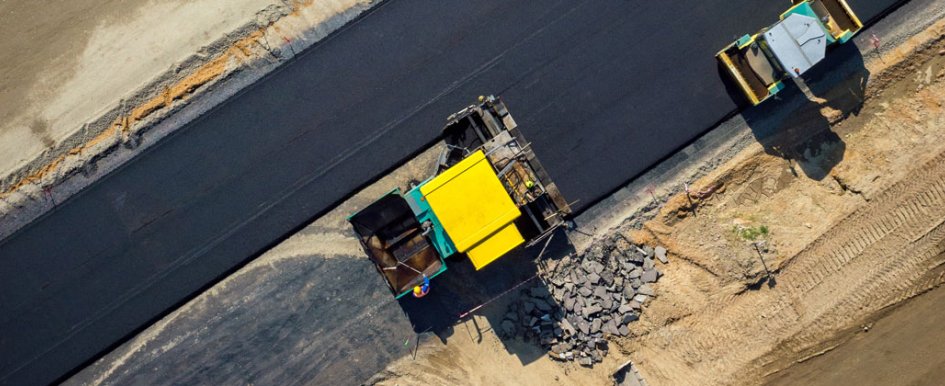
Autonomous cars will soon be a regular feature of American highways. The nation’s farmers, suffering from years of agricultural labor shortages, are banking on manufacturers developing robot swarms to make planting and harvesting cheaper and more efficient. Mining companies have already been employing autonomous trucks in various parts of the globe.
Al Cevero, senior vice president, construction, mining and utility for the Association of Equipment Manufacturers (AEM), believes the construction industry will routinely see autonomous equipment operating on jobsites as well—within in 5 years or less.
The Labor Shortage Continues
Now that the development of a variety of autonomous construction vehicles is underway, the speed with which adoption will occur will surprise no one familiar with the difficulty of finding and hiring skilled tradespeople.
With two-thirds of contractors reporting an inability to find sufficient skilled workers for their projects, automation isn’t about labor cost savings—at least that’s not the first-level benefit. First and foremost, contractors just want to be able to manage the overwhelming workload and wait list most of them already face. And they’re going to have to start leveraging technology to do it.
In a recent Software Advice survey of construction managers, 32 percent of respondents indicated they were employing or planning to soon employ technology to address labor shortage issues.
According to the Construction Intelligence Center’s Global Construction Outlook 2020, given the global construction industry generates $10 trillion per year in revenue, the opportunities for increased efficiencies, cost savings and higher productivity, with the help of technology, are boundless. While automation has decimated jobs in sectors like automobile manufacturing, construction workers need not fear with numbers already so small relative to the need.
“The workforce will be shifting, yes,” says Cevero, noting that today’s equipment operators will gradually slide into new roles, whether it be helping to design the layout of a construction site and how vehicles will operate within it or programming that equipment to follow certain rules of operation. “The pace will be slow enough that the change in the marketplace for jobs will be a positive one,” said Cevero. “I think, if anything, it’s going to elevate people.”
Where Construction Is Behind the Curve
The construction industry has been recognized for being behind the curve when it comes to employing new technologies and techniques. While driverless cars are already a reality (legal in 22 states and the District of Columbia, possibly available for consumer purchase as early as 2021) autonomous vehicles and equipment in the United States construction industry are just now hitting their stride.
Autonomous equipment, for example, the massive Komatsu-manufactured dump truck, has become the norm on many mining sites, particularly in Australia. In fact, global mining firm Rio Tinto has been using Komatsu autonomous trucks for hauling ore in western Australia since 2015. These vehicles and others like them are already providing modeling for the construction industry, and other manufacturers like Caterpillar are being forced to follow suit.
Many major equipment manufacturers, along with some industry newcomers, have released, or are in the process of developing, various pieces of autonomous equipment. Some of the latest developments for the construction market include:
- Driverless excavators and bulldozers (already successfully working on California jobsites) from Built Robotics, a company founded by a former Google engineer
- The Semi-Automated Mason (SAM), which can lay 3,000 bricks in an 8-hour shift, from New York-based Construction Robotics
- An autonomous quadcopter from Kespry, out of Silicon Valley, that is capable of surveying a building site in minutes, compared to the day or more it would take a human surveyor
- Prototypes of an autonomous wheel loader and an articulated hauler being developed by Volvo
According to a recent survey from JBKnowledge, almost half of construction managers spend less than 1 percent of their budget on information technology (IT), and only 49.6 percent have dedicated IT staff. But that’s going to change, and it will likely happen quickly. Contractors will be forced to keep pace with technology to remain competitive in a market where labor shortages are the norm.
Autonomous equipment using real-time kinematic (RTK) is already active on mining sites. “The use of this equipment in urban and residential areas will require very high safety standards,” says Akshay Bandiwdekar, director of product at Area 17, a software company that provides navigation information to machines. “Part of what drives safety is location. GPS shows you where you are but doesn’t tell you anything about what’s around you.” That’s changing, too, according to Bandiwdekar. “In the future, the truck will both know where it is and what’s around it.” Another advancement: “Machines have been working independently, but in the future, a truck and bulldozer would work in tandem.” He estimates this will begin in as few as 5 to 8 years.
