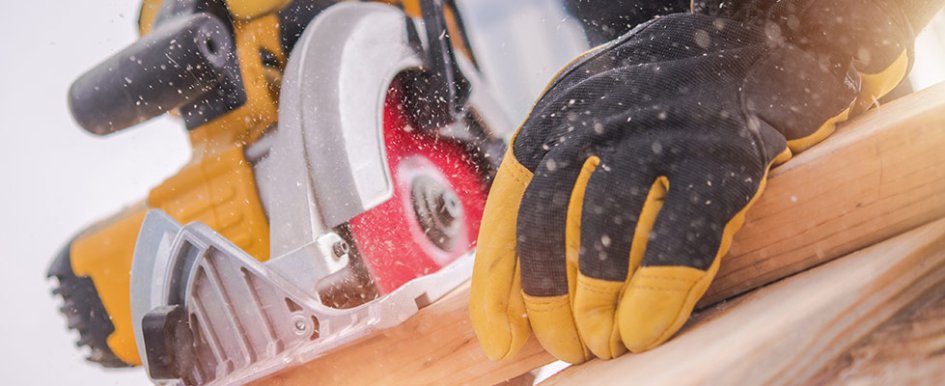
In 2002, the Occupational Safety and Health Administration (OSHA) of the U.S. Department of Labor released a booklet that outlined many of the dangers that power tools present, including exposed moving parts, flying chips and sparks, in-running nip points, etc. Corded pneumatic tools also presented dangers like “being hit by one of the tool’s attachments” as well as their air hoses being prone to accidental striking and tripping hazards. Heavy jackhammers can cause fatigue and strains, while noise presents as another hazard requiring “effective use of appropriate hearing protection.”
That same year, there were 401,330 power tool-involved injuries resulting in emergency room visits, according to data from the Consumer Product Safety Commission of America.
Since then, many technological breakthroughs in the development of cordless power tools have made jobsites and operators safer. Here are five:
1. Cut the Cord & the Trip Hazard & Lock Down Active Jobsites
Unwieldy cords needed to power traditional electric tools on jobsites present a tripping hazard — ranking No. 2 in Pro Tool Reviews’ top eight causes of power tool accidents. An accidental trip is the last thing anyone wants to experience near a spinning table saw blade.
Major breakthroughs in lithium-ion battery technology have led to battery platforms from power tool manufacturers that redefine what can be accomplished on a battery system.
Consider a reciprocating saw, a very common tool needed for demolition. Compared to corded reciprocating saws, cordless saws remove the clunky cord and add a variety of features their more traditional, corded counterparts don’t offer, such as powerful brushless motors, variable speed, smart controls, orbital action, vibration control (less fatigue), pivoting shoes, blade release, LED lights for workspace illumination, rafter or belt hooks, etc.
But reciprocating saws, drills and other common handheld power tools aren’t the only power tool categories that have been disrupted by battery technology — for virtually any application a tradesperson may encounter, battery technology development has been cultivated.
Cordless table saws, for example, not only feature smart controls and the ability to remotely lock out unauthorized users, but these tools can also be locked out after-hours when left on jobsites. This feature helps protect contractors against liability where a potential accident may otherwise occur.
2. Ergonomics
Ergonomics has spurred considerable investment to develop innovation in the development of cordless power tools.
Development in this area has resulted in impact wrenches that shave weight while delivering more power (easier overhead use for reduced user fatigue and superior balance for better control).
But that’s not the only category where ergonomics development has flourished. Ratchets with extended reach offer smaller heads for better access in tight engine bays and undercarriages (while delivering pneumatic performance without the noisy experience and unwieldy cords). Drills, packed with brushless motors, have gotten more compact designs to deliver better balance and control in tight spaces. Grinders feature easier-access switches for increased comfort and ease-of-use when operating in many different, sometimes awkward positions.
Development into other categories that present dangers to workers (e.g., musculoskeletal disorders like “trigger finger”) like overhead utility crimpers has led engineers to solve design challenges and deliver lighter weight packages that improve center of gravity for greater control and require less muscle effort when operating triggers.
3. Greener Power Equipment & OPE
Major breakthroughs in solar power have been seen by companies like Generac and Tesla, but launches of equipment battery systems help introduce fully cordless power generation in the construction industry in a variety of emissions-rich categories:
- Portable power generation — Removing gas emissions that present risks to the environment and worker while also solving issues with electric generators (e.g., trip hazards as well as reduced performance due to voltage falloff)
- Faster, safer demo — Removing gas and musculoskeletal hazards of traditional jackhammers with a lighter-weight, easier-to-use, cordless solution
- Concrete finishing — Removing gas hazards and musculoskeletal hazards with innovative solutions like backpack concrete vibrators and screeds
These types of innovations help the industry reduce their carbon footprint and contribute to a greener built ecosystem. Additionally, power tool manufacturers are actively exploring solutions for solar panel installers (e.g., high-torque impact wrenches designed for solar applications) to help them make installations to solar manufacturers’ specifications with quality assurance (QA) reporting opportunities.
Innovations in the outdoor power equipment (OPE) category, furthermore, have led major manufacturers Ryobi and Club Cadet to release solutions for the landscaping industry. Further, several major manufacturers have developed categories like battery-powered chainsaws, blowers, hedge trimmers, sprayers, spring trimmers, etc.
4. Safer Installations
Kickback has long been a hazard of using power tools — e.g., drills violently propelling backward in bind-up situations, saws (table saws, miter saws, reciprocating saws) encountering knots that cause their sharp blades to not only risk damage to materials but also to spin back toward operators and result in emergency room visits.
Modern-day power tools use advanced technology like machine learning to prevent these situations from happening and protect users with enhanced safety. Describing the development of this feature to IEEE Spectrum Magazine, an engineering director for power tool technology at Milwaukee Tool said, “We’ve collected thousands of runs of data to develop an algorithm that can reject false trips. This would not have been possible with using sensor data to make the decision.”
5. Quality Assurance
In addition to protecting users against kickback, breakthroughs in other categories, like electrical installation, have led to new-to-world technologies that install fasteners faster, verify precision digitally, and streamline a once two-tool process to help protect users against musculoskeletal disorders from repetitive motion injuries encountered torquing.
What’s more, these tools have been used in the field to provide quality assurance to customers of specification-level precision fastening on critical fasteners that can be verified via web-generated reports. Similar reporting capabilities can verify to teams the utilization in hydraulics tools, while precision fastening in impact guns, furthermore, have been used by heavy-duty mechanics to achieve certification-level of fastening tightness via smart controls.
Bottom Line
In the 21 years since OSHA’s power tool booklet, massive breakthroughs in cordless power tool technology have seen these tools get safer and smarter while delivering tremendous performance. Battery technology is an ever-evolving space, and we’re sure to see even more disruptive innovation in the next 21 years.
That said, there has never been a better time to cut the cord.