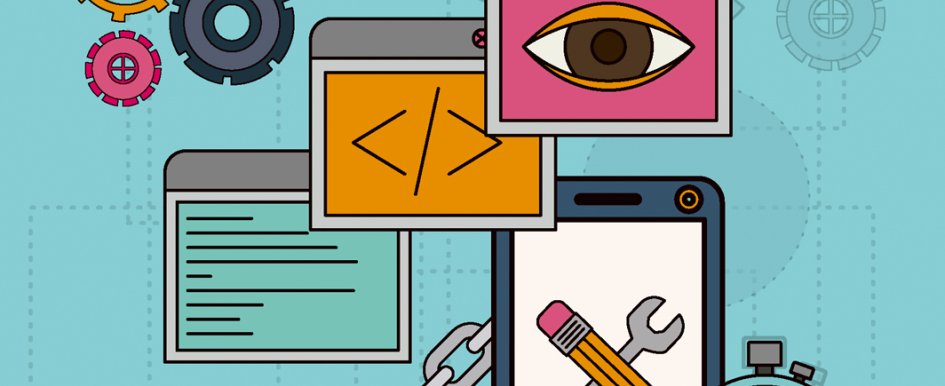
Relationships within a construction project are numerous and complex. Owners, subcontractors, general contractors, architects/engineers and other partners create a plethora of information that must be communicated accurately in order to produce a world-class project. And just like building the project itself, to effectively collaborate you need the right tool.
The relationships between cement companies, ready mixers and contractors is a variety bag with traditional processes of calling in orders and tracking with paper and pencil. The digital transformation in construction has been slow on adoption as compared to other industries, but most recently it has been taking hold in areas of building information modeling (BIM), project management and applications that connect the office with the field.
The ordering and scheduling of materials in the concrete industry, along with the visibility, tracking and documentation of the steps along the way, improves project timelines and fosters the synergy and collaboration of all parties—not to mention it raises the quality bar. Yet, so few tools are available that truly enable this transparency in the concrete industry, so change must occur.
Some applications in the market claim to foster communication and bring their own “value proposition.” These range from large-scale project management systems to mobile field applications. But do they really solve the issues that face the construction industry? How do you know which solution is the right fit for the job?
You may have heard the term enterprise resource planning (ERP), and chances are you have worked within an ERP system even without being aware of exactly what it is or means. ERP is a business software that acts like an umbrella of separate applications but is managed by a primary database. ERP systems track resources—such as cash, raw materials, purchase orders and payroll. The system connects different departments—such as HR, accounting and sales—in order to run the business effectively. While the traditional ERP system may have served its purpose well in the past, the rapid changes experienced by the architecture, engineering and construction (AEC) industries require more than a single ERP solution.
Simply put, best of breed technologies and software companies that are agile enough to keep pace with the ever-changing requirements and requests on a construction project are best suited to develop leading-edge solutions. Moreover, as the needs within the construction industry continue to rapidly evolve, it is nearly impossible for any one company to develop and maintain an ERP system that is a one-stop shop, because the ERP system is now being tasked with serving in capacities it may not have been designed to handle. For example, in many instances the ERP system is now being expected to serve the following additional functionalities:
- Collaboration tool—The ERP system is tasked with not only record-keeping of transactions, orders and supplies, but it is also responsible for collaborating across several users in different regions and in different capacities.
- Forecasting—Using analytics provided by the ERP system, companies rely upon this data to forecast inventory needs and gain insight into the effectiveness of their supply chains.
- Mobile environment—Going mobile is not a trend but rather a new requirement in doing business effectively in real time. The ERP system is tasked with communicating mass amounts of data within a single application.
- BIM—Over 80 percent of all construction firms have one form of a BIM system or another, according to a 2014 Building Design Construction BIM survey.
What if an ERP system misses the mark in handling these tasks? It will, as with all ineffective software, have a direct negative impact on profit and productivity. So, what is a reasonable solution? According to Mike Oster, CEO of Gemba Technologies and former CIO at McCarthy Building Companies Inc., in order to have a competitive advantage in today’s economy, the best approach is to develop a systems integration plan (SIP) that analyzes all the touch points between the two systems, and then obtain an application programming interface (API) software product to build the integrations. It is important to work alongside your software teams to ensure that no data is left behind.
As the AEC industries continue to evolve, a natural progression of technology adoption will be in value-added applications that integrate with ERP and larger systems. The benefits of automating processes, such as the current antiquated concrete ordering process, will pay dividends in production quality, efficiency, visibility with real-time collaboration and risk mitigation due to digital documentation.
Simplifying the complex collaboration challenges within the AEC industries is achievable when the right tools are put into place. The benefits of employing automation and collaboration tools not only lead to better project management and success, but also to savings to the bottom line.