Why Automation Makes Sense
Safety
Construction workers have the highest rates of injury among workers in any other U.S. industry—nearly 170 injuries per year per 10,000 workers, according to a study published by the National Center for Biotechnology Information. Most could be avoided with autonomous equipment. Driverless vehicles, or those operated remotely, can put workers out of harm’s way on jobsites. They also reduce work injuries related to repetitive tasks, wear and tear on the body from daily operation of off-road vehicles for long hours, as well as the effects of constant exposure to loud noise, dust and vehicle vibrations.
If you’re concerned that autonomous dump trucks and bulldozers could run over your workers, keep in mind they are outfitted with a variety of safety features to prevent this, including lidar, an obstacle-detection feature that prevents equipment from injuring humans or damaging objects on the jobsite, and a geofence that defines the precise perimeter in which an autonomous vehicle can operate.
Reduced Labor Costs
“There’s always going to be a need for actual humans on jobsites to make decisions,” said Dan Taylor, content analyst for Software Advice, “but the industry is on a trend, trying to replace as many workers as possible.” He says if the cost is reasonable, contractors will buy autonomous machines as opposed to the expense and risk of hiring a worker. Cost is the kicker, though. “A lot of small and midsized businesses will find it tough to make a case [for autonomous equipment],” Taylor said. And that’s not just because of cost; it’s also because of the learning curve associated with integrating the technology on the jobsite.
That being said, drones offer a low cost of entry into autonomous equipment. They can provide land surveys, map a jobsite and assess site safety in minutes. Manufacturers are aware of the cost hurdles smaller businesses will face. AEM’s Cevero posits that, as with the autonomous agricultural equipment industry, cost awareness will ultimately drive the need for smaller, less expensive options like robot swarms.
Productivity
The biggest cost and efficiency gains of autonomous equipment for contractors, however, will be increased productivity. “[Autonomous equipment] drives productivity by reducing wasted time and cost,” said Bandiwdekar. “Right now, construction only takes place when you have labor.”
Autonomous equipment can work 24 hours a day, 7 days a week. Unlike human equipment operators, driverless vehicles and equipment don’t need sleep, rest or vacations. Thus, contractors who use autonomous equipment will likely see substantial increases in how quickly they can complete projects.
In fact, a recent McKinsey & Company report indicates the slow-to-adopt construction industry could improve productivity by up to 60 percent if it instituted more innovation and improved technologies, including autonomous equipment.
Operational Efficiency
Along with being able to operate at all hours of the day, autonomous equipment is typically outfitted with a variety of sensors that alert human remote operators or supervisors if there are maintenance needs on the vehicle. This monitoring of vehicle health prevents bigger and often expensive breakdown issues from occurring. Autonomous equipment is also programmed to operate at maximum fuel efficiency and optimize its speed to meet the specific demands of the jobsite, with much greater accuracy than a human could.
Construction Labor Needs Won’t Go Away
Construction workers worried for the safety of their jobs in this new era of automation need not fear. Not only will the lack of supply for the demand of workers likely continue, but autonomous equipment will still need human supervision and intervention. Humans will need to provide the machine with the right inputs for getting the job done and be able to take over if a machine error or failure occurs.
Plus, workers will always be necessary for finer skills. A driverless excavator may be able to prep a jobsite, and even do some of the final grading, but human laborers will still be required for detailed work, finishing touches and tasks in high-traffic areas or places where automated equipment can’t safely maneuver around obstacles.
Autonomous construction equipment will ultimately free human workers from dangerous, repetitive and monotonous work while allowing them to focus on highly skilled tasks that require more finesse. Of course, autonomous equipment isn’t cheap, even though newcomers to the equipment industry have already begun to retrofit existing vehicles for driverless operation. Cost will prevent many contractors from switching out human-operated equipment on a grand scale anytime soon. But, as with driverless cars, the future is coming, and it’s coming quickly.
Virtual Training
For now, most construction jobsite equipment, apart from drones and demolition robots, still requires human operators. But the way those operators receive training has shifted substantially, thanks to augmented reality (AR) and virtual reality (VR).
Today, apprentices can learn how to operate everything from bulldozers to wheel loaders, using simulators that replicate not only the vehicle itself, but also the conditions of a jobsite. One of the key advantages is that trainees aren’t taking production time from real equipment to learn the ropes.
Simulators can also provide trainees with feedback on their performance—how well they changed gears, made efficient use of fuel and moved objects around the construction site.
However, Cevero, of AEM, points out that simulators can’t entirely replicate the jobsite experience, such as the feel of hitting rocks or operating at odd angles, How equipment feels is a big part of the training process, and right now, that can only be achieved on-site, he says. But even that is coming soon.