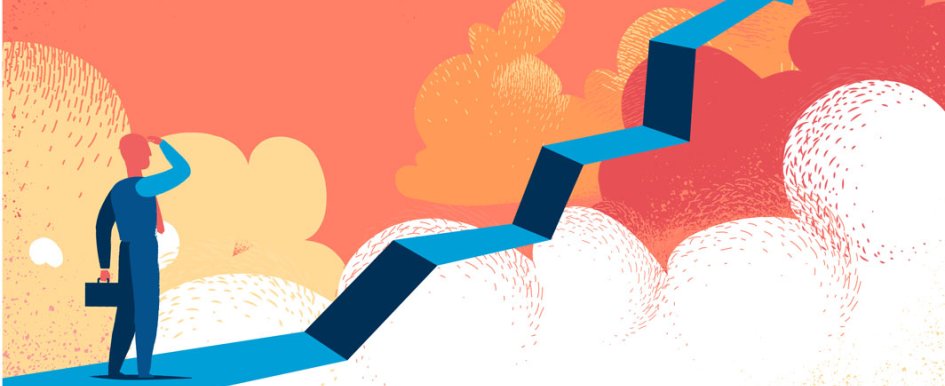
This month, the construction industry will converge in Las Vegas for World of Concrete 2019. Many show attendees will be looking for hydraulic attachments to help them maximize productivity and profitability in the construction season ahead.
But, with so many different applications and myriad hydraulic attachments to choose from, selecting the proper attachment can be a challenge for construction business owners and managers. To assist you in the process, following is an overview of the 10 major types of hydraulic attachments and their applications.
1. Breaker
Hydraulic breakers are the oldest hydraulic attachments for carriers. They are designed to break any kind of rock or concrete with any hardness level or other physical property. Applications include demolition, deconstruction, primary rock excavation, secondary rock breaking, trenching, foundation work, asphalt cutting and many others. These attachments have a high level of breaking force, to power through materials quickly, and require minimal routine maintenance, which makes them a cost-effective option with minimal downtime.
Breakers are available to match any excavator, backhoe or skid-steer loader. Over 60 years, development of the hydraulic breaker has produced advancements, such as self-lubricating systems, sound and vibration dampened systems, automatic rock hardness adjusting systems, energy recovery, the intelligent protection system, the solid body concept, and many more.
2. Bucket Crusher
A bucket crusher is a small jaw crusher that is mounted onto a carrier. In the most common setup, the bottom of the bucket is fixed, with one moving jaw crushing the material against it. This jaw is moved by an eccentric element that is mounted on an axle being rotated by a hydraulic motor. For adaptation, it normally requires pressure and return lines and one free shock line to the tank.
Bucket crushers are used to crush the demolition materials used for backfilling on a new building or to be transported to a customer. On construction sites, they can crush the stones excavated from the jobsite, and the aggregate can be used for construction. In quarries and gravel pits, they can crush small amounts of soft stones and boulders that have been prescreened.
3. Combi Cutter
Combi cutters, or multiprocessors, are designed to enable a single-host frame and cylinders to accept different, interchangeable jaw variations—each designed for a specific application. There are various working jaws available, including concrete cutting, pulverizing, steel cutting and more. They are found on demolition jobsites and are mainly used as primary demolition cutting tools.
For optimum operation, combi cutters have 360-degree integrated rotation devices, and the hydraulic installation on the carrier is more sophisticated than other hydraulic attachments, such as breakers. While breakers require a single direction hydraulic circuit, combi cutters require a bidirectional circuit for opening and closing and an additional installation for rotation functions.
4. Compactor
The compactor is ideal for compacting soil on slopes or in confined places where self-moving plates or rollers cannot operate, such as pipeline backfills and road or railway slopes, making it possible to add thicker layers on a backfill. Compactors can also be used for installation and extraction of sheeting, piling, posts and other formworks. When used with a quick coupler, the same excavator can easily perform filling and compaction without waiting for a separate machine.
5. Concrete Buster
Concrete busters are similar in appearance to combi cutters when they are equipped with concrete cutting jaws. However, they have a much larger jaw opening than comparable sizes, and they are stronger in design. Concrete busters are used for thick concrete wall structures, such as building foundations, or for very tough applications, such as long front demolition where the operator has restricted visibility. The focus on these machines is to have the widest possible jaw opening to better bust thick concrete walls.
6. Drum Cutter
A drum cutter is an attachment in which rotating drums, equipped with picks strategically positioned around the outer diameter, are rotated by a hydraulic motor at relatively low revolutions per minute to cut rock, concrete or frozen ground. The picks are wear-resistant and exchangeable. Drum cutters can be used for rock excavation, demolition, underground scaling, tunnel profiling, trenching and other applications. The excavated material can then be used for backfill without separate crushing.
7. Grapple
Grapples are universal tools for demolition, sorting and loading all kinds of materials. The basic structure is simple: a rigid main body with two moving jaws mounted on both ends of the frame. The jaws are powered by two to four hydraulic cylinders, and they are connected together so that they move simultaneously. Grapples are also equipped with a powerful hydraulic rotator for ease of picking, sorting and positioning the materials being picked up or set into place.
Grapple design is based on which specific features are needed for your applications. For sorting, it is essential to have fast movements and precise control of the jaws to penetrate the pile easily; while for demolition, it is more important to have a powerful, strong tool with more weight. For even more versatility, it can be equipped with various accessories for different applications.
8. Magnet
The magnet is a self-contained attachment in which a generator, powered by a hydraulic motor, creates a magnetic field below the bottom plate. The magnetic force is used to hold steel particles, rapidly demagnetizing them so that the particles drop immediately. The operator controls the functions by means of the auxiliary hydraulic system and remote control.
There are no other connections needed. These magnets are used in demolition and recycling applications for loading and separating out steel from other materials. They are ideal for removing the steel from demolition and construction jobsites, tunnels and bridges where steel can harm pedestrians or puncture tires.
9. Pulverizer
A pulverizer crushes demolished material between one fixed and one moving jaw to reduce the particle size and to separate iron from other materials. There are two main categories of pulverizers—bulk and demolition. A bulk pulverizer is designed to pick up demolished material from the pile. Therefore, many contractors do not need a rotator for it. Without a rotator, the machine is lighter and can perform more precise and shorter movements for maximum digging power.
A demolition pulverizer is designed to crush the material (straight from the wall) and pick up the iron. These attachments are usually equipped with a hydraulic rotator for easier positioning and are particularly good for renovations where it is critical to avoid causing damage to surrounding structures and there is no room to handle the falling debris or rubble.
10. Shear
A steel shear is an efficient tool for demolishing steel structures with large plates or girders. Typically, steel shears have a fixed pair of jaws and a single, nonfixed jaw that moves between them, cutting the steel like scissors. For maximum cutting force, there is a large hydraulic cylinder, which makes the frame very long compared to the jaws. Steel shears are equipped with hydraulic rotation, and they need two, two-way hydraulic connections.