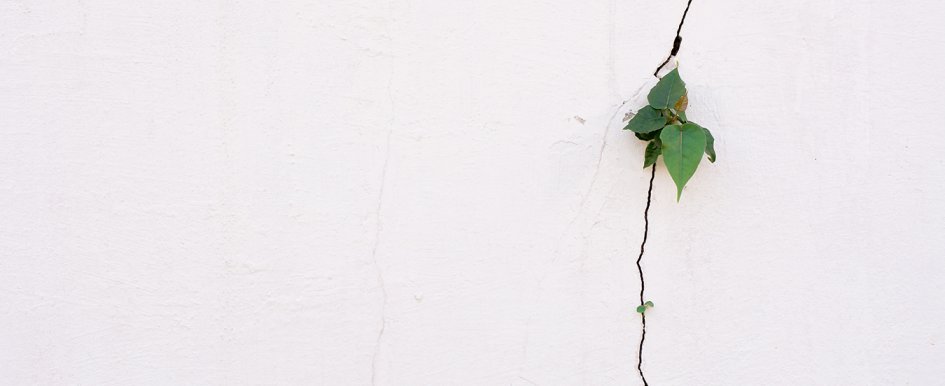
“Adapt or Die,” is arguably the most memorable line from the movie version of "Moneyball." The meaning of the quote and how it relates to business and risk management is paramount—we must fight and overcome the current status quo if we want to change the industry. In construction, we continue to encounter challenges, such as shortages of a skilled workforce, fast-paced technology changes, economic impacts, trade partner liabilities, succession issues, and the ability to attract and retain top talent. Strong enterprise risk management (ERM) programs can help us manage these risk factors.
It is no secret that construction risks are far too complex for traditional risk management methods to be effective. We all understand that risk is the cost of doing business for us, and we have embraced risk as our ally. In doing so, we have developed strategies that enable us to exploit risk to improve our company position, and we have methods in place to manage those risks that could have a negative impact on our company position. Our ability to continue to do these things collaboratively will give us a competitive advantage.
That is why the ERM strategy is rather simple; do not approach risk management as insurance, claims management and loss control. While each of those components is part of our ERM model and the overall bigger picture, for us, good risk management is much more. We have learned risk that affects one department often bleeds over to another and, in turn, impacts the company's strategic goals. For this reason, Hoar has spent a great deal of time developing the framework for an ERM program, which aligns with our culture, our vision and our core values.
Why ERM? Because ERM is a holistic approach that allows us to focus on all our risks—such as legal, insurance, finance, safety, quality and claims. A focus on each of these components allows for the breakdown of the barriers that exist when each operates independently. Viewed holistically, these components tie together to support Hoar's lifeline—operations. Each of our risk areas brings a key stakeholder to the table to collaborate on a consistent basis to ensure various business risks are identified and assessed, and that proper strategies are put in place to mitigate the exposures.
One key factor in our smart risk strategy is the utilization of analytics and data to drive Hoar's mission. While we have historically relied on data as a driver, we have broadened the categories of data collected over several years to allow us to focus on key risk points. For instance, in the past, we focused on severe or frequent injury and incident data, which helped us improve our Occupational Safety and Health Administration (OSHA) recordable statistics. We were able to improve those statistics from a double-digit statistic to a single-digit statistic in under 5 years.
In that process, we learned that simply focusing on that “lagging” data would not get us to the goal of zero injuries. We needed to get in front of the existing conditions and behaviors that resulted in those injuries to eliminate the hazards for both Hoar and its trade partners.
One good example of cross-departmental collaboration is our monthly risk and safety incident review meeting. At the beginning of each month, our risk and safety stakeholders dedicate time to review and discuss every injury and incident that occurred the prior month on our projects. On average, we review 24 incidents each month, and then conduct a deep dive into the circumstances of each one to determine how we can position ourselves to prevent reoccurrence.
Dedicated time to analyze incidents helps us determine if any have the potential to become a serious injury or fatality (SIF), and if they do, a broader review is conducted to learn more about the existing conditions leading up to the incident. This puts us and our trade partners in a position to prevent those same conditions on current and future projects. We then ask our project team to lead us in a learning session, so we can share the results of what we learn to improve the industry overall. This has allowed us to develop key safety programs to focus on the top 10 risk categories.
In conclusion, just as the professional baseball industry experienced a change in mindset through the use of a cache of numbers—numbers that were collected over several years by individuals, such as software engineers, analysts, lawyers, statisticians and physics professors—we have implemented an ERM program focused on numbers in order to gain a competitive advantage in an industry where the health and safety of our employees and those that work on our projects is most important.
You can’t just flip a switch and have a complete ERM program. It is a continuous improvement process that takes time to fine-tune. We must tailor the program to match our culture and risk profile. If something does not work, we refine it. If something does not fit, we replace that component. As we grow, it grows. There is no such thing as a one-size-fits-all ERM program. We must continue to adapt.