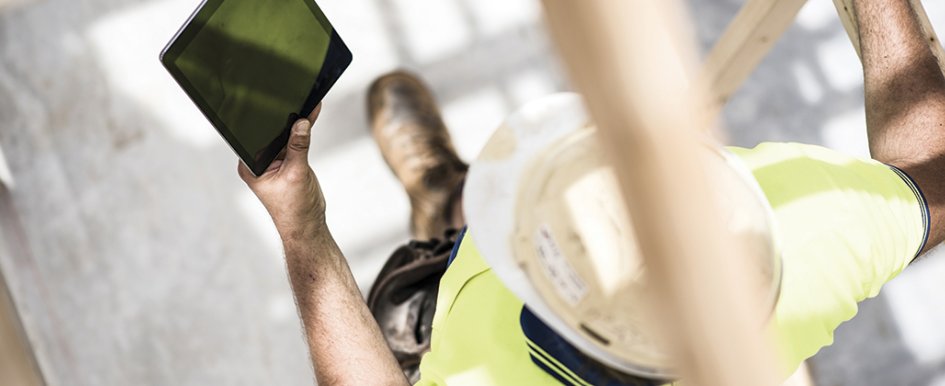
Effective materials management can either make or break project success. Efficiently moving materials through the construction supply chain and installing those components according to code rests at the core of successful project scheduling, quality, safety and cost. Yet, many project managers do not approach materials management with the appropriate levels of rigor and discipline.
Too often, the best-laid plans are fast-tracked to shorten delivery schedules. Those changes can potentially impact thousands of materials and supplies sourced from different vendors and locations. Add to that the inherent unpredictability of building construction due to issues like weather delays, materials shortages, regional regulations, cost variances and labor shortages. Labor and materials are undeniably the two highest cost categories of any project's operations. Although they occupy separate line items in the project's estimate and budget, labor and materials are closely linked. When material is not available, employees cannot execute the assigned work. Each acts as a driver for the other.
According to a study conducted by Electri International, about 40 percent of laborers' time in the field is spent on non-value-added material handling or on moving materials on the jobsite that don't end up in installation. Contractors can reduce labor waste by optimizing material tracking and commissioning on the jobsite. To maintain effective project control, the real-time status of materials must be carefully tracked and coordinated with labor and equipment and optimized through the entire project lifecycle—from proposal and design to fabrication, transport and receipt, throughout installation and QA/QC and into ongoing facilities management.
Manual Processes Wreak Havoc
Supplies and equipment are often tracked and sourced using a collection of disparate applications, spreadsheets, documents and PDF files stored in different locations, making it difficult to gain visibility into materials status and maintain real-time accuracy of that progress.
A typical workflow may involve a procurement or supply coordinator tracking inventory of materials and components off-site. Once delivered to the jobsite, materials managers and quality controllers inspect installation by making notes on paper logs and then manually updating progress reports back in the office.
Any fix, adjustment or change order kicks off another round of timely manual tracking and reporting. One small error or delay in the transfer of that information, especially when the status of that information is held up by manual processes, can initiate a snowball effect, creating cost overruns and delays in project completion and reducing overall project performance.
While easy to use in the field, many popular mobile punch-list applications produce separate reports that cannot be used downstream and require manual integration of outputs with the core project management database.
The need for data integration has escalated. Some firms now have dedicated information coordinators on staff to ensure project information is up to date and leveraged adequately to inform decisions. Not only is this costly, but it makes it extremely difficult for project management to have visibility into the current status of projects in order to make necessary and timely scheduling adjustments.
An increase in prefabrication and modular construction is placing new demands on materials management as well. Introduced to improve quality and accelerate speed by being produced in a conditioned environment, prefabrication requires an increased need for detailed planning of fabrication, delivery and installation. In particular, tight, inner-city jobsites require "just-in-time" delivery of prefabricated components due to a lack of storage space.
Project managers and engineers need to know the exact status of required components, when they can be delivered and whether the components match the defined quality specifications. Real-time access is key, so spreadsheets are not the ideal medium for maintaining this information.
Complete & Connected Workflow
Advances in mobile field technology and the Internet of Things have transformed the materials management workflow, enabling new levels of efficiency and accountability.
New processes utilizing mobile devices, barcodes, QR codes and RFID connected with BIM and project management software allow field personnel to easily and quickly identify materials in the field and perform tasks, such as updating supply chain status, recording attributes, entering material checklists, managing issues and capturing photos and video.
Automating materials tracking and commissioning within the primary project control system eliminates manual steps and errors, reduces project risk and transforms productivity to deliver the following benefits:
- Maintain real-time status of supply chain—Combining mobile field technology and barcodes, QR codes or RFID tags enables field workers to quickly and easily update material attributes and automatically log supply chain status at every step of the project lifecycle. Materials can be defined within the BIM or design drawings and verified for constructability. During fabrication and transport, components can be scanned and tracked as they enter the supply chain, providing critical information to verify on-time delivery, optimize schedules, increase productivity and control costs. The ability to have material, labor and equipment on the jobsite at the right time, in the right place, is what determines a project's overall success.
- Standardize QA/QC procedures—During construction, scanned materials can automatically trigger installation checklists. Those QA/QC checklists ensure materials are installed correctly and perform as designed. Safety checklists can be assigned to materials and installations to ensure field workers adhere to proper protocols or procedures to improve security measures and reduce the risk of errors and accidents.
- Improve project handover—Tracking material component attributes, installation history, operation manuals and work orders can improve project handover. Facilities managers and building owners need detailed information about the makeup and performance of the building. During the preconstruction and production phase, a large amount of information about installed components is collected. This information is critical for successful operation of a facility and often needs to be reproduced manually by searching in digital and physical storage areas.
Materials affect every aspect of building construction, including the ability to schedule work and assess project performance throughout the project's lifecycle.
With today's increasingly complex and unpredictable construction environment, a robust and tightly integrated materials tracking and commissioning process is essential. Every construction project presents an opportunity to improve both delivery and owner satisfaction to, in turn, achieve greater profitability.
Automating materials management enables construction business owners to improve efficiency and accountability, eliminate costly manual steps and errors, reduce risk and capitalize on an opportunity to deliver more profitable building construction projects.