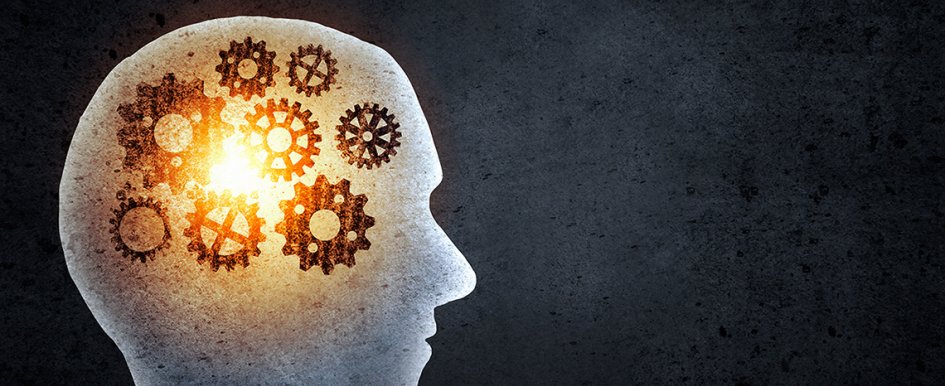
The construction industry continues to evolve at a glacial pace from a management and productivity standpoint, while other industries have transformed themselves and their productivity performance. Efforts to improve productivity in construction have been widely unsuccessful. Lean construction or lean project delivery is no exception. However, construction companies need to take a fresh look at the concept of lean with a new perspective. There is a way for leaders of construction companies to apply lean thinking to their organization and achieve breakthrough productivity.
Most attempts at applying lean management to construction have failed miserably because they lacked a clear understanding of the problem. Applying lean principles to construction can be done successfully if you apply them to the enterprise as a whole and utilize technology to systematize and automate processes. This aligns the organization and yields real-time insights that were not possible before, boosting productivity dramatically.
Lean is about breaking down organizational silos and rethinking how your business processes work to eliminate inefficiencies and become a “boundaryless organization”. But, before getting into exactly what is the boundaryless construction enterprise and how technology can facilitate the transformation, let’s look at the history and present state of the construction industry to understand the current situation.
Construction Remains Stuck in the Siloed Organization Past
McKinsey & Company has previously reported extensively on the construction industry’s lackluster productivity. The graph below illustrates that while productivity has nearly doubled for manufacturing over the last 20 years, it has remained stagnate and even declined for construction.
But if we take a closer look at the 1990s, we need to ask what advances were taking place in manufacturing that allowed it to improve that were not taking place in construction? The answer: the emergence of enterprise resource planning (ERP (from MRPII)) and the introduction of lean management theory in the west, both of which were never fully incorporated into the typical construction enterprise.
Lean thinking has its origins in the Japanese automobile industry, dating back to the 1950s and the Toyota Production System (TPS). Outside of Japan, lean manufacturing gained popularity in the 1990s after the publication of Womak & Jones’ The Machine that Changed the World.
Similarly, working across organizational boundaries was a new way of thinking in the 1990s—one that was largely championed by Jack Welch, then CEO of GE. He advocated for a “boundaryless organization,” which would bring people together across levels, functions and geographies to solve problems and make decisions in real time.
Today, 30 years after lean thinking and ERP revolutionized the manufacturing industry, construction remains plagued by operational inefficiencies. The root of many of these inefficiencies lies in the siloed architecture of construction organizations. These organizational silos lead to system silos, which lead to data and information silos. This silo modus operandi results in inflated cost structures, extended project schedules and a general inability to detect and react effectively to disruptions.
The absence of holistic business applications for construction has played a key part in the continuance of this structure. Even though construction enterprises have been investing in ERP for decades, mainstream ERP for a typical construction organization is effectively little more than a financial, back-end application.
For mass manufacturing companies, the core part of their business is inside the ERP, making it easy to gain process efficiencies. Construction companies’ core business is projects. The traditional ERP does not support projects effectively, and therefore, construction companies deploy a multitude of standalone point solutions to manage critical parts of their business. This means many companies are using spreadsheets and various ungovernable desktop and project tools outside of their ERP to run their billion-dollar businesses.
Transforming into a Lean Construction Enterprise
Clearly, as lean principles are introduced to new industries a certain level of refinement is required. Operationally as well as financially, construction companies are faced with significantly higher levels of uncertainty and risk compared to manufacturers due to the inherent volatility of construction projects. This issue does not negate the value of lean thinking, but requires additional emphasis on managing uncertainties, synchronizing and ensuring visibility into the various and constantly moving parts that go into the execution of a project.
Traditionally, the construction industry’s efforts to pursue process improvements have been confined to the project management silo. For example, the progress attained with the Last Planner System has been significant in discrete places. However, it is mostly confined to the short-term planning process, and intended to facilitate communications between project managers, site managers and trades foremen, limiting the value brought to the enterprise as a whole.
The next great leap for construction lies in pursuing a holistic approach where solutions, tools and business processes make no distinction between functional silos and organizational divisions.
Unifying Project Business Processes
To successfully adopt lean principles, companies need to align business processes across the entire enterprise, ensure corporate practices and standards are followed while maintaining the agility required to react fast and effectively to variations and disruptions.
Fundamentally, this transformation requires rethinking how your business processes work. The normally disparate financial and operational project management processes must merge in a seamless manner, breaking down those organizational silos.
Technology as the Enabler
To be effective and enduring, we believe this process unification must be enabled and enforced through technology. Codified in this way it creates the infrastructure that keeps the company moving in this new direction.
Practically speaking, what we are seeking is the consolidation of project financials, project operations and ERP into one system, which we call the Unified Project Solution Paradigm. Consolidating the application landscape of these processes reduces complexity and facilitates the transition to lean thinking across the enterprise.
Specifically, technology enables four critical components of successful transformations in construction companies:
1. Align the enterprise—The delivery of a construction project involves many moving parts, including internal resources, subassemblies, materials, equipment, subcontractors and vendors, plus financial constraints which are required to meet profitability and cash-flow targets. Managing these components over the long duration of an engagement subject to frequent changes and adjustments is challenging at best and near impossible in a siloed architecture dependent on manual intervention. The introduction of a single integrated business application automatically aligns business activities in real time. Financial implications of operational changes are instantly captured and reported. The ability to align the enterprise means fewer surprises, lower mitigation costs and fewer operational delays.
2. Automate processes—By operating within a single integrated business application framework, construction organizations can implement end-to-end, automated processes that span across departments and functional silos. These automated connections facilitate enterprise alignment and process synergies, enabling companies to operate and react in real time.
3. Increase visibility—The ability to understand instantly the financial impact of operational changes and vice versa dramatically strengthens risk mitigation capabilities. When holistic project status reports and KPIs are available in real time it enables project managers and other stakeholders to take corrective action and resolve minor emerging issues before they escalate into major problems that significantly affect project performance. This type of instant visibility alone is revolutionary in construction.
4. Institute best practice enforcement—Centrally managed policies, rules and processes promote disciplined behavior and enable companies to enforce best practices across the enterprise with repeatable and scalable business models, emphasizing corporate governance rather than reliance on individual stakeholder performance. Moreover, the ability to effectively analyze past performance provides enterprises the insight required to identify and learn from past mistakes.
To have widespread, long-term success, lean must be applied to the whole enterprise so functional and departmental silos are broken down and replaced with a system of aligned and interconnected processes that allow the entire organization to operate in real time. Only with this top-down, holistic approach can construction firms achieve productivity gains on par with those achieved in traditional manufacturing over the last 20 years and set themselves on the path to becoming boundaryless organizations.