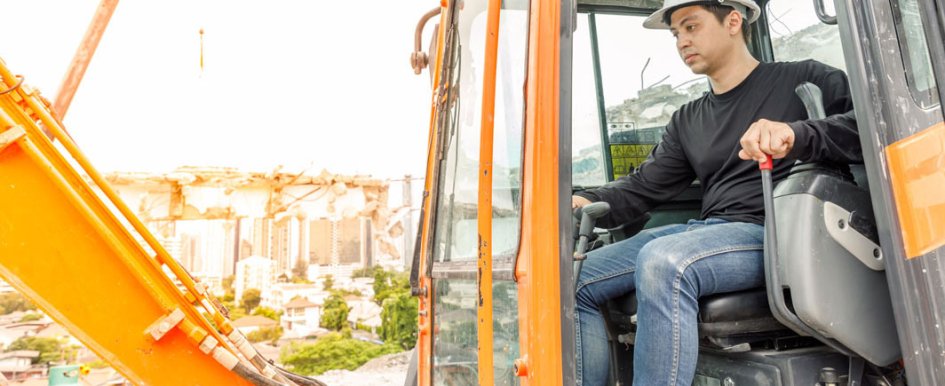
Advancements in technology and the ongoing evolution of equipment are among the most widely discussed trends in the construction industry today. Topics like telematics, hybrid-powered equipment, electric power and autonomous operation usually get all of the attention and glory, but the safe operation of machinery has been, and continues to be, the top priority for equipment manufacturers.
Equipment industry standards and regulations committees regularly focus on the topic of safety devices. Back-up alarms, perimeter lighting and rearview cameras are already being used by many manufacturers, and devices like proximity detection sensors and collision awareness systems are quickly gaining widespread acceptance.
As the technology advances and becomes more reliable, original equipment manufacturers (OEMs) have a long history of adding the proven systems to their equipment. Seatbelts, rollover protective structures (ROPS) and safety glass have been extremely successful in protecting workers over the years.
Now, most manufacturers include safety systems on the majority of machines. (This is not necessarily due to any regulatory mandate, but simply because it’s the right thing to do.) While many of these technological advancements have made significant improvements to jobsite safety, and have built greater awareness for worker safety in general, a number of other factors could potentially undermine their effectiveness.
Decreased Attention Span
When it comes to humans interacting with technology, generally, current studies aren’t focusing on the benefits of the technology itself, but rather on how it’s affecting people. Many experts in the field theorize that the onslaught of new technology (mainly focused on mobile devices) is eroding attention spans.
Studies like these argue that humans scan information so quickly that they no longer take the time to read slowly enough for comprehension, and their interaction with technology is becoming more impulsive and impatient over time. If these theories are valid, what ramifications could they have for the construction industry, where awareness is critical for safety? Will the safety devices mentioned previously be as effective if a worker’s attention span is not as long as it should be?
Complacency
All of this begs an unsettling question: When it comes to equipment safety specifically, how much technology can be added before the equipment operator becomes overwhelmed? Equipment operators are human. They deal with physical and mental stress, fatigue, and the pressure to meet deadlines. Even the best technology available will not eliminate these issues.
If equipment operators become accustomed to the repetitive warning sights and sounds, day in and day out, they are at risk of becoming complacent—trusting in the technology’s intended purpose and simply ignoring the warnings when desired. Even though operators should rely on their training, hand signals and the equipment’s safety systems in their work, is it possible they still suffer from sensory overload and distraction?
Limited Effectiveness
Yet another factor to take into consideration is that equipment safety devices are not one size fits all. While a certain technology might work well in one environment, it may not perform as effectively within another piece of technology. Whether it’s construction, demolition, mining or forestry work, dirty, dusty and wet environments can affect the performance of most safety features. Back-up cameras, proximity alarms and sensors can have their effectiveness limited in certain worksite conditions.
In such situations, will workers become so reliant on technology that they begin to take it for granted, placing themselves in danger by failing to consider the technology’s limitations on the jobsite? There’s also the concern of equipment operation itself and how it can hinder the effectiveness of safety devices, such as back-up cameras. For example, high-vibration exposure might render the technology useless if it’s not robust enough to withstand the rigorous movement of a heavy-duty machine.
In addition, remote camera mounting locations may be required to avoid the impact caused by normal operational requirements or the size of the equipment. The more remote, the more impact on performance and the more difficult to access for cleaning (e.g. the height of camera placement due to machine design can affect image quality).
Artificial Intelligence
When implementing technology that uses artificial intelligence (AI) for autonomous operation, a number of other challenges arise. For example, automatic emergency braking as part of a collision-avoidance system may be straightforward to the automotive industry, but it’s a tremendous challenge for the heavy-equipment industry.
Other, more complex factors must be considered when applying artificial intelligence to big equipment, and construction sites have more variables to consider than mining sites. Ground conditions, nominal payload, payload distribution, increased variation in operational skill levels—all create numerous challenges for applying safety technology that calculates the different types of hazards.
The open nature of many jobsites does not allow for some of the simplest inputs available in automotive applications, such as clearly defined, paved lanes; intersections; and signs. False positive detections can easily be introduced on the jobsite, which can create hazards due to braking on curved paths or locations with poor underfoot conditions (especially at high travel speeds).
Furthermore, the travel speeds and mass amounts of construction equipment on-site make the dynamics of braking far more complex. Many of the different machine forms and intended tasks on construction sites demand a wide variety of safety features for the unique safety challenges of each machine.
For example, excavators have entirely different risks and avoidances than wheel loaders or haul trucks. Space constraints, especially on smaller machines, can be an issue in applying new technologies. The equipment operator is often in the best position to make the appropriate braking decision for the site-specific conditions. Taking control away from the operator with an automated safety system may not always result in the best outcome.
When it comes to automotive applications, as conditions become more challenging, systems are automatically disabled, thereby placing control back into the operator’s hands. For instance, in some vehicle models, the adaptive cruise control and auto-braking system are disabled during poor visibility.
Also note that the use of automated systems can result in reliance on the system by the equipment’s operator, which could become an issue when they move to a machine without those features. Field conversion of older machines to those types of automated systems could be difficult and cost-prohibitive.
When applying automated safety technology, it’s a challenging task to determine when to take control away from the operator. Ultimately, the operator of a machine should remain in control when possible, and they are responsible for its safe operation.
The Bottom Line
Business owners must understand that technology, while advancing the cause of safety on the jobsite, is not perfect. Technology has limitations, not only within the environment in which it’s expected to function, but also in the way it’s used by the operator.
Regardless of the technology being used, the key to ensuring safe operation of heavy equipment is to ensure the operator’s commitment to safety. Not only do they need training, but they also need to consistently participate in safety programs, engage in toolbox talks and help to cultivate a culture of safety awareness.
There’s no overstating the value of technology’s ability to reduce safety risks. However, it remains critically important to recognize that an equipment operator’s safety awareness provides the greatest possible protection. That awareness, though, can only be achieved as a result of a full commitment on the part of an organization to implement and adhere to a robust safety program—one which extends all the way from the boardroom to the trenches.