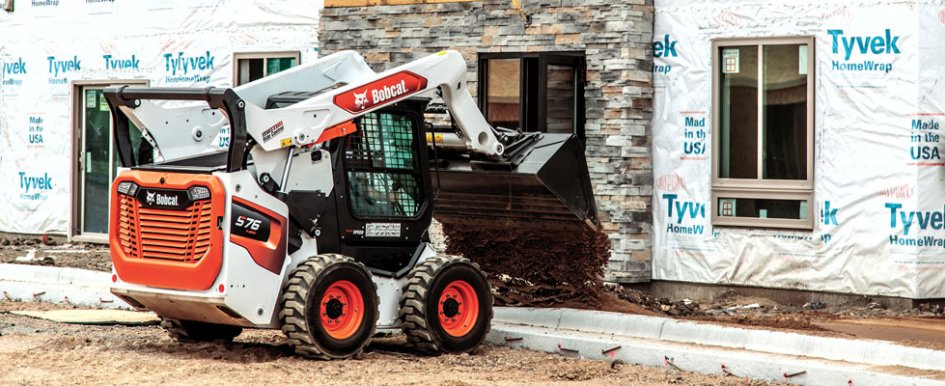
Rock, asphalt, sand or dirt. As a construction business owner, you and your equipment operators work in a variety of jobsite conditions. But how do you know what type of tire is best suited for your equipment and your specific application?
There are two major tire types—pneumatic or solid—that can tackle just about any project with ease. For instance, if you will be excavating, grading or performing other construction tasks, consider a pneumatic tire for superior traction.
If you will be working in demolition situations, consider a solid tire that will resist cutting and chunking caused by debris.
Depending on which option you choose, the right tire will help you get better performance out of your machine, reduce costly downtime and enhance your company’s profitability.
Pneumatic Tires
Pneumatic tires, which are made of rubber and inflated with air, are generally the best fit for construction applications. While they are vulnerable to punctures and flats, pneumatic tires provide better shock absorption and ride comfort than solid tires, especially when carrying heavy loads.
All pneumatic tires have a tire ply rating, which provides owners with a basis for how much load the tire is designed to carry at its industry-specified pressure. Here are some popular types of pneumatic loader tires:
- Standard-duty tires—When faced with general construction tasks, a standard-duty tire will be the best fit. These tires are designed for maximum traction and grip, feature thick sidewalls and are constructed with natural and synthetic rubber.
- Heavy-duty tires—These tires feature superior quality rubber, self-cleaning tread designs and a higher ply rating. To help protect rims and reduce sidewall damage, some heavy-duty tires also feature extra bead guarding. Additionally, these tires wear longer and are more resistant to flats compared to standard-duty tires, making them the ideal choice for rough jobsite applications.
- Severe-duty tires—Your tires should be reliable day in and day out in all applications. Severe-duty tires are aggressive, long-lasting and designed to take more abuse than conventional tires in some of the toughest applications. The deep tread depth and larger surface contact area significantly extend tire service life. Plus, stronger sidewalls protect against cuts and punctures, which can increase your equipment uptime.
- Turf and super-float tires—Turf and super-float tires offer better performance when maneuvering over existing lawns and soft or wet conditions. Both tire types have a design that provides 85% more footprint area when extra flotation is required.
Solid Tires
A solid rubber tire will provide the lowest operational cost on the harshest jobsites. Solid tires are designed to last approximately three times longer than pneumatic tires because they are made from special rubber compounds.
The tear strength on solid tires is more than double that of most pneumatic tires, which helps keep the tire intact when traveling over debris-filled applications.
Severe-duty solid tires feature an aggressive, off-road tread pattern for unmatched traction and self-cleaning action. Ideal for demolition, the large tread depth ensures great performance in severe applications. Additionally, severe-duty solid tires feature a conical aperture design, which improves ride quality and reduces vibration.
Extending Tire Life
The life of a pneumatic or solid tire depends on a variety of factors, but especially the application where it is used. For instance, you may get 1,000 to 1,200 hours of use on one set of tires when working on sand or very soft ground. However, when working on hard dirt, gravel or rock, you can expect between 600 to 800 hours of life. When working in severe operating conditions on only roads and parking lots, you may get 400 or less hours of life from tires.
Another factor to take into consideration is the initial purchase price. Many equipment tires look the same at a glance, but after researching and comparing brands, you will notice the difference. Industry-specific tires can have a higher initial cost, but they typically have thicker sidewalls (more rubber and the correct outside diameter) compared to off-brand and second-line tires. This feature affects bucket height-to-ground contact dimensions.
Educating yourself and your operators on steps to extend tire life will be beneficial to all parties. For example, when working on asphalt and concrete, it is better to make turns prior to traveling across the hard surface. Your operators should avoid spinning when digging and pushing.
When you outfit your machine with the right tire for the job, you can maximize your loader performance, reduce downtime and expand your business potential. By reaching out to your local equipment dealership for recommendations and to compare what tire best fits your application, you will find a tire that gives you superior traction, flotation, wear and overall performance.
5 Maintenance Tips to Maximize Tire Life
You’ve got the muscle. Now it’s time to make sure you are taking the right proactive measures to help extend the life of your tires. With these five tips, you can make the most of your tires and minimize maintenance costs and downtime.
1. Rotate tires—Keep an eye on the tires that have the potential to wear more quickly and make sure to rotate them regularly.
2. Transport equipment—When possible, transport your equipment by trailer to reduce the amount of wear and hours on the tires.
3. Consider the weight—Keeping your load balanced and being mindful of the weight you’re carrying will help maximize the life of your tire.
4. Monitor tire pressure—Routinely monitor tire pressure to make sure it’s at the recommended level. When a loader sits idle for months, especially during the winter, air slowly permeates through the rubber, causing the tires to lose air pressure. By assessing tire pressure each time your machine is in use, you can help save downtime and maintenance costs.
5. Regularly inspect your tires—You should inspect tires for signs of cracking or damaged tread and replace tires as needed.