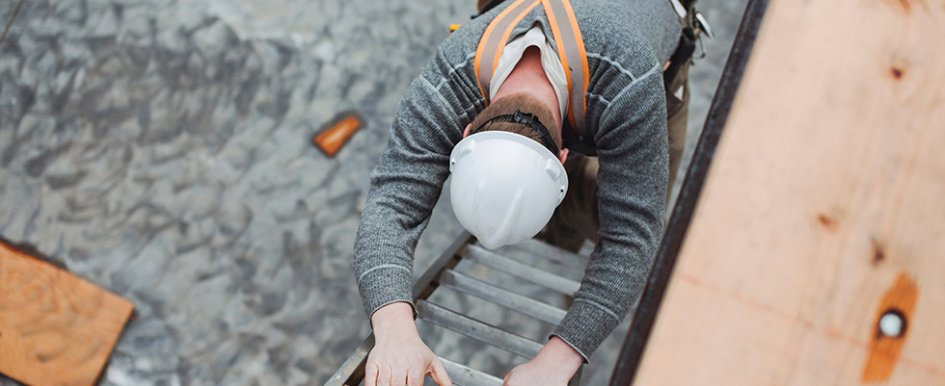
Fall protection is a highly important topic, yet it is often ignored. Falling from elevated work locations has been a leading cause of injuries and deaths in the construction industry. Falls can hurt an employee both physically and emotionally.
During construction, developing and implementing safety programs can help prevent accidents. But what happens afterward?
After construction is complete, a building will require routine or nonroutine maintenance. This maintenance may include, but is not limited to, unclogging drains, cleaning windows and skylights, repairing and inspecting equipment installed at rooftops, etc.
As an employer, ask yourself this question: Have we provided a safe workplace for the workers performing these construction and maintenance activities? The Occupational Safety and Health Administration (OSHA) sets standards and regulations to protect workers. However, due to lack of knowledge about these requirements, people don’t always follow them. This puts both the employee and the employer at risk. You can avoid this risk by proactively putting enough fall protection in place.
The U.S. Bureau of Labor Statistics reported that during the period of 2014 to 2021, falls to lower levels accounted for 13% of all the fatalities in all industries. To improve the fall protection in workplaces, the U.S. Department of Labor announced a new national emphasis program. This will allow OSHA to initiate inspections whenever they observe someone working at heights.
According to OSHA, this will hold the employers accountable to provide safe working conditions for their employees. The program targets both construction and maintenance activities. To improve overall on-site safety, we all need to be more conscientious about the seriousness of fall hazards. We can all save lives. Below are answers to some common questions about fall hazards and ways to protect against them.
How does OSHA define a fall hazard?
According to OSHA, a fall hazard is a work location elevated at 4 feet in general industry workplaces, 5 feet in shipyards, 6 feet in the construction industry and 8 feet in longshoring operations.
Note that some states have OSHA-approved state plans that may dictate different fall-hazard elevations. For example, in California, fall hazards start at 30 inches in general industry workplaces. Please review the state requirements along with federal requirements.
Additionally, OSHA also requires fall protection when working over dangerous equipment and machinery, regardless of the fall distance.
What are the best ways to protect workers from falls?
Fall protection can be achieved by using one of the following methods:
- Active fall protection — This is a fall-protection system that workers need to actively engage with, such as safety tieback anchors, lifelines, safety tracks, etc. This is recommended when the work is not routine, since it involves competence of the worker, training and active certification of the system installed. One can also categorize these systems as “fall-arrest systems” (systems used to arrest a fall in case the fall occurs) or “fall-restraint systems” (systems that do not allow workers to fall and restrains them from falling).
- Passive fall protection — This is a fall-protection system that workers don’t need to actively engage with, such as parapets and guardrails. The preference is to use these in routine maintenance work locations. This eliminates the user errors or malfunctioning of a fall-protection system.
When is permanent fall protection the best option?
The ideal time to consider a permanent fall-protection system is during the design phase of the project. That way, you can budget and implement fall protection during construction. Not considering fall protection is a common mistake that owners/developers make early during projects. Fall-protection systems don’t just save lives — they save money as well.
We have approved permits from the city department. If they did not require fall-protection systems in our plans, why do we need to design and install them?
You may have received permits from city, state or government personnel who may not have full knowledge of OSHA’s requirements. But OSHA doesn’t hold other government personnel responsible for knowing OSHA requirements — they hold you responsible.
Designing and installing these systems upfront does cost money, but not installing fall protection is risky, and there can be an unfortunate accident if fall protection is not in place.
When that accident occurs, OSHA investigates it. That investigation goes back to the start of construction to determine liabilities. It’s better to be proactive and stay compliant rather than pay hefty fines or experience the injury or death of someone while working at the building you built. Per the National Council on Compensation Insurance’s (NCCI) data, the average workers’ compensation claim for falls/slips is more than $48,000.
City departments don’t often call out missing fall-protection systems since they fall under OSHA’s jurisdiction, but that doesn’t mean the projects don’t require fall protection. If you are a general contractor, your proactive approach to fall protection can save you and your clients from future liabilities.
The architect doesn’t know the requirements. What are my options?
You can hire a safety consultant who will work alongside the project architect and provide design drawings for fall-protection systems. Doing this upfront may save you a lot of money and last-minute coordination that can push the project schedule back, cause headaches and cost a lot more money.
In addition to fall protection, what other safeguards can be built during construction that improve overall safety and add to the overall value of the building?
In addition to fall protection, you should consider access to all elevated work locations. While employees can use portable ladders to access those work locations, OSHA recommends providing fixed access ladders or roof hatches to eliminate user errors while setting up portable ladders. Some states that use the state’s OSHA-approved requirements demand fixed ladders or roof hatches to provide access to elevated work locations. They will even have different criteria for each condition. In addition to access to work locations, you should also consider an exterior building maintenance system (EBM), or the “window cleaning system.” Using ground-based equipment such as ladders, water-fed poles or aerial lifts to clean the windows are only safe to certain heights with certain safety precautions taken: Are there any high-voltage lines nearby? Is the ground stable enough to handle the loads required? Is the ground slope too great for certain ground-based equipment? Are there obstructions around that could impact the work area?
General contractors can play an important role in saving construction costs by considering and building these systems during construction and adding to the overall value of the building.
Let us collectively thrive for safer workplaces and remain mindful of hazardous working conditions.