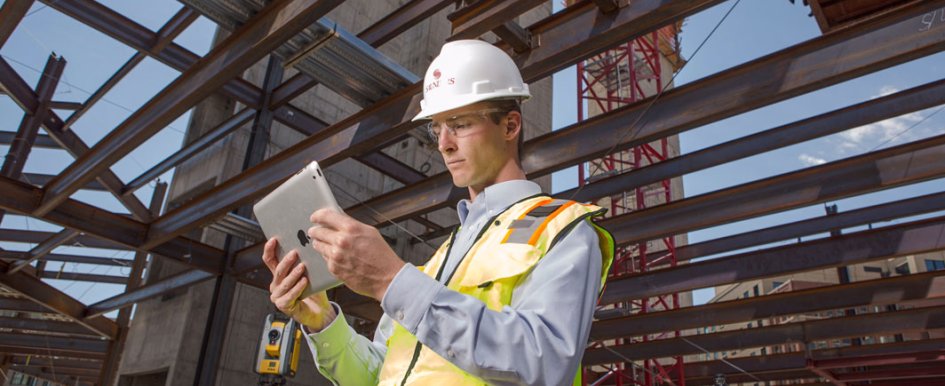
There’s a paradigm shift happening in our industry. Ready or not, every company involved in construction—no matter what phase it supports in the building lifecycle—must now also consider itself a data company. When we design, construct and operate a building, we’re not only constructing walls, columns, beams and roofs, but we’re also creating mountains of data on the jobsite and in the office. This data is collected in a myriad of file formats and disparate workflows and then stored in silos and often incompatible repositories.
How well we use data to drive better decisions and to deliver projects more efficiently, more sustainably with higher quality and with lower costs and fewer risks is what defines the next frontier of construction management. It is our most significant challenge and our greatest opportunity. To that end, implementing technology that transforms the way project information is delivered and consumed is more important than ever.
The Dark Side of Innovation
Cloud computing and mobile technology have radically changed the way we create, track and share data on the jobsite and in the office. Virtual design and construction (VDC) methods and building information modeling (BIM) have streamlined collaboration and transformed relationships among architects, engineers, contractors and owners. Emerging technologies like unmanned aerial vehicles (UAVs), the internet of things (IoT) and wearables are creating new applications for capturing and analyzing rich data on complex jobsites. Mixed reality is merging real and virtual worlds to produce new environments and visualizations where physical and digital objects coexist and interact in real time—transforming the way construction professionals consume, communicate and interact with data. Cloud computing is enabling ubiquitous, on-demand access to shared resources, allowing rapid product development and unprecedented data processing capabilities.
However, there is a considerable consequence to this innovation. As technologies evolve and come to market at rapid speeds—and projects become more complex and larger in scale—the amount of data created and accessed across the planning, design and construction project lifecycle is extraordinary, making it difficult for stakeholders to find the information they need, analyze it efficiently or share project data downstream. Project managers have been hit hardest, now having to add “data Sherpa” to their already long list of responsibilities.
Construction organizations must extract data from these silos and make it available through more easily accessible and spatially organized interfaces. General contractors looking to restore project control should consider these strategies that focus on data centralization and project intelligence.
BIM-Centric Project Management
Drawings remain the preferred way of interacting with project information in the field and in the office. Moreover, BIM is evolving beyond design to become an invaluable process for construction management. With a BIM-centric workflow, markup drawings and models provide spatial context and can indicate areas or places that require the attention of team members. These markups can be associated with project data such as requests for information (RFIs) and submittals, therefore creating the spatial reference for this information, which makes it easier to consume and use in decision making. For instance, if potential change orders (PCOs) can be created and assigned directly from the jobsite, how much time would it save? Or, imagine a scenario in which emails are automatically generated to notify appropriate contacts of an RFI initiated by recognized changes to the 3-D model. In an environment where critical project data and project changes can be captured and shared instantly, project visibility and transparency will improve dramatically.
Elemental thinking
Thanks in part to the deluge of information and shifting digital preferences, project management has become heavily focused on data and file management. However, this can be counterproductive. General contractors will need to shift their thinking away from files and toward elements in order to successfully take BIM to the next level and to continue to leverage data across the project in more productive ways. To get there, contractors should look for solutions that will help to increase the level of granularity and control over processes. More than a visual representation of the building, today’s centralized project management tools are taking BIM beyond the traditional design function to effectively coordinate the design, quality, production, delivery, schedule and assembly of building elements. Using this approach, general contractors can visualize how proposed design changes will impact the schedule and project costs. Specialty contractors such as mechanical and electrical contractors, as well as steel and concrete fabricators, have already converted their BIM processes to elemental thinking. This means that centralized data sources and construction-ready BIM are embraced from the onset of projects, and in doing so these contractors have adopted prefabrication as an integral part of their business workflows. General contractors should follow their leads and look to apply elemental thinking to support reduced risks and more predictable schedules, not to mention better collaboration, lower assembly costs and reduced maintenance costs.
Proactive Project Management
Many believe the building process is rife with opportunities for reinvention. The McKinsey Global Institute estimates that the world will need to spend $57 trillion on infrastructure by 2030 to keep up with global GDP growth. This is a massive incentive for players in the construction industry to identify solutions that transform productivity and project delivery through new technologies and improved practices.
For project management, this means shifting from a retrospective, or as-it’s-happening, project tracking and data recording function to a proactive and predictive forecasting function. This is only possible if the right project controls and building data are added to models and plans earlier in planning stages, are processed in an efficient and timely manner and stored in a way that is easy for future retrieval. Only then can project owners get ahead of the workflow and utilize the invaluable project data for timely decision making, useful analysis and forecasting.
Other industries have gone through similar transformations. Implementation of the six sigma methodology—a disciplined, data-driven approach for removing the causes of defects and minimizing variability for process improvement—has had an enormous impact on companies. For example, Motorola estimated it saved $15 billion in 11 years using six sigma; GE achieved annual benefits of $2.5 billion; and Honeywell saw more than $800 million in savings. These savings would not have been possible without data analysis. Data is necessary before improvements can be implemented, and this is the big opportunity for construction.
Moving forward, advancements in project management applications that combine modeling capabilities with the ability to manage data on the element level will deliver optimized project intelligence for general contractors. Next-generation project management tools can also help construction companies effectively manage and leverage the growing tidal wave of project data created on the building site every day. By moving project data beyond individualized containers to a centralized common environment, data can truly become an asset, and the insights gained can lead to better outcomes and risk management for contractors and project owners.