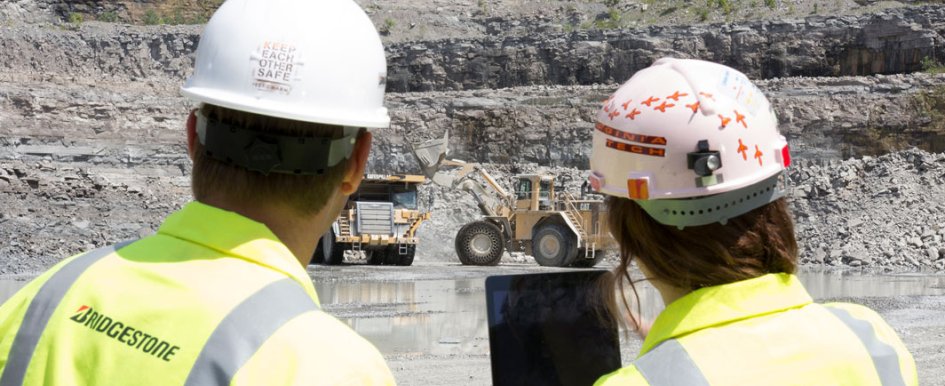
We don’t get far without them, and neither does the progress of a construction project. They are a big contributor to production on every jobsite and are, quite literally, the things that keep everything moving. They are not your employees or your equipment: they’re your tires. And, whether we acknowledge it or not, the safety of our teams and projects greatly depend on the tires we take to the jobsite every day.
One major name in the tire market is Bridgestone Americas Inc., manufacturer of tire and rubber products. Bridgestone has more than 180 manufacturing plants and research and development (R&D) facilities in 26 countries, and sells products in more than 150 countries worldwide.
Rob Seibert is the director, marketing, off-the-road (OTR) tires, commercial group, at Bridgestone Americas Tire Operations (BATO), where he leads all marketing research, planning and execution for Bridgestone’s OTR tires in North America. Seibert also manages the strategy development and execution of special projects aimed at advancing the organization’s OTR solutions offerings, some of which promote jobsite safety through technological solutions. CBO sat down with Seibert to talk tires, technology and the direction of jobsite safety. Read on for his insights.
CBO: Why is regularly inspecting and monitoring tires important for construction safety?
RS: Proactive tire maintenance is key for OTR fleets to keep their operations productive on jobsites. It helps ensure optimal performance and mitigate tire-related events that can lead to unwarranted repairs, downtime and labor costs. For example, under-inflation, overloading and over-speeding can lead to irreversible wear, and productivity and profitability can be hindered through downtime.
For these reasons, technology has become an integral part of tracking and managing tires on the jobsite. From monitoring real-time tire pressure and temperature to sharing key insights for maintenance, the incorporation of new technologies within jobsite operations is becoming an industry best practice.
CBO: What does proper tire maintenance and management look like on a construction jobsite?
RS:The rough terrain and rigorous conditions of the construction jobsite provide everyday challenges for tires, which can lead to tire damage and result in unplanned downtime, negatively affecting jobsite productivity. Just like your personal vehicle, construction equipment, loaders and articulated trucks require attention and upkeep, such as wheel alignment, tire rotation, tire-pressure management and inspection. Bridgestone recommends these four best practices to ensure your tires continue to live up to the job and contribute to a more secure workplace.
1. Select the right tire —This is the first and most crucial step of any tire program. Not matching the appropriate tire to the application can compromise tire performance, machine traction and safety. It is important to take into consideration the type of application, environment, necessary loading capacity and speed ranges. Additionally, tread patterns, casing design and compounding allow tire manufacturers to engineer products tailored to customer needs, including traction, stability, treadwear and heat resistance.
2.Work with tire experts —While daily inspections identify issues early on, trusted dealer partners play a significant role in ongoing maintenance and management. Operators should call their dealer as soon as an issue is identified, allowing the dealer to help address the issue immediately. As the tire expert, a dealer can help manage a tire program to ensure the right tire is selected and then address potential issues before they impact operations.
3. Maintain air pressure —Low tire pressure can increase stress on tire components and is caused by factors, such as not following tire manufacturers’ cold inflation pressure recommendations, using pressure gauges that are out of calibration, having leaking valves and bad wheel components. Operators and site managers often aren’t checking tire inflation pressure frequently enough. This is where a tire pressure monitoring system (TPMS) can really help to provide real-time tire-pressure information.
4. Make inspections part of everyday operations —Equipment operators should also know how to conduct pre-shift tire and equipment visual inspections to identify problematic wear and tear between professional inspections. Hazardous tire indicators, such as irregular wear, mismatched tread depths, cuts, cracks, bulges or penetrations can be tied to larger maintenance issues or improper tire pressure. These quick, daily checks can make a big difference. By identifying issues early on, operators are able to avoid unplanned downtime.
CBO: How do tire management technologies impact maintenance programs and enhance jobsite safety?
RS:In addition to pre-shift inspections, many construction companies are integrating technologies into their day-to-day jobsite operations to improve safety, productivity and efficiency. Data-driven tire tools enable more accurate maintenance inspections and more timely identification of potential problems that are contributing to asset performance and jobsite safety.
TPMS is an example of how technology is improving a formerly time-intensive process with real-time data and analytics to make inspections faster, easier and more accurate. Wireless, in-cab systems supply instantaneous inflation pressure and temperature data to drivers, signaling if a change needs to be made in loading weight, inflation pressure or driving speed.
The technology also provides more accurate readings and measurements on these metrics, decreasing the room for human error. For example, the Bridgestone PressureStat system provides instantaneous tire pressure and temperature data as well as wireless, in-cab system updates. This particular tool can also be integrated with the Bridgestone TreadStat system, a cloud-based tire and rim tracking software platform that allows end users to forecast tire needs and track against their inventory based on real-time tire performance and condition.
These technologies can help business owners improve their operations by maximizing safety and productivity and minimizing the total cost of ownership. Working with a trusted dealer who offers these types of resources is a great way for construction equipment owners to apply today’s tire technologies to their business in a practical and impactful way.
CBO: Will new tire technologies eliminate the need for manual tire inspections altogether?
RS:Intelligent technologies are transforming the world around us, and the construction industry is no exception. The industry is moving toward a sensor-based monitoring and reporting model for real-time updates to maximize jobsite safety and productivity. It will continue to modernize inspections and monitoring.
Further, hands-on coaching and encouragement from both project leadership and tire professionals will allow operators to be well-informed and involved, building a stronger culture of safety one shift at a time.
CBO: Is there anything else you would like to add?
RS:Remember: Intelligent tire management technologies can help owner operators improve jobsite safety by providing real-time data that allows for critical operational adjustments.
However, they can never replace a hands-on tire inspection. Pre-shift diligence, along with intelligent tire management technologies, work best together to help maximize uptime and performance.
Construction applications take place in tough environments that affect tires, and it is important to be proactive in your company’s tire maintenance to help safeguard against detrimental tire conditions that can impact equipment and, most importantly, people.
Visit Bridgestone’s website at commercial.bridgestone.com/en-us/otr-tire-inspection to learn more about daily inspection best practices and to get a Pre-Shift Tire Inspection poster for your jobsite.