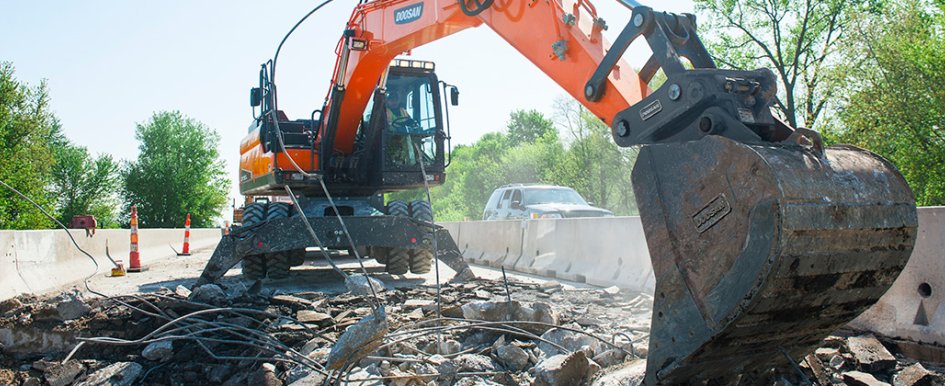
Are you aware that wheel excavators can perform in a variety of applications and maneuver in places deemed impossible for other types of heavy equipment? By looking at jobsite factors, key machine performance features and maintenance considerations, you can make a more informed decision on whether purchasing or renting a wheel excavator is the best solution for your business.
1. What type of excavator best matches the job site?
Before purchasing or renting a wheel excavator, it is best to first assess the scope of work. Will the machine you need be assigned to a single job or multiple jobs? Will the machine’s current jobsite tasks be the only work it performs during its entire lifetime in your fleet? Does the machine you choose need to accommodate any specific workspace constraints?
Wheel excavators are equipped with rubber tires, making them a popular choice when working on finished concrete or asphalt. These machines are often used in highway and street development, bridge construction, building and manufacturing operations, site development and land improvement. Other applications where wheel excavators work well include ditch-cleaning projects and underground utility installations.
Renting a wheel excavator may be a viable option if you need a machine for a single project or only a few times each year. However, you may commit to a long-term project that would be better served with an acquisition.
2. How about stability on a jobsite?
As a business owner, you may be asking yourself how exactly a wheel excavator can maintain its stability when used in heavy digging and lifting applications. Just as a crawler excavator relies on its undercarriage for stability, a wheel excavator relies on its tires, a dozer blade and outriggers, or four outriggers, for its stability in digging and lifting applications.
Wheel excavators can be equipped with a front dozer blade with two outriggers in the rear or four outriggers, two of which would replace the blade. The dozer blade can be used to replace a secondary machine when leveling or backfilling material, or when stabilizing the machine during digging applications. In addition, the blade’s large dozer bottom and parallel design minimize ground pressure. Outriggers can be individually controlled to level the machine on slopes.
As far as digging performance goes, both crawler and wheel excavators perform similarly. When the outriggers are down, wheel excavators have just as much stability as crawler models. This allows your wheel excavator operators to have lifting capacities similar to crawler excavators when working over the side.
3. How much mobility will be available?
If you need a machine that will deliver versatile, mobile performance and can travel quickly to the jobsite, a wheel excavator is the machine to add to your fleet. Because the excavators are equipped with wheels, there is less need to trailer the machine and move it when traveling short distances. The travel speed can be adjusted by selecting between three transmission speeds for increased productivity on a variety of jobsites.
For instance, operators strictly transporting the wheel excavator can select the high travel speed, which can reach up to 23 miles per hour (mph). However, if your operators are working on rough terrain or cleaning out ditches, they may choose to use a creep mode, which has a maximum speed of 2.5 mph.
In some cases, your operators will be working on jobsites where space is limited and will need to maneuver around several other machines. Wheel excavators are compact enough that they can efficiently work in one lane of traffic without closing down an entire section of highway or damaging existing infrastructure. In addition, wheel excavators have a two-piece, variable angle boom that bends in the middle, giving your operators optimal visibility to both sides of the machine and additional flexibility.
4. What maintenance considerations are there?
There are minimal wear items in a wheel excavator undercarriage. Operators should follow preventive maintenance schedules, including visually inspecting tire pressure, wear and damage on a regular basis. These are detailed in the owner’s operation and maintenance manual. A visual inspection will show if the tire has tread punctures or sidewall damage because of road hazards.
Also, look for rocks wedged in between dual tires, which can cause tire failure. Steel spacer rings have been added to prevent rocks from entering in between tires, but it is still important to visually check the tires before use.
Following a thorough preventive maintenance schedule can save you significant money by reducing downtime, which then improves productivity and profitability.
Although wheel excavators may have been seen as niche machines in the past, it might be time to look at them in a different light. Wheel excavators are versatile and well-suited for urban areas, mainly because the machine may be moved from one jobsite to the next without the need of a truck and trailer. Before you decide to add a wheel excavator to your fleet or as a rental unit, take time to evaluate jobsite conditions, key machine performance features, attachment versatility and maintenance considerations to make sure this machine is the right fit for your business.
Attachment Versatility
Often, operators have to be self-contained on the jobsite, and using a wheel excavator paired with the right set of attachments can fulfill those needs. The most common wheel excavator attachments include:
- Buckets (for trenching and grading)
- Grapple
- Hydraulic breaker
- Hydraulic clamp (also known as a thumb)
- Plate compactor
- Quick coupler
These attachments are compatible with wheel excavators for greater efficiency, economies of scale and justification to purchase. Some attachments have been designed to vertically integrate with the machine’s electronics and hydraulics.