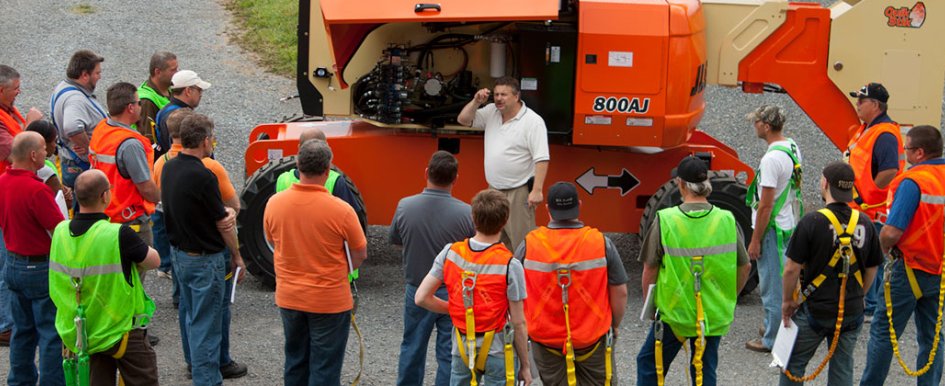
Anyone involved closely with workplace safety has heard presentations, webinars or people just generally talking about the need to develop an organizational “culture of safety” in order to reap long-term, incident-reduction benefits. It’s a term that, despite being around since the Chernobyl disaster in the 1980s, recently has become a bit of a buzzword among safety professionals and modern business leaders.
Unfortunately, so-called improvements at the hands of overzealous safety officers, or those looking to delay a job, have given safety efforts some bad press. However, adopting a safety-focused culture does not have to limit your ability to get work done, nor does it have to lead to a reduction in productivity when implemented correctly.
So, what are the building blocks to creating this type of positive behavior within your teams, and how do you ensure that your efforts focus on worthwhile improvements?
What is a Safety Culture?
First, let’s define the term. In its simplest form, a “safety culture” is the principles or values an organization attaches to the prevention of worker injury, or—to put it another way—it’s the way in which a company views and treats safety.
Adopting a safety culture can be achieved within an organization of any size, but it is not something that can be cultivated overnight. It should be seen as a journey of continued improvement.
Outlined below are six nonnegotiables in the creation of a safety culture in any organization. There are, of course, others that could be included here, but implementing each of the ones below is a major step toward ensuring a sustainable approach within your business.
1. Create Excitement
To garner effective long-term commitment, your organization and teams need to be excited about making an improvement. Maintaining motivation about safety means communicating real benefits that are relevant to your team, as well as explaining the rationale behind the changes.
Encourage support from all levels of the business to help refine your ideas, which helps to ensure that employees will want to support your efforts (if you remain positive and pertinent actions are taken).
Don’t be fooled into thinking that gimmicks are a way to excite people. You will suck all the energy out of a room the minute a safety word-search activity is produced or an outdated safety video is shown. Take time to celebrate the major milestones, and congratulate those who are willing to make significant contributions.
2. Remove Blame
People are generally more likely to engage if they are not on the defense. In order to truly understand not only the lessons from incidents and near-misses, but also the elements that may contribute to incidents over time, an inclusive approach to feedback is required. Ensuring the team can talk openly about problems, potential improvements and additional opportunities assures employees that you support their honesty and integrity in reporting such incidents.
While this certainly doesn’t mean that deliberate acts or misbehaviors should go unaddressed, it is important that everyone feels they can provide feedback without suffering severe, negative repercussions to their decisions or actions. Therefore, creating an environment in which improvements can be suggested without department protectionism is critical to developing a positive safety culture.
3. Empower Workers
Establishing a successful safety culture requires people who support the organization’s vision, so make all employees part of the plan from the start. Take your team members and coworkers with you on the journey, rather than simply pointing to a required destination. Trusting your local team will most likely encourage them to engage with the program and empower them to reinforce any new procedures long after the first safety sign is erected.
Often, when companies attempt to get serious about safety, they immediately put up a new set of signs prohibiting certain behaviors. While well intentioned and likely warranted, this may be seen as enforcing rules from the top down, which can lead to less employee buy-in.
You will gain greater participation by giving supervisors a say in how improvements can be made.
4. Consistently & Continually Improve Your Plan
We can all recall projects or initiatives that started with enthusiasm. These are usually accompanied by big announcements, and then, over time, motivation slowly fades. This happens when people are distracted by other priorities, management support weakens or the project encounters a challenging situation.
Any plans should be realistic and based upon the level of support your organization can sustain. This doesn’t mean significant safety risks don’t need to be dealt with; these, of course, should be addressed right away. But in terms of training, environment and procedural implementation, it is better to introduce a safety program in a way that it can be sustained by the organization. As such, you will want to avoid a “one step forward, two steps back” approach, which results in employee frustration and eventual disengagement. The journey to a true safety culture is a marathon, not a sprint. One important element of consistency is how you apply resources to any plan. While it is not always necessary to have a dedicated safety professional in-house (trainers can be brought in as required, especially for smaller businesses), it is important that anyone assigned responsibilities alongside another function has the bandwidth to handle them all.
5. Make Communication a Top Priority
The purpose of communication should be to pass on information about all elements relating to safety, including positive messages. This goes beyond communicating incident rates and recent occurrences. When workers have experienced favorable improvements in working conditions or are perhaps trying out a new tool or method, share these with the organization to show that safety is not just about rules and procedures.
If you want to change the behavior of your workforce, consider how safety messages are transmitted. For instance, are they just posted on a board, or are they included in a monthly meeting and/or shared using digital media, which is more accessible and iterative? The way in which an organization communicates about safety demonstrate their level of commitment to making changes and improvements. Simply posting safety results without really sharing the implications is not sufficient or effective.
6. Engage Top-Level Support
Are your senior managers committed and engaged? In addition to attending meetings, do they say the right thing during facility tours? Do they do the right thing when no one is watching? Being committed to a culture of safety means wanting to see daily improvements in the way the organization is addressing safety-related matters and being prepared to support the safety team/committee.
Consequently, obtaining support from top management is essential for success. Commitment to a culture of safety requires managers leading by example. This means that if rules are imposed on workers, such as wearing personal protective equipment (PPE) in a particular area, then management leaders need to follow these same rules. It’s not about what they say; leaders’ actions are a far better measure of their commitment to a culture of safety.
If a safety culture is implemented correctly and adopted by team members, not only will safety improve, but also areas such as productivity, employee retention and even product quality will increase. When workers see that the company has taken a genuine interest in their well-being, they feel valued, which, in most instances, leads to better on-the-job performance.
Building a safety culture is all about attitude—your company’s, your co-workers’ and yours. If each of the six imperatives above are addressed and people are committed, then your drive toward the successful implementation of a safety culture will become a reality.