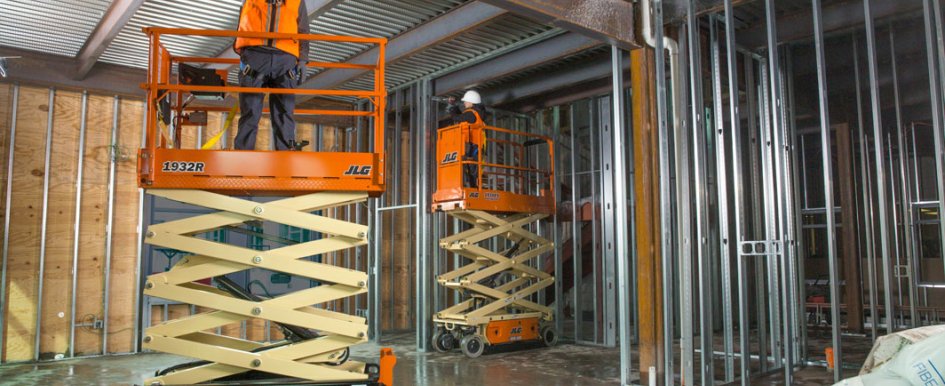
When it comes to scissor lifts, there are several factors to consider before you can decide which machine is best for your particular application. What’s your budget? At what height do you need to work? Will you be working inside, outside or both? Will you have access to a power source for charging the machine? How much weight will you need to lift? What features are must-haves? The list of considerations can be virtually endless.
However, there are a handful of questions you should be certain to ask when purchasing or renting a scissor lift. Your answers to these questions will help guide you toward the right unit for the job, in terms of general specifications. But, as with all equipment, additional features beyond height and weight differentiate one machine from another. So, while all scissor lifts may look similar, they are not the same.
Many scissor-lift models allow operators to complete one specific task, but how efficiently and safely that task is accomplished, as well as the serviceability and durability of the machine, are impacted by the model. Add to that the advanced technologies built into the machine, and you’ll quickly find there are several differentiating factors among various brands that can impact your return on investment (ROI). As such, it is imperative that you do the necessary research and choose wisely.
1. What type of drive system does the machine use?
There are typically two drive systems used in powered lifts: hydraulic and electric. Hydraulic drive systems take electrical energy from the batteries and convert it to hydraulic flow. While hydraulic machines typically cost less to purchase or rent, they can be less efficient and, in turn, more expensive to operate compared to electric drive machines.
Electric drive systems have batteries directly linked to motors on the drive wheels, making them more efficient overall. These systems require less hydraulic oil, which helps to reduce issues with oil viscosity, and renders them better suited for colder environments.
Further, electric drive lifts significantly reduce the number of leak points because they require less hoses, fittings, manifolds and other components that are critical to their hydraulic counterparts. Electric drive systems also boast increased battery life and require fewer replacement parts.
2. How is the power output managed?
Replacing batteries on a scissor lift can be expensive, making it critical to have battery-management software that allows the lift to consistently operate at peak performance. While contractors often try to maximize the run time of a lift, doing so may sacrifice the long-term durability and reliability of the machine’s batteries.
For example, when the battery starts to drain during a shift, the output voltage also begins to drop. The battery logic helps determine how low the voltage can drop. However, the lower the voltage drops, the more the long-term durability of the battery is compromised.
Power management is a critical ROI consideration, and equipment owners should consider working with manufacturers that offer solutions for optimizing work times and cycles while protecting the long-term battery life.
3. What equipment protection programs are available?
Pothole-protection systems lower the ground clearance of an elevated lift to reduce the risk of an accident if the machine hits a pothole. Some equipment manufacturers pin the system to the machine’s service doors, which can cause it to move in and out of alignment. Mounting the system to a stationary component, like a chassis, helps prevent alignment issues, resulting in less service and more uptime.
Additionally, many manufacturers rely on duplicate components (limit switches, plungers, etc.), which can increase the risk of system failure. Manufacturers that use one limit switch and one plunger help reduce the number of components needed to safely activate the system.
It’s also important to consider what the system’s limit switches can handle. Systems with lower tolerance can move the protection mechanism out of position, causing the equipment to have to be serviced.
Machines designed for high tolerance will help keep operators on the jobsite and increase productivity. These small differences in pothole protection design make a big impact on uptime.
4. What technologies or innovations come standard with purchase?
As technology has progressed, some manufacturers have pursued solid-state electronics. A decade ago, when a machine experienced an issue, diagnostics were done through the swapping of relays and fuses until the machine’s fault code disappeared. Today, improved technologies, like solid state electronics, provide multiple benefits to both end users and fleet managers.
From an end-user perspective, solid-state electronics provide operators the ability to get fault codes so that they can quickly determine the issue with a machine. This allows operators and end users to better communicate with their service team or servicing company to begin troubleshooting and diagnosing the problem. The next generation of technicians is anticipated to be more comfortable connecting to the machine’s controller area network (CAN) bus system through a service diagnostic tool, which is essentially connecting to the “brains” of the machine.
The service diagnostic tool can be used to monitor the machine’s critical components. In many cases, the machine will point a technician directly to the component or part that is experiencing the issue.
5. What type of load-sensing system does the machine use?
There are two types of load-sensing systems (LSSs): force-based and pressure-based. A force-based LLS acts like a bathroom scale by providing a reading that calculates how much the pin has been compressed, showing how much weight is on the scissor lift. It provides an accurate measurement that does not need to
be calibrated.
A pressure-based LSS measures pressure on the barrel side of the lift cylinder and translates that pressure reading into weight. While it costs less than force-based, pressure-based can pose a challenge in colder weather. Since hydraulic oil moves slower in colder temperatures, it is harder for the piston to push the oil out of the lift cylinder’s rod-side to elevate the scissor.
This increases the pressure in the barrel, making the machine work under the assumption that it’s trying to elevate a large amount of weight, when really, the sensor is giving a false reading because the oil is so viscous.
To avoid this, some manufacturers have adopted a dual-pressure sensor LSS, which places an additional sensor on the rod side to calculate the differential between the barrel-side and rod-side pressure. This reduces low-temperature error readings.
As you continue your journey to select the right scissor lift for your business, consider the process behind the design of the brand and model you are choosing. While scissor lifts appear similar, they are far from the same. Key technologies and features that drive tangible jobsite benefits can make a big difference to your total cost of ownership and the experiences of the operator, fleet manager and technician.