of survey respondents have shown interest in investing in advanced technologies.
For example, an industrial technology company recently released an all-in-one cloud-hosted software that enables end-to-end workflow estimation for general and specialty contractors. It provides a structure for consistent and standardized estimating procedures that allows companies to leverage leading practices to boost accuracy and productivity. It also offers collaboration software that connects users with data on any device to enable efficient project collaboration.
Generative design methods produce unique optioneering options (design alternatives) and enable faster collaboration between E&C companies and their customers. These innovative methods help improve project execution, resulting in better managed costs and schedules.
The generative design approach allows companies to leverage modern optimization algorithms and cloud computing power, combined with codified rules, engineering parameters and constraints for early design considerations.
Prefabrication and modular construction will likely continue to be a key new way of working and delivering projects. These modern construction methods enable more standardization across the building process and allow construction firms to actively address the severe productivity problems affecting construction projects’ quality and pace of delivery.
According to Deloitte’s survey, 46% of respondents will likely invest in prefabrication and modular construction capabilities next year. 2023 will likely experience increased adoption rates for the same as more developers and contractors look to capitalize on building in controlled environments to drive operational efficiencies while also solving for changing customer demands and addressing margin erosion.
Leading E&C companies have adopted a structured approach to innovation and exploring emerging technologies. They seek to mitigate the following risks:
- Overlapping funding requests that can lead to confused project approvers and other inefficiencies.
- Creating a burden on talent through siloed R&D, lack of defined impact measures and lack of technology readiness frameworks.
- Prioritizing investments incorrectly due to lack of a disciplined program approach.
Assuming these risks can be minimized, both established providers and startups are expected to continue bringing innovative solutions of different maturity and readiness levels. A focus on practical value and return on investment could further expedite these efforts and potentially achieve significant gains for organizations. In 2023, companies will likely increase the adoption of structured approaches to emerging technologies across the E&C industry.
5. ESG & Sustainability
Industry evaluates new practices to deliver positive societal impacts
Many customers are becoming more sustainability conscious and placing greater pressure on developers to lower the carbon footprint of new construction. The increasing global focus on climate change could incentivize construction companies to factor sustainability into their projects, construction processes and designs (Figure 4).
The 2021 World Green Building Trends report showed that commitments to boost green building efforts remain strong. Thirty-four percent of surveyed companies in the U.S. were focused on green building, and 46% reported that they would do so in the next three years. According to a survey by the Associated General Contractors of America (AGC) in June 2022, 78% of respondents reported having policies to promote recycling, 48% for materials reuse, and 26% for environmentally friendly or sustainable purchasing. However, only 14% currently report greenhouse gas (GHG) emissions on one or more projects.
However, the construction industry is fragmented and project-based, which makes it more challenging to adopt sustainable technologies. One of the biggest challenges construction companies face when implementing sustainable practices is a lack of integrated visibility in their processes and with subcontractors.
As a result, the sector is likely to focus on technology because digitalization plays a key role in enabling energy efficiency and demand flexibility in facilities and buildings. For instance, technologies such as big data and AI/machine learning can help companies track their overall carbon footprint. Smart buildings and infrastructure, which integrate IoT sensors, can increase data availability to track and monitor energy efficiency and enable more efficient operations and maintenance.
ESG will continue to be an increasingly important part of requirements from the operating owners, and it will likely be reflected accordingly in the flow-down requirements.
Additional opportunities in 2023 will likely include considerations for green construction materials (e.g., recycled plastic bricks), renewable energy sources (e.g., hydrogen/solar), and a wide range of supply chain topics, including transparency, traceability, resiliency and circularity.
E&C companies are also factoring in social and governance issues such as ethical organizational practices, community impact and involvement, quality of governing body, and risk and opportunity oversight because these are increasingly important to stakeholders.
To remain competitive, construction companies should prioritize and innovate how they identify, plan and deliver on ESG strategies that comply with regulatory requirements and investor demands, as well as benefit the communities in which they operate. They should remain aware of changing regulatory requirements and reporting procedures.
For instance, in March 2022, the Securities and Exchange Commission (SEC) proposed a new rule that would require public companies to disclose annually certain climate-related financial statement metrics, information related to climate-related risks, and GHG emissions in public disclosure filings. If these rules are finalized and effective during this calendar year, they could begin to be phased in for 2023.
Preparedness Could Be Crucial to Navigate Volatility
2022 got off to a strong start for the E&C industry but was met with several strong headwinds, including rising costs and labor shortages. This created both opportunities and challenges for the industry. E&C companies should prepare for the rapidly changing operating environment characterized by supply chain challenges, high inflation, rising interest rates, increasing material costs and persistent labor shortages. As developers and contractors compete intensely for materials and talent, business continuity, along with buying strategies such as centralized buying/demand planning across projects, should remain a key priority in 2023.
In the coming year, E&C companies will be attuned to the different business environments in each of their customer markets and should therefore focus on the following:
- Having better control over leverage and credit, and creating a buffer through additional cost savings
- Paying attention to changing workforce and workplace expectations and skills levels to more effectively retain talent in a competitive market
- Increasing the use of digital technologies to improve visibility and efficiency, providing resilience amid ongoing disruption
- Capitalizing on additional funds and projects arising from the IIJA and Inflation Reduction Act that could provide additional opportunities in the infrastructure segment
Where companies invest, how they approach project delivery, and how they differentiate themselves in the market is important as the industry becomes more competitive in 2023.
Source: Deloitte