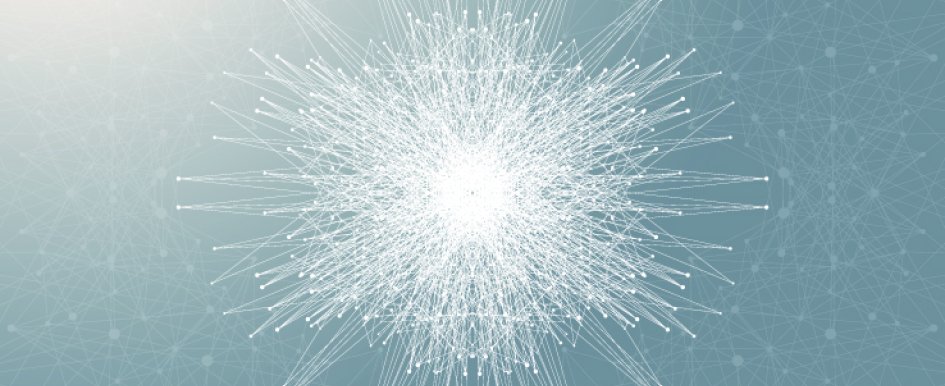
The growing demand for compact tracks loaders can primarily be attributed to the increased maneuverability and productivity that tracks can now provide. Compact track loaders are ideal for operating on soft soils, such as clay, mud or sand, and outfitting a compact track loader with the proper tracks for your worksite can improve machine performance, minimize ground disturbance and extend your working season in wet months.
Tracks can be wide or narrow, are designed with different tread patterns and can be nonmarking. However, before choosing a compact track loader, you should consider first whether tracks are the best choice for your jobs.
After much thought, if you decide that tracks are right for your projects, consider the following factors for selecting the ideal set of tracks.
Wide vs. Narrow Tracks
The wider the tracks of the loader, the less ground pressure the machine will exert because wide tracks distribute the loader’s weight over a greater surface area. Therefore, when minimizing ground disturbance on your jobsite is a priority—during landscaping or turf application work, for example—you should choose wider tracks. This will increase the loader’s flotation, making working on soft soils easier.
Narrower tracks are a good choice when traction or push force is the top priority for the job, and flotation is less of a concern. With narrow tracks, the loader’s weight is concentrated in a smaller surface area, which in turn increases ground pressure and traction. Choose narrow tracks when operating in slippery or icy conditions or when trying to maximize the loader’s push force on a firm surface.
Tread Patterns
Compact track loader manufacturers sell a variety of proprietary tread patterns, but there are four basic patterns that are common across all manufacturers: C-pattern, block-tread, straight-bar, multibar and nonmarking turf.
The C-pattern is the most versatile—good for a variety of applications. It offers a happy medium between loader traction and flotation. It creates less ground pressure than a straight-bar or multibar pattern and more ground pressure than a turf pattern. The C-pattern is a popular, do-it-all tread pattern that offers performance and operator comfort.
The block tread is one of the most popular options. This tread type works well on hard and abrasive surfaces like pavement or gravel. Additionally, the block tread operates smoothly on hard surfaces, causes minimal ground disturbance and is ideal for use on clay, sand, dirt, mud, gravel and asphalt.
A straight-bar pattern creates the highest ground pressure of the four patterns and is best used in work on surfaces requiring high traction. On hard surfaces, especially pavement, this pattern may cause the loader to vibrate and create an uncomfortable ride for the operator.
The multibar pattern provides greater ground pressure and traction than the C pattern, as well as a smoother ride on hard surfaces than the straight-bar pattern. So, if the loader operator needs high traction and is moving the loader between hard and soft surfaces frequently, such as in ice or snow, the multibar pattern is a good option.
Turf patterns create the least amount of ground pressure of all the track types and are a good tread choice for jobs in which minimizing ground disturbance is a top priority. The individual lug height on turf patterns is much lower than on the other patterns discussed, which reduces traction and minimizes the displacement of the ground material. This reduces the risk of damaging irrigation systems and underground utility lines when operating a loader.
Traditional compact loader tracks can leave black rubber marks when operating on concrete. If the loader operator is traveling across hard surfaces, such as concrete, driveways, sidewalks and parking lots where visibility is a concern, nonmarking tracks are a good choice. As such, they are especially helpful for landscaping and turf-maintenance uses.
Maintenance
While some compact track loader models automatically maintain track tension, the track tension of most current machines needs to be manually maintained. Owners and operators should consult the operation and maintenance manual to see how often the tension should be checked. Loose tracks can result in detracking and unplanned downtime. Tracks that are too tight reduce loader performance and can cause accelerated wear to the rollers, sprockets and drive motors.
Operator performance also affects the life of compact track loaders. While compact track loaders are nimble enough to turn within their own tracks, operators can minimize track wear by making three-point turns when possible.