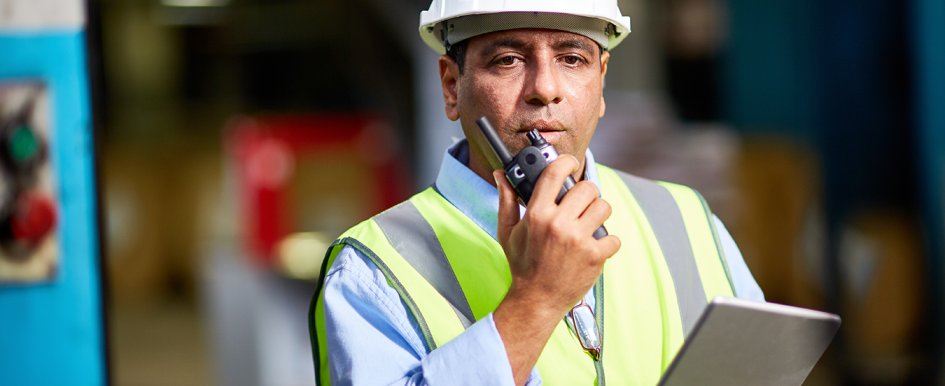
Many construction companies are implementing technology solutions to improve productivity, asset utilization and efficiency on the jobsite. Increasingly, they are also looking to technology to improve the overall safety of workers, equipment operators and project managers while on construction sites and around heavy equipment.
While technology plays an important role in safety, owners and managers can’t simply throw these solutions at problems and expect better results. At the same time, it’s unrealistic for supervisors to police or monitor safety personally since they can’t be in multiple places at once. To create a safer jobsite and build a culture of safety—where safety considerations inform every decision or action—technology must be paired with human insights, ownership from everyone on a site to care about safety and specific actions to bring about effective, lasting change.
The following are four areas where managers must work closely with technology to create a safer jobsite.
1. Safety Analytics
Many companies looking to improve safety implement technology solutions to capture data and observations and track safety incidents to identify trends. But data collection shouldn’t be left to safety managers alone; everyone on a construction site must own and care about safety, meaning they’re also responsible for data collection. Once this data is gathered, safety managers can analyze it to better understand why incidents happened, who was involved and what tasks they were working on when the incident happened. This data analysis can then be used to update safety practices or create personalized training material to target unsafe behavior trends.
Safety managers with an advanced understanding of analytics or sophisticated software programs can also use this data to make predictions. With emerging technologies like artificial intelligence (AI), machine learning (ML) or predictive analytics, data from safety analytics can be used to build models to predict scenarios where incidents may occur based on past events. Armed with this information, safety managers can use insight from the data to prevent accidents before they even happen.
2. Safety Training
Fleet tracking technology or telematics installed in vehicles and equipment allows owners and safety managers to directly track and identify unsafe driver behaviors, like speeding, harsh cornering and more. But simply monitoring for these unsafe events and communicating them to the driver isn’t enough. Fleet or safety managers should use telematics data in an actionable, data-driven way to grade operators based on performance and coach to correct behavior.
Safety training isn’t just a one-time thing, either. Managers must ensure training is an ongoing, consistent process. Pairing technology with hands-on coaching on a regular basis is an effective way to create a safer jobsite. Some companies have implemented gamification or virtual reality programs for this specific purpose as well to coach and train drivers in a fun, engaging way without the risk of harming themselves or their coworkers.
3. Preventative Maintenance
Old, faulty or improperly maintained equipment poses a safety risk to both equipment operators and other workers on a job site. Keeping track of maintenance not only contributes to better equipment utilization and improved productivity on the site but is an important part of building a culture of safety.
Telematics or IoT technology can help managers and foremen keep track of historical maintenance records and stay on top of scheduling both preventative and future repairs, ensuring equipment is in good shape and doesn’t malfunction unexpectedly, causing potential accidents on the jobsite. While maintenance and equipment managers are typically responsible for maintenance programs, safety managers should play a role here, too, incorporating maintenance into overall safety plans.
Vehicle and equipment operators themselves should also be trained on how to manually inspect vehicles and equipment and how to spot signs of wear and tear so problems can be quickly attended to, before they become hazards. This requires hands-on training and coaching from professionals and ownership from the operators in their own safety. Electronic inspection tools can then be used to alert the right teams if an operator marks a piece of equipment not safe to operate.
4. Jobsite Management & Geofencing
Knowing who is on a jobsite and where they are located plays a huge role in safety. To track workers on a site, supervisors may use geofences to create different zones and set up rules to guide the certifications or training required for workers to enter. Some managers or supervisors may create specified safety checklists workers must complete before entering a geofenced zone.
Similarly, geofences can be used to identify areas where vehicles must not enter, or locations where they must be confined due to weight restrictions or hazardous conditions. Supervisors can also set rules for individual geofences based on speed limits or curfew.
As construction companies turn to technology to improve efficiency and productivity, they’re also examining how to create a culture of safety for true change within the organization. By pairing cutting-edge technology with the human touch, managers’ expertise and personal ownership from each worker, companies are taking steps to transform their daily safety habits and create safer jobsites.