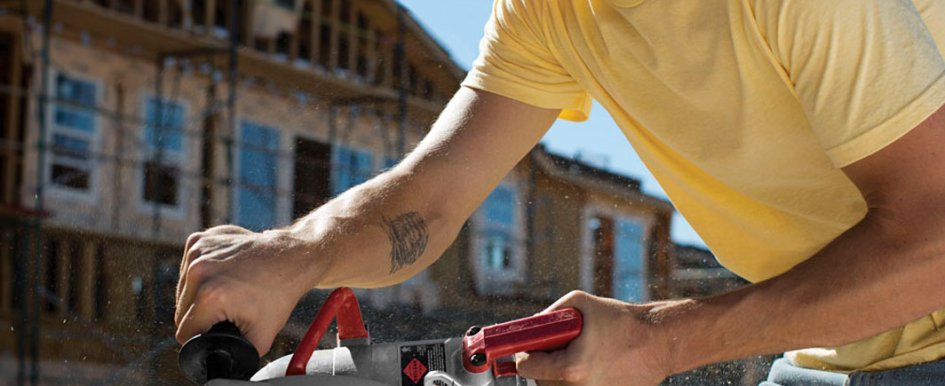
Jobsites are generally dirty, unforgiving places. They are the product of a hard day’s work, and the reason why so much emphasis is now placed on dust-control solutions. But at the end of a day’s worth of grinding, sawing and drilling, keeping your equipment running in the best possible shape comes down to prioritizing tool maintenance. Properly maintaining your suite of tools keeps them running harder for longer periods of time before the eventual replacement.
More than the cost savings, though, proper equipment maintenance ensures the safety of your workforce on the jobsite. Sure, you get the oil in your car changed and the tires rotated because you don’t want it breaking down on the highway, resulting in a wasted day at the mechanic and an unwarranted bill. But more than that, you do it so your car doesn’t flip into a ditch.
The same is true for tool maintenance. While the short-term goal may be to save money on replacement equipment, every business owner knows that maintaining a safe work environment contributes to the success of his/her employees and
the company.
In fact, according to a 2016 report from the United States Bureau of Labor Statistics, professionals in the construction industry need to take roughly 10 days away from work after suffering from a job-related injury or illness. That means maintaining your equipment quite literally translates to safety and productivity on the jobsite. Here are a few key tips for keeping your equipment up to the task.
1. Keep the Motor Running Smoothly
It seems obvious enough, but it bears repeating: keep your tools clean. Both dust and moisture are killers on the jobsite. They can affect tool performance and overall lifespan. Because of the upcoming OSHA regulation regarding silica dust, concrete tools will soon need to have dust-control solutions. However, it is still wise to ensure your tools, specifically the motors, are dust free. The easiest and most efficient way to clean your tools at the end of a rigorous workday is to pull out the air compressor. Focus on a tool’s motor and any areas where there is motion, like a foot plate or blade guard on a saw.
Next, know your equipment and what it needs to run smoothly. For example, did you know the lubricating oil in a worm drive saw needs to be replaced annually? Or if you are experiencing excessive arcing or sparking, did you know it’s time to replace the motor brushes? Knowing your tools’ needs can make the difference between a total replacement and a simple repair.
2. Notice the Cords
While cordless tools are becoming more powerful and realistic to use on a jobsite all day, the job at hand often still calls for its corded counterpart. It is just as important to inspect your tools’ cords and extension cords as it is the equipment itself. Examine the cords on a regular basis to make sure there are no tears or exposed conductors. Once you have cut the jacket or insulation, you should replace the cord entirely. Some safety officers bring a colored roll of tape with them to inspect a jobsite. Should the cord pass the test, they wrap the colored tape around a small part. That way, they know it was inspected and can keep track of all the tools. The next time they visit, they bring a different color, which helps them keep a visual record of inspections.
3. Remember Maintenance Starts with Your Crew
Cleaning your tools, making proper replacements and checking the cord are all important, but in reality, the best way to get ahead of any maintenance issues is by maintaining your people.
By ensuring your team is properly trained, you can be more confident that your company’s tools are being used properly, which leads to less maintenance overall. This includes general safety instructions as well, such as reminding the crew not to violate a tool’s safety guards and features or setting tools down in a location where they won’t fall or get damaged.
Many workers come to the jobsite with the appropriate skills gained during years in the field, union training or having gone to a vocational school.
But for those without that kind of experience, individual manufacturers can visit a jobsite and put on a training seminar regarding their equipment. This is especially important when new specialty tools come out that haven’t existed in the market before. Owners need to make sure they are reading the operation and maintenance manuals and that their crews know how to use them safely.
Proper equipment maintenance is essential to a functioning jobsite, a profitable business and a safe team. By taking an extra step to be concerned about both your tools and your people, you can create an atmosphere that facilitates success.