If the recession taught the construction industry anything, it was the importance of being razor sharp in terms of productivity. Best-in-class contractors understand that arbitrarily slicing margins and costs without a true productivity improvement plan is short-sighted and ill-advised. All this plan achieves is adding low-margin backlog with increased risk. As the economy continues to improve and firm backlogs grow steadily healthier, the same tenets that served contractors well in the rough times can help them maintain competitiveness and improve the bottom line long term. Often referred to as the blocking and tackling principles in the operations world, productivity best practices are the fundamental building blocks of your business. Ultimately, the only true productivity improvement comes from a commitment to organizational and individual behavior change.
These primary building blocks of productivity improvement revolve around three areas—proper planning, collaborative communication and a steadfast ability to maintain accountability across the various stakeholders. Managers and superintendents often view planning as a distraction to true work and fail to dedicate the appropriate level of resources. When it comes down to why they don’t plan, the excuses may vary—not enough time, things change too much to plan or the job is too small or too big. Collaborative communication requires that the project team generates meaningful solutions and truly brainstorms everything from the project in totality to the daily planning. Lastly, there must be a mechanism to ensure adherence. Otherwise, the tools and processes will simply be viewed as recommendations, rather than mandatory management best practices.
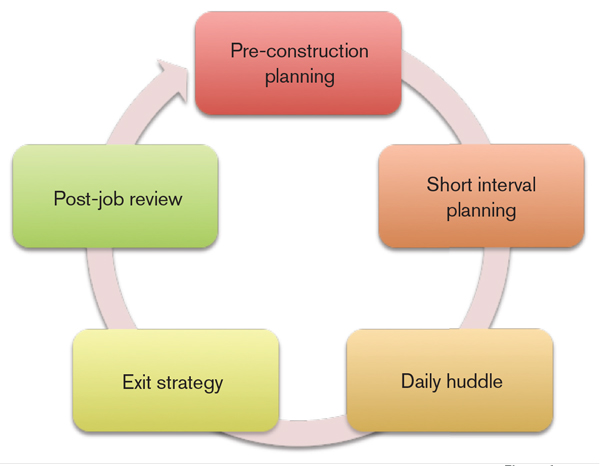
While there are many elements that encompass true project management and supervision, the foundation on which all productivity improvement efforts should focus is illustrated in Figure 1. The following definitions should be applied for a true understanding of the elements within this foundation.
- Pre-construction planning—This is a collaborative, structured set of planning meetings that includes the estimating and project management team and the field leadership. Enough time is allowed for the individuals to do the requisite amount of preparation for the meetings. At the conclusion, the project team has a solid strategy and everyone understands his or her role in that plan.
- Short interval planning—Not to be confused with scheduling, planning requires the field manager to storyboard the work over a one or two-week stretch and assign appropriate labor or trade partner resources. Key impediments can be identified. If the work is too dynamic to game plan, contingency plans can be drafted. The planning tool must be consistent across all field managers in order to eliminate variability.
- Daily huddle—This quick meeting in the field establishes the goal of the day. Using the aforementioned short interval plan and project budget, the field manager sets the target goal for the day (lengths of pipe, bays of steel, painted rooms, sheets of drywall or squares of roofing insulation). Additionally, the field manager can cover real-time safety issues in conjunction with safety protocol. Lastly, material and equipment needs in the short-term are percolated to avoid work stoppages.
- Exit strategy—Similar to preconstruction planning, the exit strategy can be considered the brainstorming associated with the last 10 percent of the project. Normally a pain point for contractors, the exit strategy provides a structured approach to finishing strong. Punch lists are done, closeout documents collected and ultimately the customers are satisfied that the project finished and did not linger.
- Post-job review—This process allows for a thorough analysis of all projects, not only the ones that fail to meet internal or external expectations. The process should be designed to gather customer intelligence, construction nuances and intricacies not shown on plans. This is an excellent vehicle to share the final score of the project with the team.
As depicted by the loop in Figure 1, each of these five productivity elements feed into each other and ultimately become a part of the next project.
Think of the process as the road map. For each of the elements above, there should be a beginning and ending point. Each step in the process should have someone within the firm that is ultimately responsible for its completion. By having a process, the firm not only has a tool that can be trained throughout, but also a way to enforce accountability.
Rather than live with a litany of disparate spreadsheets, documents and agendas, the firm should create one body of consistent tools. Reinventing the wheel on every project becomes time-consuming to develop and complicated to translate to every individual within the firm. What if Wal-Mart, Apple or McDonald’s not only operated individually across their franchises, stores and factories, but also allowed individuality to exist with every associate within those singular locations?
A productivity best practice must be universal. Often, firms confuse one individual’s great results with the existence of best practices. The end game of productivity improvement should be the implementation of one standardized approach that the firm employs. These processes will require enhancements and modifications. A firm must regularly evaluate the efficacy of its processes to ensure they are driving better productivity. Achieving operational excellence is the pinnacle every contractor should strive to achieve.