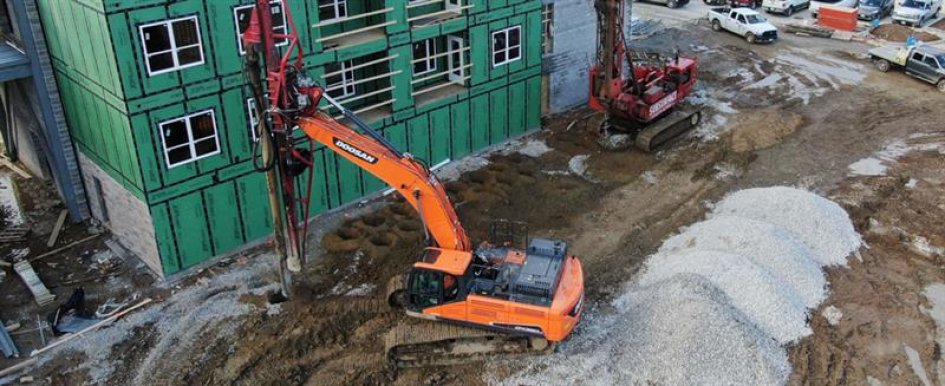
Finding the right attachment to do a job better or more efficiently can give your company a competitive advantage. And you may be able to expand your company’s services by adding attachments to your fleet. The following are stories of entrepreneurs who have successfully used attachments to gain an edge over competitors.
1. Excavator: Vibratory Probe
Subsurface Constructors of St. Louis, Missouri, installs aggregate piers, also called vibro stone columns, by using a mast-mounted vibratory probe to compact stone into columns. After learning about the equipment from a company in the U.K., Subsurface became among the first companies to bring vibratory aggregate piers to the states. The firm designed its own special mast that’s central to the process. As a vibratory probe on the mast is pushed into the earth, soft soil is displaced to make way for stone that are compacted with the probe.
Subsurface originally intended to affix their masts to rental units nationwide. But the scattershot availability of rental excavators prompted the company to partner with an equipment manufacturer that would be responsive to their needs and be able to work with them nationwide.
2. Excavator: Drill
Oscar Orduno, Inc., is a construction firm in Texas that builds permanent retaining walls. Many of the company’s earth retention projects are located in the expanding Dallas and Austin areas. The company pairs its crawler excavators with a specialty drill attachment powered by the hydraulics on the machine. Thanks to the addition of the specialty attachments, Oscar Orduno, Inc., offers the following services: engineered temporary systems, slope stability systems, wall remediation and failure repair, shotcrete applications, underpinning and specialty foundations, nonengineered erosion control and design/build retaining walls.
3. Excavator: Plate Compactor & Hydraulic Rotating Grapple
Matt Quinnell of Advanced Wall Structures in Prior Lake, Minnesota, builds approximately 60,000 to 70,000 square feet of dry-stone boulder walls per year. A critical part of the company’s success is compaction. Operators use excavators with plate compactors to ensure the ground is ready for the fabric that sits between the dirt and the boulders. Quinnell then uses a hydraulic rotating grapple on an excavator to select the right boulder and place it precisely into the wall. “People always joke with me that I play Tetris all day long,” Quinnell said. “But it’s an extreme form of Tetris with 5-ton rocks.”
4. Excavator: Breakers
Carolina Drilling does site preparation for projects where the soil is too rocky for simply using an excavator bucket. First, a drilling rig lets the team drive holes into the soil. Explosives are then carefully placed in the ground.
They detonate the explosives, and then a team of excavators comes in, including several with breakers. The breakers smash the boulders left after the blast into smaller chunks, which are cleared away by excavators with buckets.
5. Excavator: Shear
AMIX Recycling of Surrey, British Columbia, is a riverside scrap yard that offers marine vessel recycling among its many services. To scrap vessels, AMIX Recycling employees first remove surplus items from the craft and then use a large, onshore winch to pull the vessel out of the water and onto a bulkhead.
Once the vessel is pulled out of the water, an operator in a 53-metric ton excavator uses a hydraulic shear to cut it into four-by-two-foot pieces. Another operator in a material handler uses a grapple attachment to pick up the metal pieces the shear leaves behind and sort and stockpile them nearby.
Operators then use a material handler to load the pieces into a high-speed container loader, which moves the scrap into shipping containers. They then transload the containers of scrap onto trucks and send it to be recycled.
6. Excavator: Quick Coupler
Metro Equipment of Braintree, Massachusetts, has been doing site preparation and utility installation work in the Boston area for decades.
The company equips all its excavators with quick couplers to reduce time switching between breakers for demolition and buckets for excavation. Crews bring three different sizes of bucket with each excavator, so the operator has the right tool to get each part of the job done.
7. Excavator: Grapple
Brad Ziemke owns Ziemke Farm Fresh Produce in Zillah, Washington. He began offering orchard removal services to his friends and neighbors as a way to stay busy in winter. Using an old excavator and dozer, his crews removed blocks of fruit trees to make way for new tree varieties and planting practices.
The demand was so great that he now has four excavators equipped with grapples that he uses to extract trees.
“Our excavators can pull 4 to 8 acres a day, depending on the size of the trees and the terrain,” Ziemke said. “Pairing the excavator with a grapple attachment allows me to pick up and carry three times the amount that I had been.”
8. Excavator: Angle Tilt Bucket
Chad Mann, owner of Lloyd Collins Construction in Teeswater, Ontario, needed an angle tilt bucket for his excavator — for daily trenching, cleanup and to dig basements. Its 45-degree angle allows Mann and his operators to dig in tight areas, increasing his overall productivity.
“We depend on this bucket to perform well,” Mann said. “When using this attachment, we don’t have to worry that material will constantly be spilling out of the bucket.”
Mann also puts quick couplers on all his machines. “Our operators change buckets often, so by having the quick coupler they are able to change an attachment in 30 seconds or less,” Mann said. “It really allows us to be more productive and increase our jobsite versatility.”
9. Wheel Loader: Onboard Scales
Aggregate miner Central Texas Stone and Aggregate of Florence, Texas, installed onboard scales on its wheel loaders to increase production efficiency. The scales measure load weight lifted by the wheel loader bucket using sensors, transducers, Wi-Fi and GPS. The sensors and hydraulic pressure transducers are installed on the loader’s lifting arm mechanism of the bucket and send information to the operator, who has instant evidence that their estimates are close.
Since implementing the technology, the team at Central Texas Stone and Aggregate has cut over/under loads from eight in 100 to fewer than one in 100.
While some attachments may require a significant investment, others are less expensive and may offer a good opportunity to help expand your company’s services. But, before you make any moves, speak with your equipment dealer about investing in unconventional attachments. The dealer and the attachment vendor can collaborate to ensure the everything is installed correctly before you begin work with your new attachment.