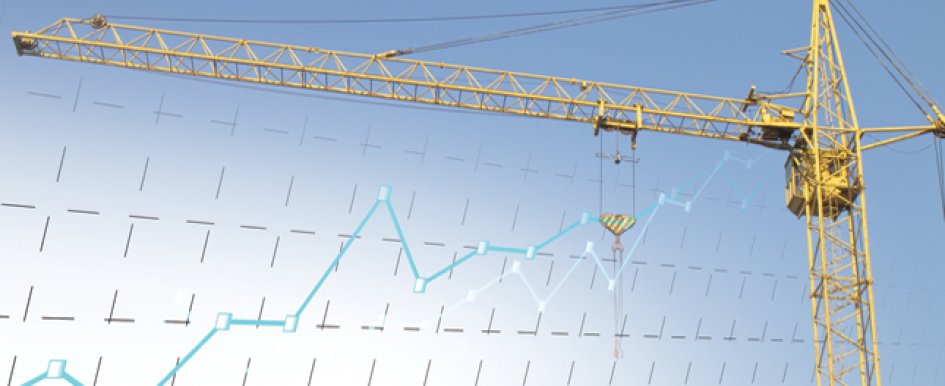
Project controls, including standardized approaches, processes and reporting, are designed to manage all costs and financial aspects of a project through its life cycle—from initial estimating and budgeting to forecasting, measuring progress, controlling change, reconciling actual expenditures and closing out the project. They should also provide better visibility into how a project is performing and allow teams to make proactive decisions to improve performance during the project’s execution.
Project controls are often overlooked or not developed fully enough to be effective with smaller contractors. Some use software tools for managing and reporting expenditures and budget variances, but many still rely on manual processes and the accounting department or project managers to monitor a project’s performance. Even at global engineering and construction firms with dedicated project controls departments, the tendency is still to use spreadsheets for managing cost performance reports.
Small to midsize contractors need to operate with lower administrative overhead costs than their larger counterparts. Nevertheless, fundamental project controls can be implemented and standardized.
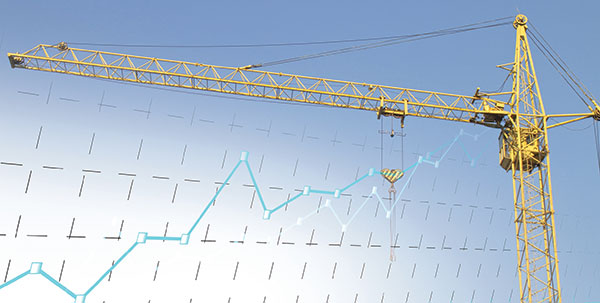
Earned Value Management
One component of project controls systems that is becoming more popular in the construction industry is earned value management. The key performance indicators employed here measure project performance by comparing work completed (earned value) against work planned as of a given date. Measured either by cost or schedule, these indicators can then be used to forecast an estimate at the completion of the project, based on actual performance.
Earned value management provides a more realistic look into where a project is heading, versus looking at the percent of budget spent, and helps to identify areas of underperformance. This can be the difference between finishing a project successfully or incurring considerable penalties.
Lack of Transparency
Data silos and a lack of transparency exist in the construction industry both internally and among external parties such as clients, partners and stakeholders. The main issue is that many construction firms still rely on manual methodologies to integrate schedule and cost data.
With much of the reporting compiled by hand, management teams simply cannot obtain reports fast enough to ensure timely and accurate insight into project performance. With silos of data and little transparency between teams and departments, managers find it difficult to forecast project performance accurately, and stakeholders struggle to gain a holistic picture of a project’s progress or to assess and mitigate risk—all scenarios that threaten margins and profitability.
A recent review of 975 owner-submitted projects by the Construction Industry Institute revealed that less than 6 percent delivered planned financial returns, and almost 70 percent failed to deliver within 10 percent of the planned returns. Although some projects seemed doomed to fail as a result of false optimism, poor market research or poor project estimates, others failed because they were not well managed or controlled.
Building on Business-Driven Technology
While Excel spreadsheets can be a logical first step for smaller contractors, these documents do have limitations. They can be time consuming and prone to human error, especially as projects become more complex. Meanwhile, enterprise resource planning systems are designed to manage business functions rather than projects, and they lack controls such as contingency, change control, multi-currency and forecasting.
A project controls solution is a business-driven technology bridging the gap between spreadsheets, enterprise resource planning and costs and scheduling tools. It provides a centralized repository for all project costs and standardized cost controls structures with project-specific flexibility, resulting in automated reporting that is faster and more accurate. Firms can use these tools for project portfolio management, project budgeting and forecasting, scheduling, contract cost management and performance measurement (through earned value analysis).
Reducing the time and effort of reporting on project data enables construction executives to focus on strategic processes delivering project efficiency, such as analyzing budgets and actuals, change management and forecasting and trending. And if that trend is anything other than desirable, the data will serve as a predictive red flag, helping to proactively plot a new course forward.