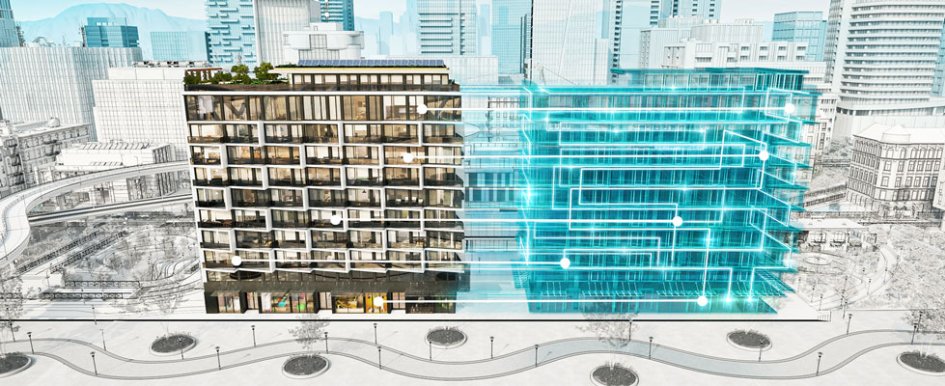
The age of the digital twin (a digital representation of a system, object, or in this case, a project) is here — and the technology is no longer just a solution for the world of manufacturing. More and more areas of the construction industry are increasingly connected through the use of the Internet of Things (IoT), data analytics and artificial intelligence.
A digital replica of the physical version of a construction project gives technologists, project managers, executive teams and other key stakeholders the ability to work more efficiently, safely and profitably. But does your team understand the full capacity of a digital twin’s usefulness in a construction project? We’re here to help.
As senior director and general manager of Autodesk Tandem, Bob Bray is leading Autodesk’s initiative to transform the built asset life cycle with digital twin technology and solutions. Bray and the team at Autodesk have been working with several leading construction organizations to test the company’s Autodesk Tandem, a digital twin platform, on real and ongoing projects. Below, learn about the use of digital twins in construction, the challenges that still exist with implementation, and more.
CBO: How do digital twins work?
BB: A digital twin is a digital replica of a built asset. To be truly effective, they need to possess operational and behavioral awareness of their physical counterpart to simulate, predict and inform decisions based on real-world conditions.
Digital twins federate all the data created over the course of a construction project into a comprehensive digital replica. The idea is that by capturing data throughout a project’s life cycle — from design to engineering to construction — a digital replica can be handed over to an owner and connected to their operational systems to begin delivering rich insight. This helps them get the most out of their investment and makes for better business and operational decisions.
For a building owner or operator, the benefits of a digital twin can be significant. They can range from simple examples, such as having a problematic floor tile or other material and being able to quickly identify where that tile is used, to being able to predict maintenance issues with heating, ventilation and air conditioning equipment before the fault occurs.
Last year, we joined the Digital Twin Consortium, an organization advancing digital twin technology across industries. We joined to express our commitment to working with our customers on digital twin best practices and standards requirements. What makes digital twins so exciting is their ability to connect the physical and digital worlds, and provide real-time operational awareness of structures, machines and even products.
CBO: What technology is currently being designed OR built to enable the widespread use of digital twins?
BB: Autodesk Tandem is a digital twin platform that allows a building project to start digital and stay digital, from design to build to operations. It transforms rich data into business intelligence.
Autodesk Tandem uses building information modeling (BIM) data created throughout the project life cycle. BIM data is an essential foundation to creating a true digital twin of the asset.
Today, digital transformation has gone from a nice-to-have to a must-have across every phase of design, construction and operations. The near-term focus of Autodesk Tandem is on enabling a data-rich digital handover to owner/operators that can be used to accelerate operational readiness of a new facility. Beyond handover, Autodesk Tandem becomes a digital replica of the as-built facility that will connect to operational systems to provide greater insight for owner/operators, and ideally a better occupant experience.
Autodesk Tandem and digital twins are part of an industry move toward digital transformation, where every system becomes more and more connected as data is generated and systems learn from one another, share insights and optimize performance in real-time.
CBO: Do you have an example of a firm that is testing this technology?
BB: Yes, we’re collaborating closely with Chief Technologist Brian Melton of Black & Veatch. They see Autodesk Tandem interfacing with data systems like computerized maintenance and management systems (CMMS) and supervisory control and data acquisition (SCADA) systems. This provides owners and operators with access to all the information so they can start asking:
- Where are all the assets that currently have open maintenance work orders?
- What are the chances of this asset failing in the next 5 years?
Another one of our customers, Marin Pastar, global technology leader of vertical information modeling at Jacobs sees the value of digital twins in reducing total cost of ownership, which drops drastically from design to construction to completion.
As approximately 80% of a facility’s total life-cycle cost is realized during operations, considering what an owner will need at handover from the beginning helps ensure proper management of assets based on business goals and processes.
CBO: What challenges currently exist with the implementation of digital twins in construction?
BB: One of the greatest challenges is capturing all of the information across multiple teams on the construction site. There are many disconnects as data flows and you go through the architecture, engineering and construction process.
If we want to make digital twins a reality for the built environment, we need to be able to connect processes and capture data through the life cycle of the design process and take advantage of the data intelligence to connect the ecosystem over time.
Another challenge is breaking away from the status quo. People are used to working how they’ve always worked and are resistant to change. There is a huge opportunity and responsibility for architects, engineers and contractors to embrace digital twin up front so they can ultimately provide more operational value to their customers and help them maximize their long-term investments.
CBO: Does the use of a digital twins depend on the team already having a comprehensive understanding of the firm’s data, or should the twin be a tool to encourage understanding?
BB: Digital twins can work both ways, but they are ideally used from the onset of a project. It tends to be an expensive, bespoke process to retrofit a digital twin for an existing facility, but it can be done.
We’re working to help the industry long-term to create a scalable, repeatable process for creating a digital twin through the design build process that the owner can use post-handover. In either scenario, it’s a matter of understanding the outcomes an owner/operator wants to achieve and capturing the right data to enable those outcomes.
CBO: How can a digital twin help other project stakeholders after the project is complete?
BB: Digital twin helps all teams along the project delivery life cycle to understand the data deliverables they are responsible for, leading them to become better managers of data. After a project is completed, the team can deliver a comprehensive digital handover to owners. The data they receive is insightful and can accelerate operational readiness and help them make better business decisions.
CBO: How would a project team or construction firm deliver a digital twin to an owner?
BB: We see offering a ready-to-go digital twin to owner/operators at handover as a significant competitive advantage for our AEC customers. It starts in consultation with the owner about their information requirements, specifying those in the digital twin,
and then capturing that information through the design and construction process. The information can be verified at each handover point, and at project turnover, the as-built digital replica can be delivered to the client.
CBO: Can you discuss some examples of successful use cases or projects in planning where digital twins are being used in other industries?
BB: The commercial aviation industry and automation industry both uses digital twins. Digital twins can work for any type of asset large or small. It’s a very similar process — whether it’s an aircraft engine, a wastewater treatment plant or highway system. The core value of synthesizing data for better decision-making and fine-tuning operational performance remains the same.