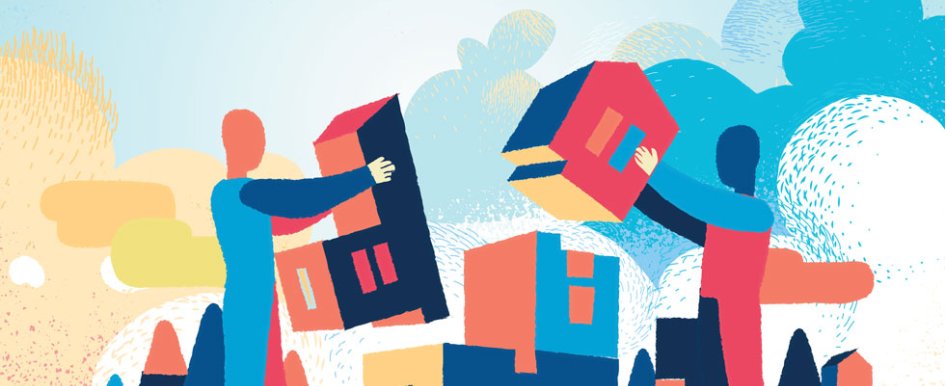
In the last few years, a lot of attention in the industry has been focused on modular construction. The $865 million venture capital investment in Katerra in early 2018 made national headlines, and more recently, the quick construction of two modular hospitals in Wuhan, China, during the surge of COVID-19 cases has led to speculation about the potential future for modular construction in the United States.
In January 2020, Dodge Data & Analytics published the “Prefabrication and Modular Construction 2020 SmartMarket Report,” with primary support from premier partners Bradley Corporation and the Modular Building Institute, and additional support from Pinnacle Infotech, the Mechanical Contractors Association of America and Skender.
Unlike the study published in 2011, the current findings examine prefabrication and modular construction independently by first separating the 608 architects, engineers and contractors who responded to the survey into two groups: those with experience with modular construction and those with experience with prefabrication.
The study only focused on those familiar with these methods. This approach allows for a thorough examination of each method on its own, which is important because, despite the similar benefits that both provide, the drivers and obstacles for further use vary by player and by method. While not an adoption study, since it focused only on using each method, the research makes it clear that experience with prefabrication is far more common in the construction industry than experience with modular construction.
Nearly all respondents (94%) had used prefabrication on at least some of their projects in the last 3 years, but only 38% reported using permanent modular construction. The percentage experienced with modular construction is likely higher than a true industry average would be since the Modular Building Institute was one of seven organizations (including Dodge) that sent out the survey to its members and lists.
The findings in the report help address that gap by revealing the top benefits of using modular and the top drivers and most critical obstacles to increasing use. One of the top findings is the impact of permanent modular construction reported on project schedule and budget performance.
Interestingly, it is general contractors (GCs) and construction managers (CMs) who most frequently report seeing these benefits, and who also see the largest benefit from using these approaches. Nearly all the GCs/CMs report at least some decrease in project schedule (88%) and budget (91%) on their modular projects compared to their stick-built ones.
Almost half of all those experiencing these decreases find that they reduce the project schedule and budget by 10% or more. The percentage of GCs/CMs who report these benefits far exceeds the designers and trade contractors who report experiencing the same with modular construction. This is notably different from the findings about schedule and budget impacts from the use of prefabrication, where the trade contractors are the biggest beneficiaries of its use.
Improved schedule and budget performance are not the only benefits commonly reported by GCs/CMs in their use of permanent modular construction. Nearly all (90% or more) also find that it improves productivity, increases cost and schedule certainty and improves quality on projects, and 80% or more find that it reduces waste, improves safety performance and increases client satisfaction. Trade contractors are only slightly less enthusiastic, with between 81% and 89% reporting experiencing these seven benefits on their projects.
The findings certainly suggest that using these methods on projects provides a competitive advantage, with lowered costs, better quality and more dependable schedules. However, even among those using this approach, it is still emerging, as only one third or less of contractors report currently using permanent modular construction on any single type of project.
Within 3 years, though, more of the contractors (GCs/CMs and trade contractors) doing any modular construction expect to use permanent modular construction for health-care facilities, hotels and motels and education buildings (both K-12 and college buildings and dormitories). Those doing work in these sectors may find increasingly that these approaches are being used by their competitors.
Use of building information modeling (BIM) appears to play a role in achieving the benefits reported. Nearly all of the respondents doing modular construction (97%) use BIM on at least some of their project, but only 34% use it on more than half of them, with only a five-point difference between GCs/CMs (38%) and trade contractors (33%) in those using BIM to that degree.
However, the use of BIM appears to correlate directly with improved schedule performance, with 59% of companies (designers, GCs/CMs and trade contractors) using BIM on half or more of their projects reporting that they see improved schedule performance on their modular projects and just 46% of those using BIM less frequently or not using it at all. Several different factors are reported by contractors as having been influential in their use of permanent modular construction so far.
The highest percentages—78% of GCs/CMs and 65% of trade contractors—say that improved productivity was highly influential. Over half regard remaining competitive and safer working conditions as top drivers for their current engagement with modular construction. Over half of GCs/CMs also consider workforce shortages an important influence, while 50% of trade contractors rate owner demand and improved cost performance as key influencers.
Improved schedule performance is the top driver for increasing the use of permanent modular construction in the next 3 years, rated highly influential by about two-thirds of GCs/CMs and trade contractors. Fifty-two percent also consider decreased costs as a top driver for increased permanent modular activity in 3 years. For trade contractors, improved project quality is also rated highly influential by over half (56%).
Since the most important drivers for new activity—improved schedule performance, decreased construction cost and improved quality—are widely reported benefits of modular construction, it may seem surprising that the anticipated use in these methods in the next 3 years is not more robust. GCs/CMs most frequently report significant schedule and budget performance improvements of any of the aparticipants in the survey, but the percentage doing more than 50% of their projects using 3D modules/full volumetric construction is only 17% now.
While that is expected to grow by nearly half (7 percentage points), the total expecting more than half of their projects to be built this way is still under one quarter (24%). This suggests that top obstacles are also critical to understand. When contractors were asked to select the top three factors from a list of eight potential obstacles, lack of owner interest in a modular approach and the availability of modular component manufactures are most frequently chosen.
This is again in sharp contrast to the prefabrication findings, where project owners are not considered highly influential in the use of that method. These two elements combined together suggest that this is a maturing market, one which needs greater owner awareness of its benefits along with more capacity in the market to fully achieve its potential.