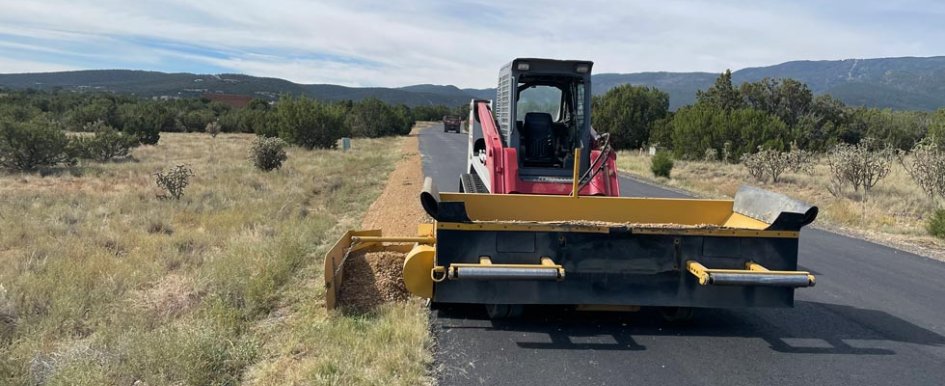
With increased infrastructure developments on the horizon, road repair projects will follow. To keep up with demand, contractors need to evaluate their fleet to look for ways to improve efficiency while keeping in mind both their crew’s safety and company’s bottom line.
Attachments provide a realistic, effective solution to this challenge by utilizing equipment that contractors already own. This is done by changing workflow, minimizing maintenance and lowering equipment cost to allow for smarter labor and increased return on investment (ROI).
The following are three ways attachments are changing the foundational methods of road construction.
1. Streamlined Processes
Road construction tasks like backfilling and aggregate placement have typically been viewed as a four-step process. Roadway materials are piled on the road, scraped into place, compacted, and then crews sweep and clean off what remains on the road. Although larger machines and added crew members can help complete projects, another perspective to increase efficiency and safety is to minimize the number of steps in the process with the use of material placement attachments, which can cut down on labor by 50%.
With this method, a single operator connects their skid steer, loader or other common host machine to the attachment and loads road material into the hopper at the top. Then, the operator drives alongside the road as material feeds down the hopper onto a conveyor, which then carries the material to the edge of the attachment, dispensing it through an adjustable-width opening to exactly where it is needed. Some attachments can even dispense up to 20 tons of aggregate in under 10 minutes with all machine adjustments made by a single crewmember from inside the host machine using a remote control.
Streamlining the process both saves money and makes money. Crews can not only do more work in a day, but also do more with their budget by cutting steps without adding more self-propelled machines or workers. And those savings continue into the future with a drastically lower cost of ownership when compared to self-propelled machines.
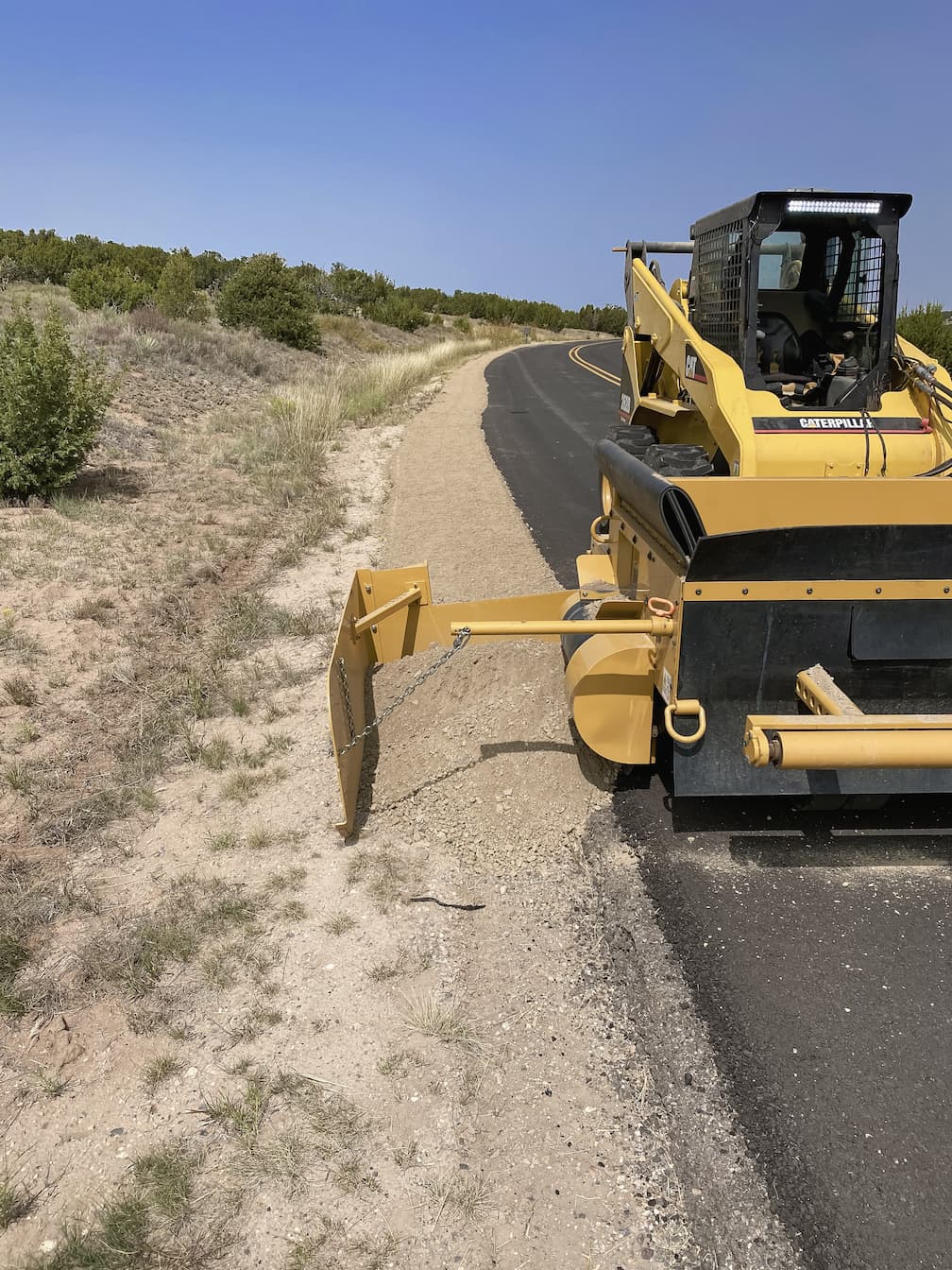
2. Reduced Maintenance
In an effort to minimize maintenance, material placement attachments can connect to both the engine and hydraulics of common, proven workhorses, such as skid steers and loaders (both wheel and track). In the case a host machine needs to be serviced, crews can quickly and easily hook up the attachment to another machine.
