Oil is one of the hardest-working fluids in compact equipment. As today’s equipment becomes increasingly sophisticated, oil must meet greater demands, requiring that you devote further attention to its role in your machine. However, the fundamental key to proper oil usage is matching the lubricant to the manufacturer’s model requirements.
With the Environmental Protection Agency’s various tiered phases of emissions regulations—specifically interim Tier 4 (iT4) and Tier 4—becoming more prevalent, the use of higher-grade engine lubricants is even more important for optimum performance. As you purchase new machines with engines that meet higher emissions ratings, you must use a better grade of oil. A benefit of the newer oils is that they’re compatible with earlier engine models.
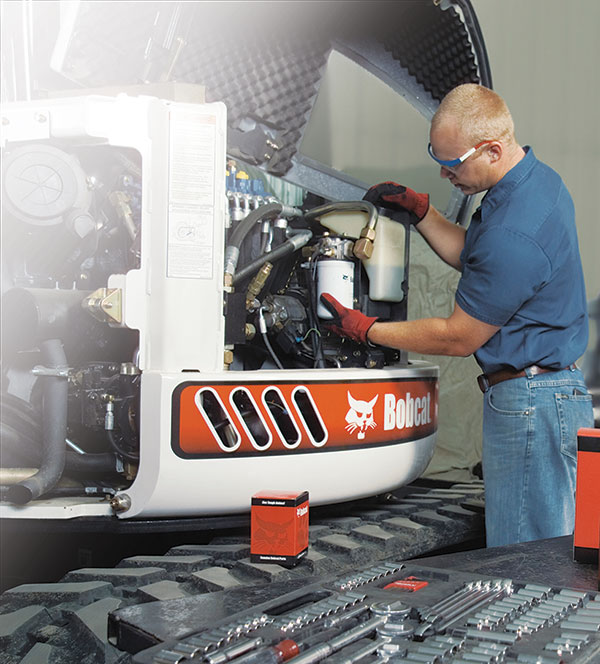
Similarly, advanced hydraulic and hydrostatic systems are running at higher pressures and flows, and performance requirements for this type of fluid also have been modified to ensure its stability for the life of service intervals. Different levels of grease are available to perform tasks as simple as greasing a machine’s pins and pivot points. The various formulations can contribute to extended service intervals or meet the needs of more severe-duty use or extreme-temperature environments.
Oil Classifications
The American Petroleum Institute (API) has developed a classification system that establishes the minimum specification requirements for engine oil. Oil categories for use in diesel engines begin with “C.” The API CJ-4 category was introduced in 2006 and is intended for high-speed, four-stroke diesel engines. It was designed to meet 2007 model year on- and off-highway exhaust emissions standards and is uniquely formulated to avoid impairing the durability of new diesel engine technologies. Those technologies typically include exhaust gas recirculation (EGR) and after-treatment systems with diesel particulate filters (DPFs) and diesel oxidation catalysts (DOCs).
API CJ-4 oils exceed the performance criteria of CI-4 PLUS and CH-4 oils, as well as key original equipment manufacturer (OEM) requirements for 2007 models or more current engines. Always use a premium oil that meets or exceeds the API service classification of CJ-4 for EPA-compliant engines.
Viscosity Matching
Matching the viscosity rating of your engine oil to the outside temperatures at your work environment is also important. The Society of Automotive Engineers (SAE) establishes viscosity specifications. Always refer to your operation and maintenance manual to determine the weight of oil that is recommended in various conditions.
A 10W-30 weight oil is a common factory-fill for many current production machines. It offers top performance in temperatures ranging from minus 20 degrees Fahrenheit (F) to 90 F. A 15W-40 weight performs well from minus 5 F to 110 F.
Synthetic or synthetic blended oils are formulated with additives that can extend oil-change intervals and promote longer engine life. These oils have better cold-weather starting and lubricating performance, as well as additional wear protection during severe high-speed, high-temperature operation. For instance, a 5W-40 weight synthetic oil is usually capable of providing protection in harsh conditions as cold as minus 40 F and as hot as 120 F.
Hydraulic and Hydrostatic Oils
Hydraulic/hydrostatic oils are formulated to meet the growing demands placed on hydraulic components, and several different types of these fluids can be used for varying applications:
- High performance — Typically, a custom blend of high-quality lubricants designed to provide peak flow at subzero temperatures while maintaining stability during periods of high-temperature use.
- Synthetic — An advanced liquid technology designed to optimize cycle times and productivity and provide good cold-weather fluidity for seasonal changes.
- Biodegradable — Introduced to meet customer demand as federal, state and local governments set environmental-related project restrictions. It’s biodegradable, nontoxic and formulated to reduce the potential for environmental damage.
Grease
Many machines require grease as a lubricant in pivot points where pins and bushings are located. The lubrication points must have grease added at various intervals specified by the machine manufacturer. If used correctly, the right type of grease will extend the life of components. Various types of grease are available as classified by the National Lubricating Grease Institute (NLGI), and their different properties should be properly matched to your application:
- Multipurpose #2 — Developed for normal applications, it provides lubrication to prevent rust and corrosion and protection under heavy and shock loads.
- Heavy duty — Containing moly for better adherence to all surfaces, it offers water resistance, extreme pressure capabilities, pump ability in cold temperatures and good seal compatibility.
- High performance/synthetic — Formulated to provide high- and low-temperature performance in severe operating conditions, it’s intended for lube points with sliding and pivoting movements.
Oil Analysis
With the additional demands placed on engines and hydraulic and hydrostatic oil, you may want to further enhance preventive maintenance efforts with an oil analysis program. A comprehensive evaluation of oils with an accredited laboratory can help you more effectively monitor the internal operating conditions of your equipment. The practice of regularly sampling and monitoring test data can generate trends during an extended period of time and detect any potential problems with your equipment, including the presence of ferrous particles, the existence of wear and other contaminants and fluid cleanliness.
Your equipment manufacturer’s maintenance recommendations can provide a guideline for developing preventive practices, but sampling oils can easily vary service schedules. Factors such as how critical a piece of equipment is to production—along with environmental factors such as hot, dirty operating conditions; short trips with heavy loads; and excessive idle times—can affect oil-change frequency. Oil analysis is most effective when samples are taken at regular intervals.
Making educated oil usage decisions and adopting good monitoring practices can help improve your productivity and increase machine longevity.