Without an engine or transmission of their own to maintain, these attachments have the power to reduce maintenance by up to 90% with just a few grease fittings to look after. Plus, cutting out the unnecessary parts slashes prices by up to 80% and allows contractors to invest in the host machines they know will support their fleet from multiple angles, not the paving machines that see months of offseason.
Overall, material placement attachments are low maintenance and cost significantly less than self-propelled machines but also provide savings by repurposing labor.
When considering this type of equipment, look for manufacturers that offer an optional universal mounting plate and easy hydraulic connections for their attachments — also note whether they can connect to any host machine in a fleet.
One advantage of choosing an attachment with a compact design means fewer parts to keep track of, fewer transportation requirements and less jobsite clutter. Another benefit is the ability to conveniently fit the attachments on the same trailer as the host machine to be transported to and from jobsites.
3. Heightened Efficiency & Safety
Remaking road construction by utilizing attachments reduces unnecessary steps, lessens the amount of equipment needed and drastically lowers maintenance requirements, but that doesn’t mean crewmembers await a similar fate. Contractors now have the freedom to assign these crewmembers to different tasks that benefit the project to keep getting work done, especially in times when labor is scarce. This efficiency lets contractors put crews to work in areas they didn’t have the capacity to work in before, and can also help to expand their road construction operations altogether. Contractors report up to 50% savings in labor, which could potentially double a crew’s work capacity when using road construction attachments. Labor savings can benefit crews from a safety perspective as well. It’s one thing for a machine to go down, but what about a crewmember? Road construction is a high-risk job. Crowding numerous crewmembers around a roadside to spread out materials or to make machine adjustments is an unnecessary risk.
However, utilizing attachments that cut out multiple steps in the process takes crewmembers out of harm’s way. Additionally, remote-controlled attachments allow the host machine operator to remain in the cab while adjusting the dispensing speed and machine positioning.
The Road Ahead
With deteriorating road conditions and the limitations of traditional machinery, manufacturers today can offer contractors a road maintenance game changer through the use of attachments.
Material placement attachments, in particular, prove to be assets, not only in times of infrastructure crisis, but also in creating a system of sustainable roadway management.